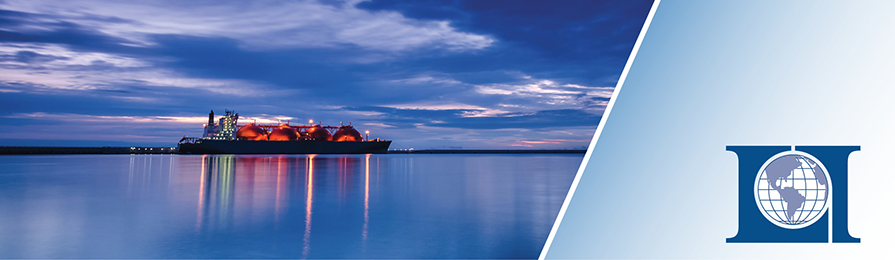
Claims Management Challenges in the “Modularized” Project Execution Environment
As modular design enters a new phase, focused on modularizing conceptual design itself, we must address the unique challenges that modular execution environments have created for claims management and dispute resolution. This article reviews some of these challenges and suggests solutions.
1. INTRODUCTION
The author first encountered modular construction in a project claim management context in 2001 while working on a claim arising from the first use of prefabricated modular units for a school expansion project in New York. Fabrication of the modular components was locally sourced in New York and the modules were transported by truck. Industry-wide understanding of modular execution environments and their role in complex construction projects has changed considerably since 2001. Yet the impact of offshored module fabrications on project execution and claims management has not been heavily scrutinized.
At the Construction SuperConference in San Diego, on December 8, 2015, a panel of distinguished professionals agreed that modular construction is indeed on the rise. Sue Klawans, Vice President and Corporate Director of Operational Excellence and Planning at Gilbane Building Company, presented some interesting applications of the modular concept to utilities risers placed in stackable vertical shafts. In a November 12, 2015, interview with Angus W. Stocking, Ms. Klawans however acknowledged that for U.S. projects, modular execution environments still have long way to go: “In terms of prefabrication and construction adoption, I’d say we’re still in elementary or maybe middle school in the the United States.”1
Worldwide, the infrastructure and oil and gas sectors have pioneered the application of modular construction techniques to incrementally larger mega-projects. But large-scale application of modular construction to U.S. apartment building projects has not yet been seen. The New York Atlantic Yards apartment tower known as B2, officially launched in 2012 with high hopes that it would be a flagship modular project, has experienced design and execution problems. Modular builders in the United States have been more successful with low-rise structures, including retail facilities, hotels, and other all-micro-unit buildings. Again for a project in New York, Capsys Corp’s 55 modular units were built in less than a year and stacked in four weeks. The Capsys project proved the first rule of modular construction: modular methods can indeed reduce costs and improve completion time. Capsys Corp then, however, discovered the second rule of modular construction: modules don’t have to be constructed locally. Portability is part of modular construction technique’s appeal: module construction can be offshored for convenience, cost-saving, or access to skilled labor or production capacity. Capsys Corp has been acquired by Whitley Manufacturing. And Polcom Modular, a Polish modular construction firm, now supplies modules to the U.S. East Coast market more cheaply than closer U.S. manufacturers, such as Pennsylvania‑based Deluxe Building Systems.
Leveraging the portability factor – the opportunity to offshore modular construction – has been a key factor in the oil and gas industry’s early embrace of modular design. And in turn, as modularization has progressively allowed energy projects to break limits formerly posed by local logistical constraints, the projects themselves have grown larger and more complex. We can, at this point, suggest that offshored module fabrication has increasingly fragmented rather than “modularized” project execution. This failed modularization of project execution results from a lack of sustained attention to the very interface issues that are now the priority in modular design. Relying solely on Engineering, Procurement, and Construction Management (EPCM) contracts as the glue for a project execution team fragmented across geographical areas, legal jurisdictions, system deliveries, contract frameworks, and delivery packages is equivalent to applying Building Information Modeling (BIM) to modular design – BIM is just a design tool, not a substitute for interface design management. As energy projects have grown increasingly complex, much attention has been paid to improving decision-making processes, but less to assessing the systemic delivery risks associated with the increasing fragmentation of project teams – or to developing strategies to mitigate those risks.
As modular construction design enters a new phase, focused on modularizing conceptual design itself, we must thus recognize and immediately address the unique challenges that it has created for project claim management and dispute resolution. As co-users of project controls data, claims managers have a critical role to play in the design and implementation of project-wide data management strategies. The purpose of this article is to review some of these challenges, and to suggest solutions that may be applicable not only to multibillion-dollar gas liquefaction projects in the northern shores of Ural, but also, closer to home, in the burgeoning modular building industry.
2. THE INCOMPLETE MODULAR CONSTRUCTION DESIGN REVOLUTION
Modular construction has been a feature of new plant construction for heavy industry for over thirty years. Many projects are now realizing the productivity and labor benefits of offsite fabrication, but we have not yet seen a widespread revolution in the way modularization is transferred from plant design to construction management processes. In the world of modular methods, the focus on design improvement has been narrowed to the point that the term “modular execution” now often refers exclusively to design execution rather than project execution. Growing systemic risks lies in the ongoing disconnect between, on the one hand, increasingly sophisticated supply chain and design processes, and, on the other hand, a project delivery framework that has not yet systematically embraced the data and analytics (r)evolution.
While modularization is not new, the level of achievable offsite work was significantly increased late in the 20th century via adoption of module-centric design, procurement, and delivery strategies. First-generation modular, similar to Gilbane’s main piperacks and pre-assembled racks (PARs), has been successfully deployed by the oil and gas industry since the early 1990s. Energy companies have benefited through reduced quantities, productivity gains for work shifted to shop, and reduced costs for field labor, at a scale far greater than is currently being seen in the building industry. The modules have ranged, based on project size requirements and logistics, from the early truckable skid-mounted equipment modules – mounting a number of separate equipment components on a common base frame skid – to more recent ship-mounted modules for Floating Production, Storage and Offloading (FPSO), Floating Storage and Offloading (FSO) and Floating Liquefied Natural Gas (FLNG) vessels.
With the development of integrated design management tools (e.g., BIM), modularization entered into an incremental second generation phase in the 2000’s. The same building-block approach was applied to more complicated mechanical elements with equipment on modules or pre-assembled units and pre-dressed vessels – pipes, equipment, and steel on a skid. This approach is reported to have reduced field work by 30% to 40% and transferred the associated risks to the controlled environment of fabrication yards. As projects became more dependent on specialized module fabricators, transportation risks became a key focus of both academic and industry studies. Although the controlled environment of fabrication yards decreased construction risks (weather delays, productivity, defective works), the systemic risks associated with greater reliance on offshored manufacturers and suppliers increased. The claims management function, however, remained site-focused; it was and is generally staffed long after the start of site works and long after the award of contracts for offshored modules manufacturing. Key pre-award project management functions that impact post-award claims management and dispute resolution – organizational design, project data modeling and data management frameworks – are not handled by end-users, if are at all systematically addressed.
In response to the recession of 2008–2009, engineering companies such as Fluor and CB&I have further pushed design-process boundaries for optimizing modularization. Prior to this phase, modules weren’t originally designed for “modularity” per se, but for offsite fabrication. Only 20% of electrical and instruments were on modules. Installation of controls, electrical cabling and module testing and pre-commissioning were still done on site. Fit and interface was still very complex, with a large number of interconnections between modules – the modules were just sections of systems rather than modularized parts.
Hence, the third generation phase made modularization a core conceptual design execution principle – with modularization driving the process block layout rather than layout driving modularization. The improved design execution model splits the project into process blocks and moves into designing modules that then drive the design and construction of facilities. The design process starts with process engineers who conceptually divide the project into various process blocks (systems within a distinct geographical boundary). In a typical post-2010 project, 95% of piping, 85% of electrical, and 95% of instruments are on modules. Pre-commissioning testing is completed at the yard. Interconnection is plug and play with only final loop checks done at site. This approach could result in up to 60% reductions in facility plot space requirements, 90% of field hours relocated to module yards, and 20% in capital cost savings for all types of plant construction.2
The oil industry has gained substantial advantages from this modular-centric “design” execution approach, including reducing some bulk material quantities through the optimization of module layout and better integration of controls,3 and maximizing the transfer of labor hours from a low‑efficiency and high-cost field environment to higher-efficiency and lower-cost module fabrication yards. Modular design execution can also offer greater planning predictability and significant capital cost savings when at least some of the following project conditions exist:
- Remote site location
- Extreme weather conditions
- Short supply of local skilled craft labor
- Short supply of construction equipment and small tools
- Greater labor efficiency or lower labor rates at an outside fabrication yard
- Suitable transportation, receiving, and handling facilities available for modules
This third phase of modularization has not yet, however, made modularization a core project execution principle. Modularization-driven fragmentation of the project management function, and its associated risks, remains the norm. Some projects are more susceptible than others to this trend and would, therefore, benefit most from a systematic mitigation approach. The Yamal LNG project in Russia, which is discussed further below, is a prime example of the potential advantages of modular design implementation. It also exemplifies the inherent project execution risks. When every component of a project, from supply barges to tankers, must be custom built to handle that project’s unique conditions, the multiplication of concurrent critical paths leading through first gas and commercial operations can become overwhelming.
In the absence of a systemic, project-wide approach to project controls and dispute avoidance and resolution (and associated functions such as lean manufacturing operation improvement, risk assurance, and internal audit), the risks associated with offshored fabrication and project fragmentation can compound to the point of becoming unmanageable. More often than not, these risks develop in an undocumented manner outside the limited reach of project claims managers.
3. GROWING FRAGMENTATION OF THE PROJECT DELIVERY ENVIRONMENT
The move to modularization is driven by world trends in the resource extraction industries – as easy raw material finds deplete, and new projects grow increasingly remote, modular construction shifts some of the burden away from high-cost and often environmentally sensitive locations. Fabrication yards, whether self-managed by large design firms or locally owned, are now strategically located around the world to support modular engineering and construction projects – in Batangas, Philippines; Batam, Indonesia; Alberta, Canada; Sakhalin Island, Russia; Tampico, Mexico; Zhuhai, China; and Okpo, South Korea, to name a few. The oil industry has been subject to the same constraints that are now shaping New York’s micro-unit modular fabrication market. When modularized, design and construction can be outsourced to the lowest bidder, irrespective of location. The delocalized construction of plant components, initially developed to solve problems specific to offshore field development projects, is now becoming the rule for almost all process and infrastructure projects, whether an LNG plant in the Ural or a coal export terminal in Australia.
Modularization is not just a manufacturing concept. As previously discussed, it has changed the way projects are delivered. As owner teams across the world have been experiencing: “The design of the modules themselves, while very important, is just one component. The key point is the execution of the project.”4 Yet modular execution methodologies have remained confined to engineering and supply chain management (with heavy borrowing from lean manufacturing), not project execution. Currently missing – though perhaps soon to be addressed as modular construction enters its fourth generation – is an integrated engineering, procurement, fabrication and construction (EPFC) management paradigm that embraces modularization and mitigates the new challenges inherent to offshored manufacturing and project delivery fragmentation.
This fourth revolution seems to still be in its infancy. Large engineering and EPCM contractors such as CB&I and Fluor seem to have pursued organic solutions, i.e., they have developed in‑house manufacturing and fabrication capabilities in close proximity to key production centers. While this integrated approach partially remediates project fragmentation, it undermines the economic incentives associated with modularization, e.g., offshoring to the lowest responsible bidder – an increasingly project-critical imperative for delivering economically viable processing facilities under challenging market conditions. Bechtel used a hybrid approach for delivering its three Australian mega-projects – third-party fabrication yards were chosen through a tender process, but the fabrication process was closely managed by Bechtel. These delivery models are not widely discussed. At industry conferences, we still see modular execution equated with engineering and transportation – execution models, project data modeling, data collection frameworks (IP pass-through clauses), change management, and dispute resolution remain afterthoughts.5
A cursory review of scholarly articles and industry resources suggests that research gravitates around two key subjects: design process interactions and supply chain management. The most accurate diagnosis of the impact of project fragmentation can be found in the field of information technology, rather than project management. A growing interest in the promise of data interoperability has arisen from three unrelated areas – information technology, asset management,6 and lean manufacturing (lean project delivery puts a renewed emphasis on data modeling and data ownership issues).7
These isolated fields have not yet converged to form a unified modular execution model that addresses and mitigates project fragmentation.
Academic literature on IT fragmentation properly diagnoses the tension between fragmented and unusable data models and the management tasks they are supposed to inform. This situation, common to the construction industry as a whole, has been exacerbated by the offshoring of construction through modularization: current construction management evolves in “information islands” with no long-term data management strategy, leading to the generation of data sets with limited interoperability. In addition to data integration issues, the voluminous data generated does not support all project functions; i.e., it is not maintained based on a central data model that accounts for all possible uses or users of data subsets (e.g., manpower data structured for productivity, safety, accounting, and progress reporting). The IT fragmentation studies call for a new class of software environment – not a new project management paradigm for supporting such a data aggregation model.8
Project claim management, a function heavily dependent on access to and integration of multiple data sets (e.g. engineering, site project management, planning, quantity surveying), has traditionally been managed by site project management teams where knowledge management happens organically; this organic model is now challenged by construction offshoring subject to language, organizational, geographic, contractual, and legal barriers. In many cases, the complexity of modular construction design projects has outgrown the traditional approach to claims management. The scope of these challenges can be illustrated by the LNG plant currently being built by JSC Yamal LNG on Yamal Peninsula, located in the Yamal-Nenets autonomous district of northwest Siberia, Russia.
The Yamal LNG plant is an ideal case for modularization: situated in a low-efficiency and high‑cost field environment, on inherently fragile terrain. The peninsula extends 700 kilometers to reach the Gulf of Ob to the east and Kara Sea and Baydaratskaya Bay to the west. The peninsula’s terrain is mostly permafrost ground, with subsoil permanently frozen and temperatures averaging –13°C (in the winter, temperatures can drop to -50°C). In the vernacular Nenet language, Yamal means “End of the World.” Off-site modular construction can easily reduce labor costs, reduce material quantities, and reduce environmental impact. As a result, the construction of Yamal LNG is now taking place, concurrently, on three continents.
The Yamal LNG plant will process gas resources produced from the onshore South Tambeyskoye Gas Condensate Field. The complex construction project includes a modularized integrated LNG complex, as well as associated storage and off-loading facilities for LNG and gas condensate. The field development plan involves 208 directional production wells, to be drilled from 19 well pads. In support of these key structures, the project also encompasses power generation and transport infrastructure, including a new, strategic Arctic seaport and an airport. The first stages (the seaport, plus one of an eventual three trains) are planned to be operational by the end of 2017, and commissioning of the completed plant is expected in 2021. The project is budgeted for US$27 billion, and will involve about 15,000 people on-site at the peak of construction.
The project has involved seven different engineering firms, based in Europe, Japan, and North America. The initial FEED development team for Yamal included CB&I, Chiyoda and Saipem. FEED was completed in 2012, natural gas treatment technology was licensed from BASF in mid‑2012, and construction of the liquefaction plant was fully sanctioned in March 2013. In April 2013, an early engagement EPC contract was awarded to Yamgas, a consortium of Technip, JGC Corporation, and Chiyoda; Technip’s operating center in Paris, France, was to execute the project. Technip firmed up its project execution plan with a handover date for the first train planned for 2017. An EPCM contract for the complete project was then awarded to Technip’s consortium in April 2014. The scope of work consists of a fixed-priced package for engineering, procurement, and module fabrication, and a cost-reimbursable package for site construction and project management.
A fabrication contract for the main process modules was awarded to Philippines-based Atlantic Gulf & Pacific Company (AG&P) in October 2014. The modularized design of the plant requires four new-built transportation vessels, for which the construction contract was awarded to Netherlands-based BigRoll Shipping. The BigRoll Barentsz, the first of four vessels under construction, was launched at Cosco Dalian Shipyard at the end of October 2015, with delivery expected in March 2016. Delivery of the second vessel is expected in May 2016, and the third and fourth vessels are to be delivered no later than early 2017. Commissioning the first two vessels in time for the 2016 construction window is critical for maintaining the 2017 start-up date.
Concurrently with the main EPC project, a tender was awarded to Daewoo Shipbuilding & Marine Engineering to build up to 16 ARC7 ice-class LNG tankers – a specialized tanker type that is globally in short supply. The shipyard will improve the existing design of the ARC7 tankers and will subcontract part of the construction work to a Russian ship-builder. Sovcomflot’s first and only ARC7 tanker, the lead ship, is to be delivered in 2016 by DSME, while the following five tankers (acquired by Athens-based Dynagas) are to be delivered from 2017 onwards. The other tankers will be operated by Teekay LNG, China LNG Shipping, Mitsui OSK Lines (MOL), and China Shipping Development. Completion and commissioning of the first ARC7 tanker is a concurrent critical path to commercial operations.
Where should the construction claims group be located? In the Philippines, where modules are being fabricated? In Korea, where special-purpose transportation barges and ice-class LNG tankers are being built? In Paris, where Technip’s project team is managing design interfaces? In Moscow, with the client’s group? Or on site, at the “end of the world,” with the construction team? On a project with such a small construction window, extreme weather conditions, and dependence on special-built transportation assets, potential sources of delays, disputes and cost overruns are too complex, interdependent and numerous to be listed here.
Reactive claims management relying on organic knowledge transfer within an integrated project team – the traditional approach applied to simple construction projects – would quickly overwhelm claims management capabilities. Project-wide data management strategy, supported by Intellectual Property (IP) frameworks, pass-through contractual clauses, and a collection/retention infrastructure is a must for a project of such scale and complexity. But such a project-wide, forensically sound and user-driven data management strategy is seldom planned or implemented. Without consideration for the modularized execution strategy, the claims management function may remain isolated, fragmented, and limited by information management silos.
4. CHALLENGES OF PROJECT CLAIM MANAGEMENT IN A MODULARIZED DELIVERY ENVIRONMENT
In the context of modular fabrication, much of the focus has been on design and transport and logistics strategies. Many project delays and cost overruns have been blamed generically on “logistics challenges.” For example, the Papua New Guinea LNG project was apparently delayed due to work stoppages and land access issues ($1.2 billion), plus adverse logistics and weather conditions ($700 million). Likewise, regarding the V.C. Summer Nuclear Station Power Plant Project it has been reported: “The project’s production schedule is largely threatened by delays in the delivery and manufacturing of submodules … and the submodule issues would require revising the construction schedule and could add $200 million to the project’s costs.”9
Table 1
Projects Using Modular Construction Impacted by Logistical Challenges
that Contributed to Significant Project Cost Overruns
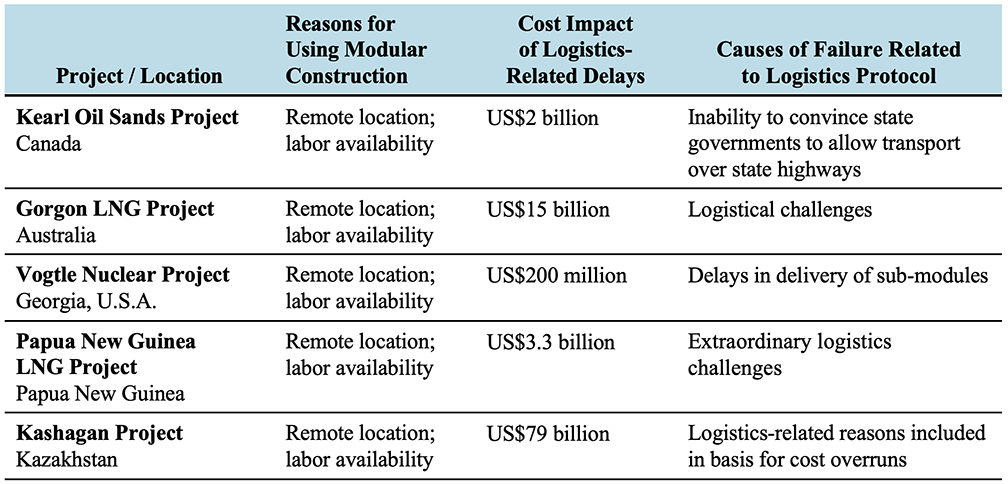
Note: Table 1 data is from Factors Affecting Large Scale Modular Construction Projects, 50th Associated Schools of Construction Annual International Conference Proceedings, 2014.)10
Yet a literature review indicates a lack of specific research regarding optimal planning and project management approaches for delivering modular projects of all sizes.11 In the context of mega energy projects such as Yamal LNG, few studies have explored the qualitative organizational issues related to the interplay between modular construction, manufacturing outsourcing, and organizational scale. Even less attention has been paid to the impact of modularization on data flow and to modularization’s impact on data-intensive analytical functions such as claims management and dispute resolution.
Concerning data management for modular projects, three key areas of concern are emerging:
- Organizational Silos and “Invisible” Concurrent Delays
- Data Silos and Usability
- IP Ownership and Data Retention
The next section of this article addresses each of these areas through case studies and theoretical fact patterns based on actual engagements.
4.1 ORGANIZATIONAL SILOS AND “INVISIBLE” CONCURRENT DELAYS
Interface management is required for projects where multiple contractors are responsible for interconnecting scopes of work on a larger integrated project. In fact, interface management is critically important for both offshore (FPSO and FLNG) and onshore mega-projects where many contractors design and supply entire process plants along with a PMC or project management contractor. Each interface is critical to avoiding work-hour escalation or schedule creep.
Interface management is first and foremost about breaking down silos between manufacturing and construction, and enabling information flow between these two functions. In an EPCM contracting model (i.e., Engineering, Procurement, and Construction Management in one contract), the overall administration of interfaces is performed by the EPCM contractor with support from the client.
The EPCM contractor typically provides interface management tools to control the status and flow of design information – but does not generally equally focus on interface management for modular project execution. These tools provide contractors with a structured method to efficiently communicate with one another. The interface management tool functionalities include: the identification of project team member responsibilities, status of interfaces, need dates for data, record of interface documentation, identification of overdue tasks, and progress measurement of the interface management scope of work.
Similarly, EPCM contractors often implement system integrity programs. Technical “system owners” for each major system have the responsibility for its overall design. These teams provide technical assurance regarding the performance of the designed modules. They are not, however, providing execution assurance. In the absence of an equally sophisticated interface management and project execution integrity program, the EPCM model adds an additional layer of complexity, rather than mitigating modularization-driven fragmentation.
Execution assurance and claims management, as project management functions, are generally relegated to the respective site offices. Rather than operating at a cross-functional and cross-system level, the claims management function is fragmented among the different project delivery groups. This fragmentation and delocalization of the claims management function often prevents information flow between claims analysts and the offshored manufacturing groups that are actually managing modular fabrications. Concurrent delays impacting module manufacturing thus become less visible.
For example, most onshore LNG projects – such as INPEX’s Ichthys LNG and Chevron’s Gorgon LNG – require construction of a Module Offloading Facility or MOF, initially for delivery of modules and later for product export. Completion of the modular offloading facility is critical for allowing the start of construction and module installation. While the largest “visible” part of building such an offloading facility is dredging and reclamation, its construction also involves installing abutment structures for barge berths and the installation of breasting and mooring dolphins for the module carrier berth.
On a typical onshore LNG project, both mooring and abutment structures (modular caissons of reinforced concrete) are fabricated offsite, possibly in China, Indonesia and Australia, and then placed on a stone bed. The berthing dolphins are piled steel structures equipped with mooring bollards and parallel motion fenders; structural steel dolphin jackets supporting the bollards and fenders can weigh in excess of 250 tons. On such a project, fabrication defects associated with any set of component parts can initially go unnoticed, causing an “invisible” concurrent delay: this could happen, for example, with faulty welding in fender parts.
Construction disputes often focus on civil work that is taking place “in the open.” when dredging and reclamation works are indeed progressing more slowly than planned; these delays can give rise to protracted litigation regarding every aspect of the dredging operation, mobilization, quarantine, and adverse weather conditions. Let’s assume that, in the meantime, owner-supplied fenders, manufactured in China, were being delivered in Batam, Indonesia, where the dolphin jackets were being fabricated. A heavy-lift ship would then transport fenders and jackets to the MOF for installation. Welds in the fenders were defective, but this defect had not been noticed in China. An unusually violent tropical storm hit Batam, and the painted fenders were submerged for several days. After the water had receded, rust marks on the recently completed fenders suggested innocuous paint defects. While re-painting the fenders, however, the Batam-based contractor noticed severe weld defects.
Radiography inspection of the welds revealed widespread weld defects. The fenders required substantial repairs. The Chinese contractor refused responsibility for fixing the defects; the Batam contractor, already under time pressure for completing its own scope of work, refused to concurrently repair the fenders. Shipping 250-ton fenders back to China or to Korea would be practically and economically nonviable. The corrective work to the fenders was completed later, resulting in a substantial delay to the date of first shipment.
This delay event originated with the fenders’ manufacture in China and the Owner’s QA team’s failure to detect the defective welds. These fender delays could be treated as concurrent with the Contractor’s dredging delays. The fender delays might, in fact, actually be the driving delay on this project. While it may be possible to accelerate dredging by mobilizing an additional vessel, it was not possible to accelerate the repair of massive fenders stored on a yard in Indonesia. Without berthing dolphins, the MOF facility could not be used for its intended purpose. The concurrent delay to the availability of the owner-supplied fenders excused the contractor’s dredging delays. Should this matter have proceeded to arbitration, the existence of such a concurrent critical path would control the case’s outcome.
These concurrent delays were, however, invisible to the claims teams on the respective owner’s and contractor’s sides. As is typical in most project-focused organizations, off-site quality assurance was performed by a separate team with a direct reporting line to the claims management group. The communications, photos, and reports of the QA group were kept on a computer system entirely separate from the project system, if they were accessible at all. Although delays related to delivery of fenders and modular caissons were known, there was no internal stakeholder for documenting those delays and acting as the central interface between the manufacturing group and the construction group. Organizational design and interface between the claims management function and all aspects of the modularized execution are key to preventing this kind of delay‑claim blind spot.
4.2 DATA SILOS AND USABILITY
Organizational design is, however, insufficient in itself: claims assessment requires access to the right data, at the right time, in a usable format. Large infrastructure and energy projects are heavily fragmented among different parties, systems, and geographical areas. The modularization of design, offsite manufacturing and outsourcing to low-cost, high-capacity manufacturing centers in the Asia-Pacific region further fragments project execution. As discussed in the previous section, concurrent delays, critical performance issues, and cost overruns can be obscured from visibility: a project office in Moscow, Chengdu, Perth or Calgary often will not have access to the document trail required to track each component of a modularized project through a maze of offshoring, outsourcing, and off-site manufacturing.
From an execution perspective, there is a qualitative distinction between fragmented and modularized. A project that embraces modular construction techniques but fails to consider the implications of global modularization on execution can only be described as “fragmented.” A modular approach to project execution, on the other hand, would incorporate careful attention to interfaces between execution modules: data modeling, data interchange, full system ownership and overall formal block diagramming of the project components. Broadly speaking, this conceptual transfer from modular design to modular execution has not yet occurred. Unfortunately, many modular design projects today could most accurately be categorized as fragmented.
The operational environment of a fragmented modular design project creates unique challenges for claims managers. Assuming that a claims manager (typically hired by the project team when the construction phase is already substantially advanced) has succeeded in fully identifying all contractual obligations to capture the complete picture of all concurrent delays, he or she now faces a significant challenge in assessing concurrent delay for a complex project with geographically dispersed modularized construction. Thus, there is an increasing need for project-wide data collection. The claims manager must now clear several hurdles, including:
- Finding the progress and contract management data maintained by multiple interrelated but uncoordinated project units but also by contractors and subcontractors;
- Accessing the data, assuming that it still exists in a format that allow for retrieval and processing;
- When data has in fact been preserved and collected, and access to that data is assured, making sense of disparate and at times incomplete data sets that have not been modeled for interoperability, e.g., for addressing the specific needs of specific project functions such as project controls and benchmarking.
Offsite manufacturing contractors often do not maintain progress data in proper formats. Progress data is often stored at the remote manufacturing facility and is seldom backed up in an easily retrievable form. Contractual claims, typically managed by a local representative, are not properly documented. Claims assessment, under such conditions, can initially take the form of an archeological dig through widely disparate and poorly mapped data repositories.
Sometimes data may be fraudulently suppressed. In one case, a concurrent delay ran through offsite manufacturing of structural elements for a large 300-ton jetty cantitraveller. The EPCM contractor had attempted to hide manufacturing delays by depicting an artificial critical path running through site preparations – progress inspections had been “visual,” i.e., undocumented. The manufacturing timeline had to be recreated using the supplier’s marketing materials, barge movement data, quality assurance reports, and Google maps views of the fabrication yard.
In other cases, data is missing or incomplete because staff in remote locations have not been tasked or trained in proper recordkeeping techniques. In one case, defective owner-supplied equipment manufactured in China was suspected to have caused critical concurrent delays. The Chinese manufacturer, eager to clear his staging area, threatened to turn the defective equipment into soda cans if the owner refused to take immediate delivery. The owner took delivery and sent the defective equipment to its own yard in Indonesia; the equipment sat there while the owner, its offsite manufacturers, and the Chinese suppliers quarreled over their respective responsibility for corrective work. At the time, no claims manager had been informed and mobilized and no organized effort to document contemporaneous records of the delays had been initiated. Documentation had been left to untrained and uncoordinated professionals. Recordkeeping was, at best, spotty.
The concurrent delay was documented by painstakingly collecting unstructured information in the form of inspection photos, handwritten travel notes, and comments included in unrelated inspection reports. The owner’s staff, quality assurance inspectors (joint project team), third-party cargo inspectors, marine warranty surveyors, and an offsite representative, had captured snippets of the unfolding delays through progress photos, export logs and inspection reports. Each data set was maintained in digital or hard copy form, in a collection of unconnected data repositories, in some cases maintained only on personal computers.
Despite the potential difficulties in gathering information, data collection might be the easiest part of documenting a concurrent delay or cost overrun. In a fragmented modular project – as opposed to a project with integrated modularized execution – each data set has been collected and modeled for the sole use of its immediate custodian. Unstructured data (photos, reports, notes, etc.) are often fragmentary, and access to structured data (attendance logs, inventory logs, etc.) is no panacea when the data has been collected without planning for interoperability.
In highly complex projects with multiple contractual actors and multiple worksites, failure to plan ahead for data interoperability can result in both a weaker claims position and greatly increased claims management costs. In Australia, an international mining company needed to assess a US$250 million claim for lost productivity arising from the expansion of a large iron ore export terminal. An offsite manufacturer was responsible for the conveying and processing systems, while the site itself involved two port facilities and approximately 60 discrete work sites. The EPCM contractor had structured the project contracts, work packages, scope of works, bill of quantities, progress reporting requirements and site manpower daily records in a way that could not be reconciled with the physical reality of the work being performed, i.e., the physical worksite and systems. Physical construction data (consumables and equipment) and manpower data were not reported on the same frequency or on a compatible data model. The EPCM had awarded Time & Material contracts without having structured progress data reporting to allow for benchmarking and monitoring of contractors’ productivity by ports, construction sites, and systems.
Without adequate job data (time, location, trade, system, type of work performed, etc.) and contextual information, it is almost impossible to give meaning to structured data such as manhours. In the case above, approximately 35,000 documents were processed, including gate reports, daily reports, and consumable use from environmental compliance reports (as proxy data for level of effort). Processing poorly modeled structured data can cost over US$1 million. In the end, the owner built a strong negotiating position and the claim value was reduced to half the amount initially claimed. The owner could, however, have better protected its interests at a fraction of the cost had it begun the project with a properly designed data management strategy and data ownership plan.
4.3 IP OWNERSHIP AND DATA RETENTION
The best data management plan is no panacea if access to project data, its collection, processing, and preservation are not provided and assured. Too often, claims managers have access only to fragmentary, incomplete, and sometimes unusable project data, when project data has not been preserved in a forensically sound manner. Many “fragmented” modular construction projects, especially large infrastructure projects, proceed in the absence of a data management strategy tightly coordinated with an overall assurance and dispute resolution plan. Data management is an afterthought, including:
- No project-wide IP/data ownership framework
- No project-wide data collection specification
- No project-wide data retention policy
- No project-wide data integrity audit
- No pass-through clause (on the FAR model) to guarantee consistency of data sets
Owners often rely on EPCM contractors to manage project data, yet EPCM contracts seldom include performance criteria or technical specifications related to data management. EPCM contractors are allowed to roll out customized, proprietary data and document management platforms over which they retain exclusive control. Owners often retain an audit right, but an audit right unsupported by control over data ownership, data modeling, data retention, and data collection, can be of little practical value.
In the context of a dispute between an EPCM contractor and the project owner, control over project data often becomes the key issue. Too often, key project data does not actually exist (due to fraudulent or willful negligence), is not available to the owner (due to proprietary data and document management systems), or has been destroyed (due to defective retention policies). This is especially problematic when the party at fault is the EPCM contractor itself. Three examples of problems obtaining documentation include:
4.3.1 Fraudulent or Willful Negligence in Data Collection
In a dispute between owner and EPCM contractor, collusion between the EPCM contractor and suppliers and contractors was alleged. Offsite inspection of modular fabrication yards was either not reported or was reported in summary or oral form. Data packages documenting shipments, QA/QC inspections, and supplier performance were incomplete and late.
4.3.2 Limited Access to Project Documents
In another case, the EPCM contractor owned the project document repository. In order to document claims against the EPCM contractor, the owner had to engage that same EPCM contractor. As the relationship between owner and EPCM contractor became contentious, the contractor curtailed access to the project documents.
4.3.3 Data Retention Breach
In most cases, data loss is the result of negligence rather than malice. The nature of modular construction requires project staff to spend more time at offsite locations. Compliance with data management policies is harder to enforce at those offsite locations than at the primary project site; more data is stored on local networks or on mobile and/or personal computer devices. When coupled with high staff turnover and often overtaxed IT departments, the result can be data loss.
On another case, there was a need to document delays for a complex rail expansion project between a new open cut mine and an export port terminal. Telecommunication systems for the railway system were fabricated as modules, delivered on skids and plugged on site. Delays arose from manufacturing issues. The integrator for the communication system had employed several planning managers – and with each staff turnover, the IT department had conscientiously repurposed the planning managers’ computer equipment, without first making an image copy of the hard drives’ contents. Years’ worth of data had been erased, and this data loss greatly complicated the claims assessment mandate.
5. CONCLUSION
As evolving modular construction design optimizes layout and moves toward plug and play fabrication, overlooked modular project execution issues have increased fragmentation of the project claim management function and fragmentation of the data that claims managers rely on to identify and resolve disputes. In the resulting paradox,12 even as construction risk directly related to module fabrication has decreased, systemic delivery risk specific to offshored modular fabrication may have increased. Mitigating the risk associated with modular construction offshoring will require a project-wide analytics transformation and a reassessment of the role and responsibility of project claims managers during the early stages of project definition and implementation.
Claims management in the context of modular construction increasingly relies on access to information maintained by a wider, more fragmented group of stakeholders, under varying legal jurisdictions and related through a complex maze of contracts that rarely impose consistent standards for data management. The claims management function is often situated in an organizational silo that undermines its ability to identify and assess concurrent delays occurring across offshored modular construction projects and related supply chain. When concurrent delays are identified and isolated, the absence of properly modeled and collected progress/construction data undermines claims analysis efforts. Where required project data has not simply been lost, it is often not legally accessible.
Meanwhile, the shift to modular design has been changing the risk profile for large-scale construction projects. Modular projects reduce some construction risks because they allow work to be performed in a controlled environment. But the movement of modular construction to cost‑favorable locations creates risks of its own: logistical/transportation risks and catastrophic risk have increased. Offshore manufacturing in cheaper markets also carries with it greater risk for fraud, negligence, and data loss. A claims manager involved with large infrastructure projects may now encounter supply-chain issues in China (where equipment can be re-imported via Hong Kong to avoid providing manufacturing QA documentation); over-ordering of electrical cable in Kazakhstan; design optimization errors in India; or simple collusion between EPCM and EPC contractors in Australia.
Yet industry experts on modular construction techniques and methods have continued to focus almost exclusively on manufacturing optimization, rather than devoting the same level of attention to project execution. The third revolution in modular design and modular construction has focused heavily on optimizing the interface between modules. Meanwhile, little attention has been paid to the increased fragmentation of the modular projects. “Modular execution” thus remains synonymous with design execution, not project management.
As owners embrace modular construction, the operational environment of project claim management has thus suddenly drastically changed. Our current data-collection systems have been carried over from traditional geographically centralized construction sites, where all work takes place on site and the proximity of all actors to the construction project and its stakeholders. This legacy approach has prevented the development of robust and formal reporting processes adapted to the challenges of a new modular building environment.
The resulting misalignment between the claims management function and the data management infrastructure is a growing risk factor and a source of frustration. From a claims management perspective, access to the right data, at the right time, in the right form, is critical for delivering dispute avoidance strategies. Obviously, the claims manager must first be aware that a dispute actually exists – which is no longer guaranteed by the claims manager’s physical proximity to the construction operation.
Outside the construction sector, companies with a solid Data and Analytics (D&A) strategy have been found to outperform their competitors and create greater value for their shareholders.13 D&A allows for better decision making and greater understanding of the evolving risks associated with modularized project delivery. Better end user-driven D&A within large-scale modular construction projects would allow claims and commercial managers to identify potential claims and actionable insights in a timely manner.
The analytic transformation of the claims management function will take time. It requires project-wide integration of data collection, modeling, and processing technologies. More critically, it requires upgrading the status of the claims management function, from a site-focused, reactive service to a project-wide proactive stakeholder in project risk management strategies.
There are strong synergies between the internal audit function, lean manufacturing and continuous improvement function, the risk assurance function, and the claims management function – all depend on the data strategy of energy companies and project delivery teams; all are equally challenged by the offshored modular delivery model.
Claims managers are well placed to capitalize on a better alignment of manufacturing process and data management strategies. They are also better placed than many industry professionals to demonstrate the immediate benefits of such realignment. Claims managers must thus take a proactive role and make their voices heard in the ongoing D&A debate. Whether they can succeed in shaping the data management strategies of their project delivery organizations may significantly enhance their capacity to protect those organizations from the systemic – yet often opaque – risks of modular project delivery.
About the Author
Charles P. Fournier, J.D., CCA, was a Managing Director with Long International. Mr. Fournier has over 15 years of experience in U.S. and international engineering and construction management and dispute resolution consulting, including construction contract disputes analysis, claims preparation, arbitration and litigation support, expert testimony, schedule control, commercial negotiation, risk assurance, construction audit, and contractual process engineering. He is a bilingual French-English business strategy and construction advisory professional with extensive experience leading teams that solve client problems involving dispute resolution, claims negotiation, and performance audits. Mr. Fournier focuses his practice on owners, engineering firms, and contractors in the petroleum refining, petrochemical, oil and gas, power/cogeneration, mineral processing, industrial, building, and infrastructure market sectors worldwide. For further information, please contact Long International’s corporate office at (303) 972-2443.
1 Angus W. Stocking, L.S., “4 Ways Prefabrication and Modern Construction Methods Will Make Building Better,” Redshift by Autodesk, November 12, 2015, https://redshift.autodesk.com/prefabrication-and-modern-construction-methods/.
2 Graham Chandler, “Smaller, Better, Faster,” Oilsands Review, May 2013, https://dycatsolutions.com/wp-content/uploads/2020/01/oilsandsreview-1.pdf.
3 Id.
4 Fred Haney, “Unlocking the Modular Revolution,” Mammoet World, Issue 14, 2015, http://www.mammoet.com/siteassets/expertise/modular-construction/unlocking-the-modular-revolution.pdf.
5 See, e.g., the proceedings of the Modular Construction & Prefabrication for Oil & Gas Conference, Rotterdam (September 21–23, 2015).
6 Especially since the adoption of ISO 55000 (an outgrowth of PAS 55, the first publicly available specification for optimized management of physical assets developed in 2002–2004 by the Institute of Asset Management (IAM) in conjunction with British Standards Institution (BSI)).
7 See, e.g., Lincoln Forbes and Syed Ahmed, Modern Construction: Lean Project Delivery and Integrated Practices (CRC Press, 2011).
8 See, e.g., Jianguo Ye, “Integrating Data Models, Analysis and Multidimensional Visualizations: a Unified Construction Project Management Arena” (Ph.D. thesis, University of British Columbia, 2009).
9 Chuck Crumbo, “Report cites ‘significant challenges’ at V.C. Summer nuclear project,” Columbia Regional Business Report, July 12, 2013.
10 Mitzi Carriker and Sandeep Langar, Ph.D., LEED AP BD+C, Factors Affecting Large Scale Modular Construction Projects, 50th ASC Annual International Conference Proceedings (2014).
11 Id.
12 This paradox is common to all data-intensive functions: internal audit, risk assurance, lean manufacturing, continuous improvement, and claims management.
13 Joint study by KPMG and Institutional Investor Research, 2015. The construction sector was not specifically addressed in the KPMG/Institutional Investor Research study (construction is mentioned only once, as an aside, in a discussion of clothing manufacturing).
Copyright © 2019 Long International, Inc.
ADDITIONAL RESOURCES
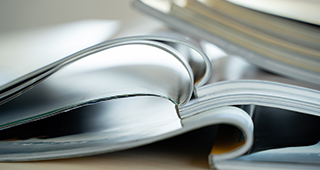
Articles
Articles by our engineering and construction claims experts cover topics ranging from acceleration to why claims occur.
MORE
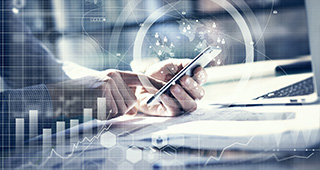
Blog
Discover industry insights on construction disputes and claims, project management, risk analysis, and more.
MORE
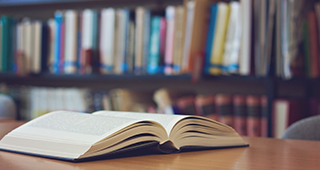
Publications
We are committed to sharing industry knowledge through publication of our books and presentations.
MORE