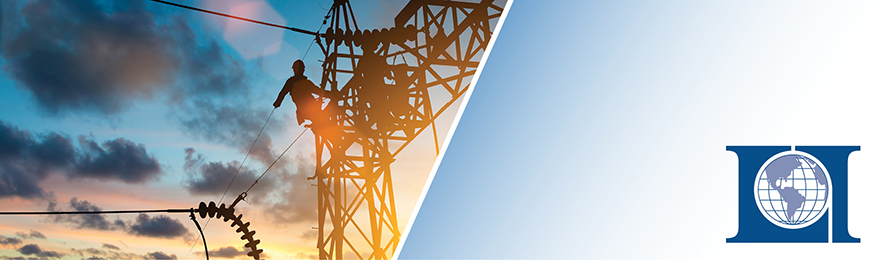
Keys to Successful Major Project Execution
This article is based on the author’s experiences in the energy sector and examines some guidelines for effective EPC project management control from the owner’s perspective.
1. INTRODUCTION
For any Project to have a successful outcome, there must be consistent application of a suite of effective Project Management processes and tools. Such application commences from the earliest stage of the Project when a Project Concept and Project Charter are being considered. These tools can be applied to any Project, regardless of its size (CAPEX expenditure, quantum of required human and equipment resources), complexity (process, industrial, commercial, infrastructure), critical success factors, timing (schedule), and governance structure (private sector, government).
1.1 WHAT MAKES A SUCCESSFUL PROJECT?
Many organizations define Project success as completion of the Project within the sanctioned Cost and Schedule. This is about as rudimentary a definition as possible and is not a good indicator of Project success if the CAPEX spend and Project Schedule have included large contingencies that simply mask underlying Project execution inefficiency.
This narrow definition does not encompass Health Safety Security Environment (HSSE) aspects, in particular delivering a SAFE Project. Also excluded are the very important aspects of delivering a Project free from engineering (or other) rework (defect elimination). Another missing objective, in the case of a process plant, is that the Project must achieve every metric specified in the Performance Test clauses in the EPC Contract, and after successful Commissioning, maintain target levels of plant reliability during commercial operation. Also to be considered is whether the Project achieved the desired level of Transfer of Technology, handed over the Project Documentation in a manner that facilitates easy utilization by Operations and, very importantly for a Brownfield Plant, whether the Interface Management with Operations was handled in an efficient manner and unplanned disruptions to Plant Operations did not occur. At the Conceptual Stage of a Project, it is important that there be agreement between the Project Leadership and the Owner’s management regarding the metrics by which Project success will be defined, since it is against the agreed metrics that the Project success would be measured.
In the past years, consensus has emerged that Project Management knowledge/experience, skills, tools, and techniques are all required for successful Project execution. Project Management has always been practiced informally, but in the mid-20th century it began to emerge as a distinct profession. The Project Management Institute’s (PMI’s) “A Guide to the Project Management Body of Knowledge (PMBOK® Guide)” identifies its recurring elements, noting that Project Management processes fall into five (5) groups:
- Initiating
- Planning
- Executing
- Monitoring and Controlling
- Closing
Project Management knowledge typically focuses on ten (10) broad areas viz.
- Integration (Management of interface with other Stakeholders)
- Cost
- Human Resources
- Stakeholder Management
- Scope
- Quality
- Schedule
- Procurement
- Risk Identification (Generally HSSE would be included)
- Communications
This article is based on the author’s experiences in the Energy Sector and examines some guidelines for effective EPC Project Management control from the Owner’s perspective. There is one overarching requirement: The entire Project Execution – from Initiation to Execution and Close‑Out – must follow a rigid process that ensures the requisite amount of Front-End Loading (FEL) is applied before – and is in fact a condition for – Project Sanction. FEL is the process for conceptual development of projects in process industries and may also be referred to as Pre-Project Planning (PPP), Front-end Engineering Design (FEED), feasibility analysis, conceptual planning, programming/schematic design, or early project planning.
The elemental components of a Stage Gate Process applied to Project Management are outlined, discussed and, where appropriate, further detailed. In a Stage Gate Process, there are defined activities that must be executed in each stage and the Project is only authorized to progress from one stage to the next succeeding one with the approval of a “Gatekeeper” who could be an individual or a committee.
2. PROJECT INITIATION AND STAGES
Selecting a capable Project Leader/Director, establishing an effective Project Leadership Team, and implementing a Stage Gate process by which the Project life cycle will be managed are key steps to initiating a successful Project.
2.1 ESTABLISH A PROJECT LEADER/DIRECTOR
The Project Leader/Director must have the required level of Project Management experience for the type of Project being contemplated/developed. Familiarity with problems and lessons learned from similar projects are key requirements and would enable thorough examination of the Project Risk Register and the mitigation strategies for the identified risks. The Project Leader/Director is the Single Point Accountable (SPA) individual who is charged with the overall delivery of the Project in accordance with the criteria established by the Owner and in consonance with a rigorous Project Initiation, Development, Execution and Close-Out Process. The SPA assumes responsibility for the composition of the Leadership Team chosen to deliver the Project.
Some considerations that should influence the selection of the Project Leader/Director include, but are not limited to, the following:
2.1.1 Proven Leadership Skills
The SPA ensures that the Leadership Team functions as a Team, effectively leveraging diversity in whatever form such diversity exists, drives alignment of purpose and commitment across the Team, and leads by personal example in critical areas such as HSSE drivers. The SPA is responsible for the development of the overall Project Plan and management of the performance of each member of the Team, setting the appropriate performance drivers in individual consultation with them and, thereafter, challenging the Team to the highest level of personal and collective performance standards.
2.1.2 Type of Project
Is the Project a Greenfield or Brownfield Project? For a Brownfield Project, effective management of the interface between the executing Project Team and the Operations Team is a critical success factor, where very often there will be requirements for operating plant shutdowns to facilitate tie-ins. Certainly no commissioning could be successful unless there is seamless and close coordination of the commissioning with plant operations.
What is the anticipated CAPEX spend? A $2 billion project is likely to be better managed by someone comfortable with such large CAPEX rather than an individual whose largest CAPEX responsibility is $10 million.
2.1.3 Project Location
For locations in developing countries, for example, experience is required in doing business under conditions that can often be very different than those that exist in developed countries. A simple example: understanding the importance of the Foreign Corrupt Practice Act (FCPA) and its consideration in setting the Project Charter is vital for a successful project in a developing country.
Another important consideration in executing Projects in countries with emerging economies, such as those in Africa, which have recorded significant discoveries of hydrocarbon resources, is familiarity with the host country’s policies such as those regarding Procurement and Local Content.
The Project Leader/Director must appreciate the importance of understanding the host government’s approval process, in terms of the various stages and the overall timeline for approval, since these could have a major impact on the Project Schedule, and failure to understand these elements inevitably leads to delays, disruptions, and disputes.
It would also be important to have sound knowledge of the availability of capable local human resources, equipment, workshops, etc. to support the Project Execution.
2.1.4 In-House vs. Outsourced Project Management
Is the Owner outsourcing the overall Project Management to the EPC Contractor on a Lump Sum Turn-key (LSTK) basis? Will there be an independent Project Management Consultant (PMC) performing all Project Management functions? In each of the foregoing contractual structures, the experience of the Owner’s Project Manager needs to be relevant.
2.1.5 Experience in Project Controls
The Owner’s Team must have experience in Project Controls to ensure that the schedule, change management, earned value measurement, and cost elements of the Project are being properly measured, statused, reported, and controlled. Depending of the type of contract, i.e., lump-sum turn-key, fixed price, unit price, or cost reimbursable, key provisions of construction contracts should be utilized to ensure that identified Project Risk is properly allocated to the party best able to control that risk. For example, the Owner may have contract clauses that reflect no damages for typical delays, such as changed site conditions, approval process delays, normal inclement weather, etc. The types of man-hour and cost reports that the contractor would be required to produce to the Owner on a periodic basis (usually monthly) is different for the various types of contracts. Labor productivity reporting also is a function of the type of contract being utilized. The Owner also needs personnel familiar with the type of scheduling software to be utilized by the contractor for CPM schedule development, updating, and control.
2.1.6 Experience in Contract Dispute Avoidance and Contract Dispute Resolution
Delays, disruptions, and changes (e.g., engineering changes as a result of any of poor Pre-FEED and FEED work, Hazard and Operability (HAZOP) Reviews, Peer Reviews, and Construction, including unknowns surfacing during site construction) are difficult to prevent, but an experienced Project Leader/Director and a solid Project Leadership Team can anticipate many delays and, therefore, to the extent that they are identified upfront, the mitigation strategies can be reflected in the contract documents and in the appropriate degree of advanced planning.
2.2 ESTABLISH THE PROJECT LEADERSHIP TEAM
Establishment of the Project Leadership Team is the responsibility of the Project Leader/Director under the appropriate authority vested in him by the Owner’s management. The Team members must be chosen based on the design of the Project Leadership Structure.
In a Project with no PMC, the Project Leader/Director and the Project Leadership Team assume full responsibility for the traditional PMC role usually adapted on most projects. The Project Leader/Director would typically report to an Owner Oversight Committee or Project Sponsor. All activities are undertaken by this Team, including direct management of the Pre-FEED, FEED, EPC Execution Phase, Project Handover, and Project Close-Out. A typical Organization Structure is shown in Figure 1 below:
Figure 1
Project Organization Leadership Structure: No PMC –
Owner Performs Project Management
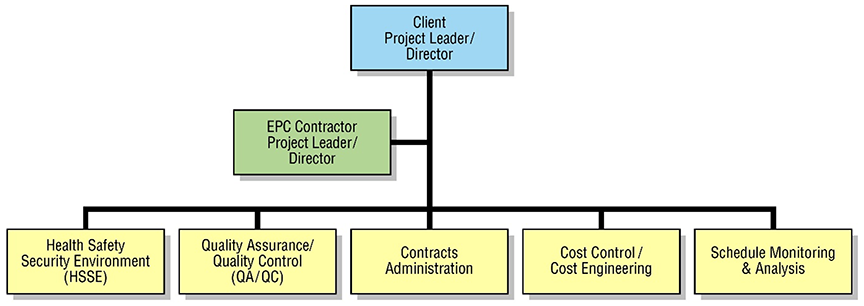
One variation to the above, and other structures that follow, is the insertion of a Project Controls Manager to take direct charge of the activities of the various Department Leads (HSSE, QA/QC, etc.) and to collate their activities to produce a Monthly Progress Report.
In the case of the Owner outsourcing the Project Management function to a PMC or to the EPC Contractor directly, the Project Leader/Director may not have a Leadership Team and would be required to act as the Owner’s Representative, in addition to assuming responsibility for the overall Project Delivery. A typical structure for this model is shown in Figure 2 below:
Figure 2
Project Organization Leadership Structure:
PMC Performs Project Management
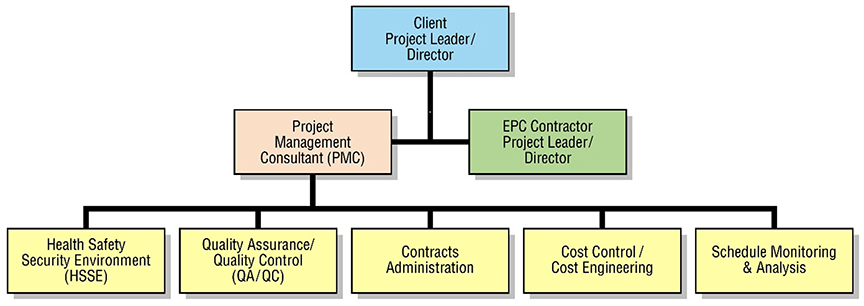
In projects in developing countries, there are several examples of the Owner ceding total responsibility to a PMC for successful Project delivery, despite the existence of a Project Leader from the Owner’s management. In these situations, the Project Leader is largely a figurehead, if he or she does not possess the requisite experience to effectively drive a major multibillion-dollar process plant Project. This example is fraught with thorny issues as the Project outcome in critical areas such as Equipment Selection, Quality Assurance/Quality Control (QA/QC), HSSE, Project Handover Documentation, Training, Commissioning/Start-Up, and Project Close-Out are at the mercy of the commitment of the PMC to the highest standards of Project Management.
A typical structure is shown in Figure 3 below:
Figure 3
Project Organization Leadership Structure: PMC Performs
Project Management and Directs EPC Contractor
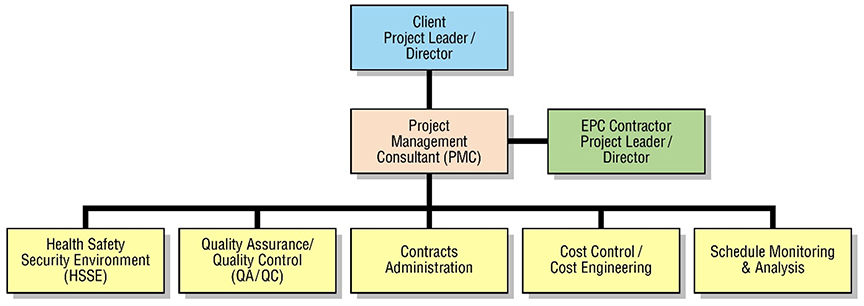
It has been the author’s experience that this is not unusual in projects executed in countries with emerging hydrocarbon economies and, in every instance, there has been a deleterious impact on post-handover operations. There have also been instances of the Project failing to achieve meaningful transfer of technology to local resources, particularly at the engineering level. In other words, failing to deliver on Local Content provisions (or Owner expectations).
2.3 ESTABLISH THE PROCESS BY WHICH THE PROJECT LIFE CYCLE WILL BE MANAGED
The Owner’s Project Leader/Director is responsible for selection of the Project Life Cycle Management process, which would typically be approved by the Owner’s Project Oversight Committee or the Project Sponsor. It is generally accepted as best practice that the Stage Gate approach, once adopted with the required rigor, will deliver a successful Project.
In a Stage Gate Process, there are defined activities that must be executed in each stage and the Project is only authorized to progress from one stage to the next succeeding one with the approval of a “Gatekeeper” who could be an individual or a committee. The selection of the Gatekeepers for each stage is a critical success factor for a Stage Gate Process to deliver a successful Project.
Why a Stage Gate Process? There are many and varied reasons, but in the author’s experience, this type of Project Management approach is greatly beneficial because a Stage Gate Process:
- Is a proven approach;
- Achieves cost and schedule improvements of 10 percent and potentially more per specific industry benchmarking;
- When applied effectively, minimizes the potential for delay and disruption claims;
- Is based on principles of other established quality systems, e.g., PDCA (Plan‑Do-Check-Act), ISO 9000, Six Sigma;
- Provides a common language and framework that enables systematic Project Management over the Project Life Cycle;
- Is applicable to any Project, but large and complex Projects (i.e., Major CAPEX expenditures, High-Technology Projects, Brownfield Projects in large Petrochemical Operating Plants, Offshore Oil & Gas Projects, etc.) will require more sophisticated use of the Stage Gate Process Principles;
- Ensures that all the work in one Stage is fully completed to the agreed standard before the Project proceeds to the following Stage;
- Implements a thorough Front-End Loading (FEL) Plan which is essential to successful Project outcomes, i.e., Plan the Work, Work the Plan;
- Establishes Key Project Roles, e.g., Gatekeeper for each Stage, Project Leader/Director, Project Leadership Team;
- Defines Project Plan and Business Case;
- Manages Stakeholders;
- Ensures Project Handover is efficient, with particular importance accorded to Project Handover Documentation;
- Captures Lessons Learned; and
- Publishes a Project Investment Analysis (PIA) report that records the achievement of the Project vs. pre-Agreed Project Drivers.
While the number of Stages and the associated activities in the management of a Project Life Cycle may vary for each type and size of Project, essentially there are at least five (5) Stages that should be considered, viz:
- Appraise
- Select
- Define
- Execute
- Operate
These Stages are shown pictorially in Figure 4 below:
Figure 4
Discreet Stages of a Typical Project
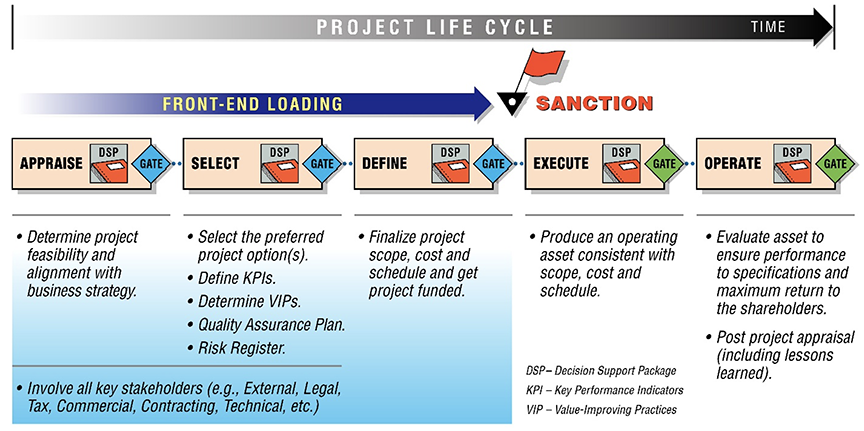
A key aspect of this type of process is to ensure that throughout the Project Life Cycle, the appropriate Stakeholders are intimately involved/consulted.
Figure 5 below depicts how this occurs on Projects that employ Project Management best practices.
Figure 5
Integrated Involvement throughout the Project Life Cycle
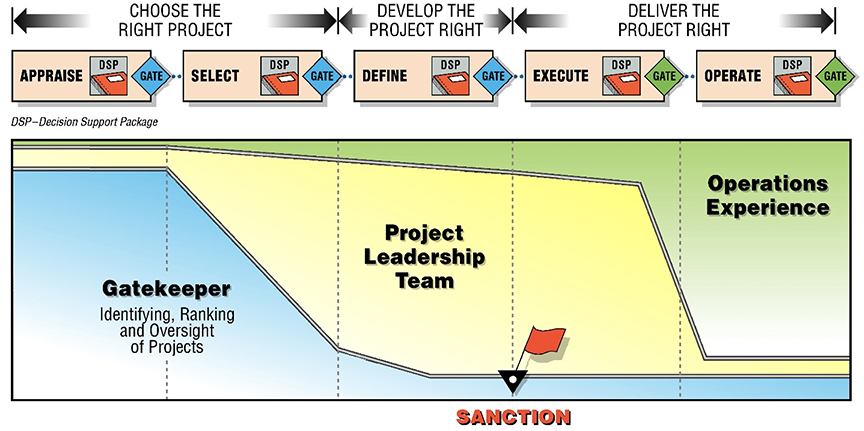
From the inception, Operations personnel are imbedded in the Project, which is of paramount importance for Brownfield Projects but also very important on a Greenfield Project. Of note is the role of the Gatekeeper, which is more critical in the early stages of the Project up to Project Sanction, thereafter reducing but still present to the End. The Project Team is engaged right to the end of the Project, as the Project Hand-Over and Closeout are top priority.
Figure 5 also summarizes the three (3) basic Keys to Successful Project Development and Execution, viz.
- Choose the Right Project (Appraise/Select Stage)
- Develop the Project Right (Define Stage)
- Deliver the Project Right (Execute Stage)
By adopting and following the tenets of a Stage Gate approach, the required Front-End Loading (FEL) allows for efficient Project Development with minor expenditure up to Project Sanction. Figure 6 shows the critical importance of FEL in the early stages of the Project. Conversely, the Project CAPEX expenditure increases significantly after sanction when the Project is in EPC or Execute Stage.
Figure 6
Front-End Loading Influence vs. Project Expenditures
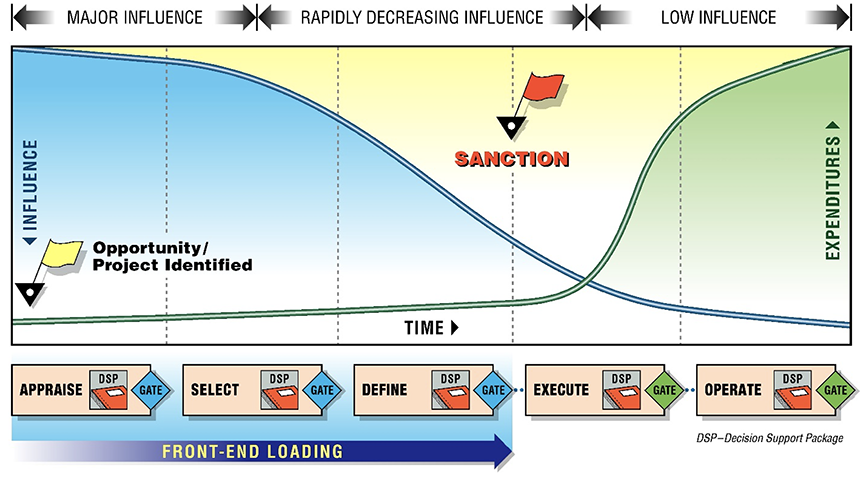
The activity sets in each of the above Stages are further detailed below:
2.3.1 Appraisal or Concept Development Stage
At the initiation of the Project, the Value Drivers will be established. For example, in one particular major project in a hydrocarbon producing company, a decision was taken to let the major Value Driver be the development of a “Green” Project.
In this stage, several options for the Project are considered and evaluated utilizing technical and commercial criteria, and which have considered all risks that could materialize during Project Execution. The Appraise Stage Gatekeeper has direct control over the concepts selected for Appraise Stage evaluation, which should consider technical and commercially viable Concepts/Options with the highest standards of HSSE accorded the appropriate priority. There may be special Regulatory Approvals required from Central (Government) Authorities like a CEC (Certificate of Environmental Compliance), which in some jurisdictions could take as long as 6–8 months.
The Project Leader/Director would also have the authority to request cross-disciplinary assistance from elsewhere in the Owner’s Organization.
The Appraise Stage would specify whether the Project is Greenfield or Brownfield, since there would be different considerations that attend each, such as the high priority placed on Interface Management between the Project and Operations activities on a Brownfield Project and possibly less soil investigation required if geological mapping had taken place on the site during the initial plant construction.
Selection of technology would also be included here. There could be many considerations, but if the Project is a Brownfield Project, a high priority may be accorded to the maintenance of similar technology as in the existing plant where the new Project is being contemplated. A preliminary Scope of Work (SOW) is prepared, and for the Brownfield case, the Project Leader/Director has to ensure that a fit-for-purpose SOW is developed.
For either a Brownfield or Greenfield Project, there must be the appropriate Front-End Loading (FEL). The FEL should include a number of Best Practices, e.g.:
- Implementation of VIPs (Value Improving Practices); one example of a VIP on an LNG project would be to establish the CO2 emissions target, usually expressed in tons CO2/ton LNG. Generally, the lower the target, the higher the CAPEX expenditure but a lower target may be highly valued in certain jurisdictions;
- Development of Project Assurance Plans;
- Establishment of a Preliminary Risk Register. Particular attention must be given to the management of the interface with Operations;
- Field verification of As-Built P&IDs, One-Line Electrical Diagrams, Piping Isometrics, General Arrangement (GA) Drawings, Control System Logic, Alarm Management, etc.;
- Integration of maintenance TAR (Turnaround) activities with potential Project tie-ins;
- Analysis of existing instrumentation systems;
- Development of material management plans and revision of Warehouse Stock Levels ‒ Re-order Points/Economic Order Quantities (ROPs/EOQs);
- Inspection and testing of existing equipment. Failure to so do may lead to unwelcome surprises during construction work with a resulting potential not only for cost increases but schedule delay and major claims that are rooted in opportunity loss (i.e., production loss);
- Integration of design package delivery with construction. Identify critical engineering review items, e.g., HAZOP, HAZID; and
- Evaluation of existing equipment specifications to establish the extent to which similar equipment could be procured.
Whether Greenfield or Brownfield, the Project Leadership should consider retaining the expert services of companies or consultants that specialize in examining the degree of FEL on a Project. Typically, the mechanisms for examining a Project’s Quality Assurance (QA) Plans are a set of project input/driver frameworks, developed through research performed by the consultant/company and application on a wide range of Projects over many years that has led to the build-up of a very significant database.
The QA plans would be evaluated in the following key areas:
- Front-End Loading status: This would establish the Project’s FEL Index, which is typically shown on a scale that compares the Best-In-Class QA FEL Index to the Worst-In-Class, thereby allowing the Project Leadership to have a sense of how its FEL measures in comparison;
- The level of application of Value Improving Practices;
- Application of Lessons Learned from similar projects around the world. Following the start-up of a major Petrochemical Project, there was a failure on piping that led to the plant being out of commercial operation for almost two (2) years, leading to billions of dollars in losses. It was subsequently discovered that failure to consider a design criterion was the root cause. A comprehensive Lessons Learned session prior to Engineering Pre-FEED, with experienced subject experts, would have identified the necessity for the application of the particular criterion that was overlooked;
- The current status of the Project Team (the Team Development Index); and
- Project Team plans for Project Controls (the Project Control Index).
In addition to these Project input/driver metrics, there would be an examination of how the Project would manage the introduction of new technology and how its transfer to the Operations Team would occur. The selection of the proposed contracting strategy would also be scrutinized to identify weak points that require further review and modification.
At this stage, there is definite value-add to consider a benchmarking exercise of similar Projects to provide additional or refined evaluation criteria to aid the selection of the preferred Project concept or option. The output from this Stage is a small number of selected concepts or options from among the short-listed concepts/options that best satisfies the evaluation criteria, and the evaluation process is detailed in the Appraise Stage Decision Support Package (DSP) that is forwarded to the Gatekeeper for review and comment.
The Appraise Stage DSP would contain, inter alia, the following:
- A number of Concepts/Options for further analysis in the next Stage (Select);
- Proposed Project Charter;
- Proposed Project Organization Structure;
- Business Case;
- Project Drivers;
- Quality Assurance/Quality Control Plans;
- Analysis of competing technologies;
- Plan to transfer Technology;
- A Preliminary Project Execution Plan (PEP), including Contracting Strategy;
- Identification of key proactive measure to minimize Contract Disputes, including inputs from experienced Claims Prevention Specialists;
- Pro-Forma Contracts for various works intended in the Select Stage, e.g., Pre‑FEED, VIP/Lessons Learned Workshops;
- Class 4 Estimates of CAPEX expenditure;
- Level 1 Project Master Schedule (PMS), showing efficient integration of various activities (e.g., Contractor, Project Team, Owner) prepared using standard scheduling Software – as utilized on international projects – that facilitates effective monitoring of Project progress and Project claims analysis arising out of contract disputes;
- Preliminary Project Risk Register with Risk Mitigation strategies carefully mapped and the Quality Assurance Plans;
- Preliminary Financial Model showing a Base Case, Low Case, and High Case for each Option, and which should be constructed to facilitate easy toggling of input parameters to instantly show their impact on the Project ROI (Return On Investment);
- To ensure that all Stakeholders are effectively engaged, the Project Leader shall drive the completion of a Communications Plan, which typically contains important elements such as:
- Engaging the Fence-Line community
- Legal and regulatory requirements
- Any site-specific or region-specific local governance processes like employment policies, special procedural requirements
- Owner’s communications policies
- Ensure protection of the Owner’s brand, i.e., reputation
- Plans for risk mitigation
- Applicable standards that will inform various aspects of project work, e.g., ANSI, API, NFPA, ISO 9000, ISO 14,000, etc.
- HSSE Plan
- Procurement principles: This is especially important in developing countries where Local Content is of great significance to the host country
- In an Operating Company, advance notice that human resources will be required to support the Project during the Project Cycle, especially to ensure coordination on a Brownfield Project.
The Gatekeeper may make any of the following decisions:
- Allow the Project to proceed to the next Stage;
- Place the Project on hold;
- Kill the Project; or
- Recycle through the current Stage, i.e., send the Appraise Stage DSP back to the Project Leader for amendments, as he/she deems necessary to strengthen the package and business case.
Ultimately, proceeding to the next Stage requires the Gatekeeper’s approval.
2.3.2 Select Stage
In the Select Stage, the Concepts/Options developed and approved by the Stage 1 (Appraise Stage) Gatekeeper are examined in far greater detail to select the single Concept/Option that would go past the Select Stage Gatekeeper to the Define Stage.
Typically in the Select Stage, there will be a deep dive into all the elements described in the Appraise Stage, but in addition, the Project business objectives, vision and mission, and the final selection of Project Drivers are detailed.
The Select Stage DSP essentially specifies the preferred Concept/Option to be further detailed and developed for Project Sanction in the Define Stage.
In the main, the activities in the Select Stage include:
- Finalize the Project Charter;
- Update the Project Execution Plan (PEP);
- Further enhance (i.e., almost 100% complete) the Overall Project Risk Register and therefrom identify the Top Ten Risks and their mitigation strategies. Some Owners wish to see this displayed as a Project Risk Matrix, accessible to the Owner on-line;
- Develop a detailed Risk Management Plan that lays out the monitoring, implementation, and feedback process to ensure the identified risks are effectively managed;
- Detailed (Specialist) review of Lessons Learned from similar Projects and which have to be considered in the early engineering;
- Select the final VIPs. On some Projects, it is more efficient from a cost and availability of experts points of view, to hold a workshop to finalize the selection of Drivers from Lessons Learned and which VIPs would be applied to the Project Life Cycle;
- Select Technology. Also considered is how the Technology is to be integrated into existing Operating plants in a Brownfield situation, or for Greenfield Projects, how the Technology selection would impact requirements for Training, Project Documentation, and Handover;
- Develop an Assurance Register;
- If a Brownfield Project, as part of the integration of the Project into Operations, a Management of Change (MOC) procedure is required. For some years now, the technology has moved to e-MOC, which makes the process easier to administrate. The MOC is required to ensure that the Operations Group is able to plan effectively to take over the Commissioning, Start-Up, and Commercial Operations of the new (or additional) Plant, e.g., review manpower levels, warehouse management, new Technology;
- Develop Contracting Strategy (Including Local Content);
- Clearly define a Pre-Commissioning and Commissioning Strategy, including Training and Hand Over Documentation;
- Prepare Pre-FEED Invitation to Bid (ITB) package, bid, evaluate, and award, and then undertake Pre-FEED work to produce a Basic Engineering Package (BEP) that would inform the FEED Scope to be performed in the next Stage (Define). Selection of Technology for a Petrochemical Process Plant would be finalized in the Pre-FEED work;
- Prepare Class 3 (+/- 30%) CAPEX Estimates;
- Update the Financial Model to reflect more accurate Class 3 Estimates;
- Identify long-lead Procurement items; prepare purchase requisitions and obtain preliminary cost and delivery schedule from major equipment vendors. This information is fed into the Class 3 Select Stage CAPEX estimates and Level 2 Project Master Schedule (PMS);
- Complete a Level 2 PMS that will show the overall Project broken down into its major components and will include the Level 1 information expanded to show activities by area or major items of capital equipment. Very importantly, the Level 2 Schedule should show the Project Critical Path and also the Project Sub-Critical Paths. It would be necessary to utilize the services of an independent expert Schedule Analyst to produce a Schedule Report that would be submitted along with the Level 2 PMS. Such an expert would provide the requisite due diligence to the identified Project critical and sub-critical paths, and the logic used in the derivation of the Schedule. This due diligence is a valued input into the Project Risk identification and management and overall Project Success;
- Perform Monte Carlo analysis of the Class 3 Estimate and Level 2 PMS to ensure that the cost structure is fit-for-purpose and that the appropriate cost and schedule contingencies are included;
- On a Brownfield project, prepare an Interface Management Plan in consultation with the Operations representatives to ensure any possible TAR activities are optimized to facilitate Project Tie-Ins;
- Prepare an ITB for FEED Scope; identify a list of qualified potential EPC Contractors;
- Identify Major Project Milestones;
- Prepare Procurement Packages based on expected Equipment Selection from the Pre-FEED Scope. This would be a major input into the Cost Estimate and Execution Schedules;
- Prepare preliminary Work Breakdown Structure (WBS) to be included in the Preliminary PEP; and
- Prepare Preliminary Project Document Handover Plan.
At the end of the Select Stage, the Gatekeeper will not approve the Project to proceed to the next Stage (Define) unless he or she is satisfied that the Select Stage work and Report Outcomes fully satisfy the Select Stage Criteria.
2.3.3 Define Stage
The main focus of the Define Stage is to complete the various areas of work performed in the Select Stage and finalize all documentation required to support Project Sanction.
The main activity sets in this Define stage are:
- Execute FEED Scope;
- With the FEED completed, request equipment manufacturers to review any previous quotations for cost and delivery schedule. The updated quotations should be market-ready such that, in the event a decision is taken, post-Sanction, to place orders for long-lead items, these POs could be released immediately. The revised equipment Cost and Delivery Schedules would be a major input into the overall Project Cost and Master Schedule;
- Develop an ITB for the EPC works to be undertaken in the next (Execute) Stage. If the Owner does not have a qualified stable of personnel to perform a cold eyes review, an independent reputable Project Management and claims consulting company with the appropriate level of EPC contract preparation and claims analysis and management experience should be retained to review the proposed ITB and the Pro-Forma EPC Contract to ensure that these important documents contain the appropriate contract language/clauses needed to minimize change orders and potential delay and disruption claims. If this due diligence step is bypassed, especially on major international EPC works, there are likely to be difficulties in defending against delay and disruption claims later in the Project;
- Bid the EPC works;
- Evaluate the bids and the contractor’s proposed execution plans, and determine the choice of EPC Contractor. These results would feed into the revision of the overall Project Costs and Master Schedule. Engage the independent Project Management and claims consulting company to provide QA/QC over the bid evaluation process and any exceptions to the Owner’s Pro-Forma Contract, etc., that may have been detailed in the response to the ITB by the EPC Contractors. Examine carefully the Bidders’ proposed Commissioning Schedule, Handover Documentation, Project Execution Plan (ensure usage of Systems Approach for Mechanical Completion), and Training Proposals (including provision for Owner’s personnel in the Contractor’s Home Office during Engineering Works to assure effective transfer of technology), etc.;
- Update Cost Estimates to Class 2 (+/-15%) and establish Control Budget;
- Complete Monte Carlo analysis of Cost and Schedule;
- Finalize the Financial Model. Ensure that all ROI-impacting parameters have been rigorously tested to ensure that the Model is able to demonstrate the ROI Hurdle Rate over different sensitivities. On most major Hydrocarbon Projects, the minimum hurdle rate is 15–20%;
- Determine Appropriate Contracting Strategy and Contracting Plan;
- Finalize Project Execution Plan (PEP) and Procedures. Particular attention would be given to managing the interface with Operations on a Brownfield Project;
- Identify regulatory and permitting requirements and make applications for approvals;
- Complete the Level 3 Project Schedule. Utilize the independent reputable Project Management and claims consulting company to perform a quality assurance review of the EPC schedules to ensure the logic is appropriate and to determine the overall Project Critical Path and as well the many sub-critical paths. In this review, the Consultant would also investigate the Contractor’s use of Schedule constraints, existence of missing activity logic, inclusion of the full scope of work, reasonableness of the critical and near critical paths, etc. This due diligence step is a critical success factor in ensuring that, in the event of delay and disruption claims, the Project Leadership is well positioned to have the requisite analyses conducted against the As-Bid Cost and Schedule;
- Perform preliminary HAZOP, HAZID, etc.;
- Update the Risk Register;
- Complete the HSSE Plan, identifying project Metrics like Lagging and Leading Indicators; develop Control of Work (COW) procedures to ensure safety of personnel and equipment during the Execute Phase;
- Update list of Major Milestones;
- Prepare a preliminary Pre-Commissioning, Commissioning, and Start-Up Procedure;
- Complete Quality Assurance/Quality Control (QA/QC) Plans;
- Complete Project Control Procedures (Cost Monitoring & Control, Change Order Management including Cost Engineering, Planning & Scheduling, Contracts Administration, etc.);
- Freeze Project Scope;
- Complete e-MOC;
- Propose a Document Management System (DMS). On any Project, such a repository of Project Information is critical but particularly on a large complex Project, its establishment is most important. Access to design information, construction issues, equipment evaluations, etc. are just a few examples of information that would be greatly needed by Operations post-Handover. Because of the sheer volume of documentation on a large Project, it may be prudent to consider a DMS that has operands (after barcoding the documents) to facilitate easy retrieval. It is a most challenging task to retrieve information from a manual system in a large room with countless filing cabinets;
- Prepare the Certificate of Environmental Clearance (CEC);
- Prepare Preliminary Emergency Response Plan; and
- Complete the Project Execution Plan (PEP). This Plan would of necessity contain all the elements required to provide assurance to the Select Stage Gatekeeper that the Project can achieve Project Sanction.
At the end of the Define Stage, the Gatekeeper will not approve the Project to proceed to the next Stage (Execute) unless he or she is satisfied that the Define Stage work and Report Outcomes fully satisfy the Define Stage Criteria. The end of the Define Stage represents a major Milestone on the Project as approval to move to the Execute Stage effectively sanctions the Project to commence major CAPEX expenditures. The achievement of Project Sanction is a Major Milestone on the Project and as shown in the earlier Charts, it signals the transition of influence from the Gatekeepers to the Project Leader/Director and the Project Leadership Team.
2.3.4 Execute Stage
In this Stage, the major activity is the EPC execution. Arguably, depending on the jurisdiction in which the Project is being undertaken, the first Project Execution strategy is to immediately apply for a CEC (Certificate of Environmental Clearance), since the approval could require as long as 6‑8 months.
The Project Execution strategies in this stage typically are shown below (not in sequential order as many are executed concurrently) and include those that are either the responsibility of the EPC Contractor or the Owner’s Project Leadership Team:
- Award the EPC Contract. Again, ensure that the independent Project Management and claims consulting company reviews the final EPC Contract documents prior to their execution. An often-overlooked clause or requirement (or one that is properly specified) in the Contract documents is Project Handover Documents. A follow-up article will provide a comprehensive overview of how important getting this right is on any Project.
- Finalize the Level 4 and Level 5 schedules. Ensure that the EPC Contractor submits an As-Planned (AP) Schedule in electronic format as part of its Bid Documentation. The importance of this requirement cannot be overstated, since all subsequent schedule updates submitted by the Contractor for the duration of the EPC works will be compared to the AP Schedule;
- Ensure all HSSE metrics are monitored and that all Site Works are executed within the Control of Work (COW) procedures;
- Ensure that the EPC Contractor submits not only a Monthly written report but also an electronic copy of its updated Project schedule. This would allow its continuous interrogation by the Owner’s schedule expert against the As-Planned Schedule to determine changes in logic, or activity duration, whether the original critical path has changed, whether sub-critical paths are about to become critical path (i.e., zero schedule float), whether any Contractor’s claims for an extension of time and compensable delay can be robustly defended by the Owner, etc. This type of quality feedback allows the Project Leader/Director to make important decisions on the basis of factual information. From the start of EPC Works when the schedule is all As-Planned, each monthly reporting period or window would progressively show the Schedule becoming more As-Built (AB) and less As-Planned (AP);
- Confirm the EPC Work Breakdown Structure (WBS). It is against this structure that all EPC payments will be made; therefore, the Project Leadership must ensure that its Team is properly resourced to provide a third eye on daily progress or lack thereof, and the associated reasons for delays, etc. Failure to set this up with the right level of construction experience would inevitably lead to challenges in defending against delay and disruption claims;
- Confirm Contractor’s design of the Systems Handover process to Mechanical Completion. Very importantly, ensure that the contents of each Systems Turnover Package are agreed very early in the commencement of EPC Works. Agree on the process by which punch list items are corrected;
- Review Contractor’s Plan for pre-Commissioning, Commissioning, and Start‑Up;
- Perform RAM (Reliability, Availability, and Maintainability) analysis for all Rotating Equipment;
- Develop process Control Alarm Management System, including Cause and Effect Diagrams;
- Complete an Emergency Response Plan: Test on a periodic basis. This is especially critical on Brownfield Projects where hot work is performed either in or close to Operating Facilities;
- Confirm all required piping and other (e.g., Control Systems, Fire Systems) Tie‑ins;
- Review the Performance Test Procedure, including metrics for Final Certificate of Completion and Formal Project Hand-Over;
- Develop Design Drawings to IFC Status;
- Procure all Equipment and Material;
- Initiate QA/QC Procedures. Set up Third Party Inspection Plan, if procurement is being done Offshore. This is very important on Projects where special materials of construction are being utilized and the testing requirements are onerous;
- Conduct HAZOPs, HAZIDs, and Constructability Reviews, etc.;
- Ensure HAZOP, HAZID, and Constructability Review Outputs are properly documented and all required changes implemented. As part of QA/QC, ensure that all items for action are closed out in the approved manner as per QA/QC procedures;
- Review Construction Plans, based on Constructability Reviews, etc.;
- Prepare, Bid, Evaluate, and Award Construction ITB Packages;
- Construct the Project Facilities;
- Ensure that overall Project Progress is documented via Monthly Reports from the EPC Contractor;
- Initiate the Change Management Process (e.g., e-MOC), with particular focus on the management of the Project Interface with Operations, if a Brownfield Project;
- Ensure that the Transfer of Technology Plan proposed by the EPC Contractor is being followed, particularly in respect of assignment of Owner resources in the EPC Contractor’s Home Office;
- Ensure, by working with Owner Operations, that an Asset Reporting System is developed in alignment with Owner’s Operations Practice, e.g., Equipment Numbers;
- Ensure that the Project Controls Unit under the Project Leader/Director is properly resourced to begin work right from the get-go.
- Obtain Regulatory Approvals;
- Set Up Document Control System, including a Manager with the relevant experience;
- As changes are made on various documents (e.g., P&IDs, PFDs, Piping Isometrics, GA drawings, One-Line Electrical Diagrams, etc.), ensure that all changes are redlined and maintained in a Document Management System (DMS) that has controlled access. This is very important as at the end of the Project, all verified changes must be incorporated into the final As-Built documentation, which would be critical to safe operation of the facilities;
- Complete O&M Manuals. The use of English is the international standard and it should be specified. If the EPC Contractor is from a non-English speaking country, the Contract documents should mandate that there be a translator versed in technical English. On an international project, this precautionary step was missed, leading to immense problems with the quality of the O&M manuals;
- Execute Training Program for Operations Personnel. Ensure adequate provision for vendor training and, as well, utilize any opportunities for Owner Operations personnel to be seconded into similar plants for hands-on training. This is of particular relevance when the project is based on new Technology, where no similar facility is available in the country in which the Project is being undertaken;
- Ensure the Contractor is approaching Mechanical Completion (MC) on the basis of Systems Approach methodology, as this is the proven way to achieving MC and Commissioning and Start-Up in the shortest time from the commencement of EPC works;
- Monitor the Progress of Project Handover Documentation. If not done in parallel with the EPC works, this activity is often rushed at the end of the Project, leading to disputes over the quantity and quality of such documentation.
- Regular Weekly Meetings with the EPC Contractor and other Stakeholders, led by the Project Leader/Director. There should be a base Agenda for the Weekly Meeting comprising as a minimum: Project Schedule showing progress on all items for the past week; a 2 or 3‑week look ahead, that takes cognizance of workarounds to maintain the overall Project Master Schedule; HSSE Metric Performance (Leading and Lagging Indicators, Control of Work); Change Order Log Review; Request for Information (RFI) Log Review; WBS review (at the end of the month, the Contractor’ submission for pay, based on its Earned Value from the WBS, should not be contentious if the progress is confirmed by the Owner); Sub-Contractor Performance; Operations Issues; Project Documentation Handover; O&M Manual preparation progress; Vendor Progress on Major Equipment; On-Site Construction Issues; and Industrial Relations Issues.
- Achieve Mechanical Completion of each System; ensure Punch list is developed with Operations input (i.e., Operations is part of the Systems Walk down Teams); ensure Turnover Package Documentation is as per Contract requirements;
- Achieve Overall Mechanical Completion;
- Complete Pre-Commissioning; with the application of Systems Methodology for Mechanical Completion, it is usual to be able to first commence Pre-Commissioning on certain Utilities Systems;
- Complete Commissioning; ensure Pre-Start-Up Review is conducted. On most Brownfield projects, the Commissioning and Start-up is performed by Owner Operations personnel;
- Start-Up and Complete Performance Test; ensure all Performance Test Data are compiled and reviewed by Operations experts to confirm that the Plant is performing as per Nameplate (Design); and
- Handover the Project to Owner Operations.
2.3.5 Operate Stage
Following a successful Plant Performance Test, and Project Handover, the Owner Operations Team assumes control of the Operating Facility.
However, as shown on Figure 5, the involvement of the Project Leadership Team is not yet done as in the Operate Stage, several important activities have to be concluded, viz:
- Complete Outstanding Contractual Work, including Punch List items;
- Publish official As-Built Project Master Schedule;
- Finalize agreement on all Contract Issues, e.g., Delay and Disruption Claims, Change Order Costs;
- Close Out all Contracts;
- Capture Key Project Lessons Learned;
- Complete Performance Analysis of Project Controls vs. Agreed Metrics;
- Utilize an independent consultant to establish the final benchmark performance rating of Project;
- Ensure Document Management System is effectively functioning with the correct operands, if an electronic system was implemented at the inception of the Project;
- Complete As-Built Documentation;
- Complete Vendor Testing and Documentation;
- Conduct assessment of the Management Performance of the Project Leadership Team and provide feedback to those human resources;
- Ensure transition of remaining Project material in the project Warehouse to the Owner’s Warehouse System; dispose of any material deemed irrelevant to the Owner’s needs;
- Ensure that Owner Accounting incorporates all Project Assets into its Financial System;
- Prepare and publish a Project Investment Appraisal (PIA) that compares Project performance against the Project Performance Metrics as established at Project Sanction. This report would also contain final Cost information on all monies expended on the project, including All Contracts, Equipment Purchase, and Project ROI, etc. The PIA is essentially the Final Project Close-Out Report.
3. CONCLUSION
Large oil refinery, petrochemical, and offshore oil and gas projects are hugely cost-intensive and the efficient development and execution of these mega-projects can often make the difference between a company going bankrupt or, at a minimum, experiencing serious negative financial in-flows due to schedule delays that lead to huge claims and increased costs.
On an LNG plant in 1995, for example, the cost efficiency may have been $250–$300/tpa in jurisdictions with fairly well established local construction and process plant operating capability. In 2015, however, in jurisdictions with new discoveries of natural gas, where there is no similar experience, the cost efficiency could be as high as $3,000/tpa. A world class Ammonia plant requires a CAPEX expenditure of close to $2–2.5 billion, similar to that required for a Methanol plant.
It should, therefore, be patently clear that tried and proven EPC Project Management Processes, if properly followed as outlined above, would result in a successful project, with a minimum of claims and cost and schedule overruns.
This article provides guidelines for effective Project Implementation. If an Owner company desires to implement a Stage Gate project Management System, an independent consultant with hands-on experience setting up such a system starting from a blank sheet should be engaged.
About the Author
S. Andrew McIntosh is a Senior Principal with Long International and has nearly 50 years of engineering, construction, onshore and offshore oil and gas operations, and management consulting experience. He has extensive international greenfield and brownfield project development and execution experience in diverse areas such as refinery, petrochemical, offshore oil and gas, LNG, oil and gas pipelines, and ferrous metallics projects ranging from US$20 million to US$1.8 billion. Before joining Long International, Mr. McIntosh served as President of The Natural Gas Company of Trinidad and Tobago. He also served as a Senior Operations Advisor, Vice President – Operations, and Vice President – Technical Services for several international energy companies. Mr. McIntosh has extensive experience in the development of Project Management and Project Execution Plans and Procedures, Stage Gate processes for Project Development, and the analysis and resolution of engineering and construction claims involving disputed change orders, schedule delay, and loss of productivity claims. Mr. McIntosh is based in Cascade, Port-of-Spain, Trinidad and can be contacted at amcintosh@long-intl.com and (868) 374-7717.
Copyright © Long International, Inc.
ADDITIONAL RESOURCES
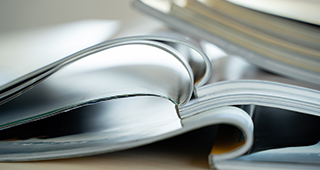
Articles
Articles by our engineering and construction claims experts cover topics ranging from acceleration to why claims occur.
MORE
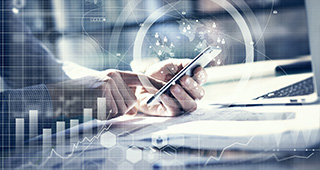
Blog
Discover industry insights on construction disputes and claims, project management, risk analysis, and more.
MORE
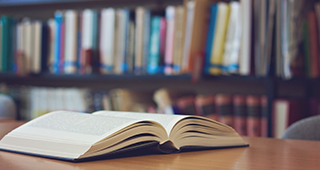
Publications
We are committed to sharing industry knowledge through publication of our books and presentations.
MORE