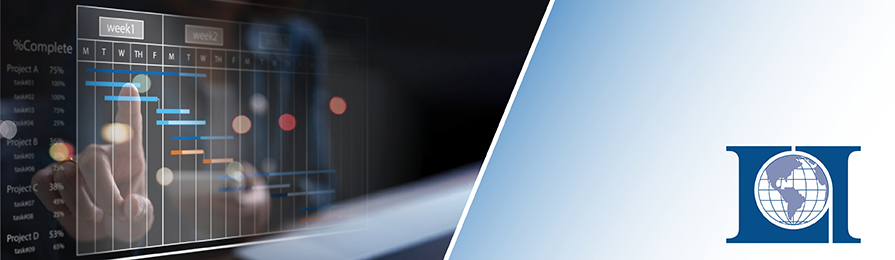
Lessons Learned from Megaproject Delay Claims
This article details the support required for schedule delay claims, incorporating lessons learned from four megaproject delay claims. Specifically, the article addresses using appropriate schedule delay methodology, properly incorporating baseline schedule information, resolving obvious budgeted labor hour discrepancies, and reconciling planned quantity conflicts.
1. INTRODUCTION
Megaprojects are generally defined as very large, complex engineering and construction projects with costs usually exceeding $1 billion. These challenging ventures typically take years to plan and execute, involve a multiplicity of private and public stakeholders, require a vast number of resources and equipment to construct, and impact millions of lives. Some examples include hospitals, airports, mass transit roadway and rail systems, hydroelectric dams, nuclear power plants, pipelines, tunnels, canals, aircraft carriers, cruise ships, seaports, offshore oil and gas extraction, oil sands bitumen extraction, onshore refineries, and liquified natural gas (LNG) plants.
Schedule delay is an all-too-common problem on megaprojects, typically resulting in extended project durations and cost overruns for one or many project participants and stakeholders. In an Ernst and Young study that evaluated project performance based on cost and schedule, most megaprojects faced schedule delay and cost overruns when measuring performance against initial cost estimates and schedule baselines. The study, which surveyed 365 megaprojects in industry segments such as upstream, LNG, pipeline, and refinery projects, showed that 73 percent of megaprojects studied experienced or would experience schedule delay.1 The contractor and/or one or more of its subcontractors is almost always the party submitting a schedule delay claim.
Schedule delay claims must meet several legal and industry requirements to be valid. Although the contract documents between the owner and contractor typically specify these requirements, some basic principles for a contractor to prove schedule delay, regardless of project size, include the following:
- Select an appropriate and supportable schedule delay analysis methodology;
- Use contemporaneous project records as a basis for support;
- Identify and resolve conflicts between supporting project records;
- Demonstrate that the delay extended the completion of the contractor’s contract;
- Provide evidence that the owner or a force majeure event caused the delay;
- Consider any concurrent contractor-caused delay;
- Quantify the amount of delay the owner caused; and
- Prove that the owner caused damages from the delay that it caused.
The author analyzed several megaproject delay claims, but the delay allocation to the responsible parties and claim validity were questioned because of the following issues:
- The contractor selected an inappropriate and least rigorous schedule delay analysis methodology in support of its delay claims.
- The contractor claimed critical delay to the start of its tank installation works but failed to consider baseline schedule available float to that work.
- There were large, unexplained budgeted labor hour discrepancies between the contractor’s contemporaneous progress status reporting and its approved baseline schedule and subsequent monthly schedule updates impacted by alleged critical schedule delay.
- The contractor’s claimed planned quantities for ground improvement did not reconcile with its corresponding planned quantities in its baseline schedule.
The purpose of this article is to provide insight and awareness regarding the required support for schedule delay claims, based on these four examples and using the appropriate schedule delay methodology, properly incorporating baseline schedule information, resolving obvious budgeted labor hour discrepancies, and reconciling planned quantity conflicts.
2. THE CONTRACTOR SELECTED AN INAPPROPRIATE SCHEDULE DELAY ANALYSIS METHODOLOGY
The contractor inappropriately used a simple as-planned versus as-built schedule comparison to quantify alleged critical path delays during the execution of site development installations on an extensive EPC refinery project. The contractor entered into an agreement with the owner to perform site development works. The site development scope was called the Site Development Work Package No. 1, or more simply the “SD-1 Work Package,” and included clearing, grubbing, site improvement, earthwork, drainage, roadways, and hardstands.2 The SD-1 Work Package had eleven distinct service areas (“SAs”) that defined specific work areas for the overall plant. Table 2-1 below summarizes the SAs.
Table 2-1: Listing of Service Areas
Service Area Reference | Service Area Description |
---|---|
SA-1 | Site Access and Roadway |
SA-2 | Dock Area |
SA-3 | Temporary Facilities |
SA-4 | Plant Operations |
SA-5 | Module Offloading |
SA-6 | Tanks |
SA-7 | Gas Trains |
SA-8 | Onsite Power Generation Plant |
SA-9 | Tanks |
SA-10 | Tankage and Inlet Flare |
SA-11 | Balance of Plant |
The contractor claimed schedule delay due to impacting issues that stemmed from alleged differing site conditions. As a result, the contractor sought a contract time extension for the relief of owner-assessed liquidated damages as well as recovery for its extended project overhead costs. The contractor’s schedule delay expert quantified delay by first identifying the critical path activities based on the contractor’s approved baseline schedule. The expert then compared actual performance, i.e., as-built dates and as-built sequencing, against the contractor’s initial critical path activities.
The expert used a delay analysis consistent with the Association for the Advancement of Cost Engineering International’s (AACEI) Recommended Practice 29R-03 (RP 29R-03) Method Implementation Protocol 3.1 (MIP 3.1). MIP 3.1 is also known as the “as-planned versus as-built schedule analysis,” which is the most simplistic and least rigorous schedule delay analysis methodology available for forensic schedule delay analyses. RP 29R-03 states the following about using MIP 3.1 as a schedule delay methodology:
L. Summary of Consideration in Using Minimum Protocol
- Suitable for analyzing short projects with minimal logic changes.
- Can be performed in a manner that is easy to understand and simple to present.
- Technically simple to perform compared to other MIP’s.
- Can be performed with very rudimentary schedules and as-built data.
- As-built activities must be closely correlated with as-planned activities.
- As-built data used must be accurate and validated.
- Does not, by itself, identify the as-built critical path.3
Further, RP 29R-03 lists several limitations in the use of MIP 3.1 schedule delay methodology:
M. Caveats in Using the Minimum Protocol/Conditions Requiring Enhanced Protocols
- Not suitable for project durations extending into multiple dozens of update periods.
- Not suitable for projects built in a manner significantly different than planned. The rate of error increases as the incidence of change increases.
- Not suitable for complicated projects with multiple critical paths.
- Does not consider the possibility of critical path shifts either within periods or across the project.
- Susceptible to unintentional or intentional manipulation by choice of as-built data that is incorporated into schedule.
- May fail to identify all critical delays or time extensions, and typically does not adequately consider concurrency and pacing issues.
- Does not consider that changes to original baseline schedule may have been the actual cause of delay instead of the identified delay issues.
- Typically fails to consider chronological order of delays or reconcile periodic planned critical path shifts with the as-built critical path.
- Not suited for clearly demonstrating acceleration.4
Many of the limitations listed above applied to the SD-1 Work Package. First, the as-planned versus as-built schedule delay analysis is not appropriate for a long-duration project. The contractor’s approved baseline schedule for the SD-1 Work Package had a planned duration from May 2016 to October 2018, or approximately 30 calendar months (i.e., 2.5 years). In effect, each SA was its own project, and the contractor planned to work multiple areas in parallel. The 30 month baseline duration does not fit within the MIP 3.1 definition of a short project.
Second, the SD-1 Work Package was not a simple project with minimal logic changes; it was complex, with eleven SAs that spanned a large and diverse geographic area with a total area of approximately 4.5 square miles. Again, each SA was effectively its own project, and the contractor planned to work multiple SAs in parallel. Comparing the contractor’s baseline schedule and as built schedule files showed significant differences in terms of number of work activities and logic relationships. Table 2-2 below shows the comparison.
Table 2-2: Comparison of Number of Activities and Logic Relationships
between Contractor’s Baseline and As-Built Schedules
Description | Baseline Schedule | As-Built Schedule | Variance (As-Built Minus Baseline) | Amount of Change to Baseline (Variance/Baseline) |
---|---|---|---|---|
Number of activities in schedule file | 1,264 | 3,690 | 2,426 | 192% |
Number of logic relationships in schedule file | 2,840 | 7,080 | 4,240 | 149% |
The amount of change between the baseline and as-built schedules was substantial. The as-built schedule had 2,426 more activities or approximately 192% more activity detail than the baseline schedule. A review of the as-built schedule work activities revealed added schedule detail for missing original scope, expanded original scope, change order activities, system testing, turnover, and punch list activities. Further, the as-built schedule had 4,240 additional logic relationships, or 149% more logic detail. This significant amount of change between the two schedule files is inconsistent with the recommended guidelines for using MIP 3.1.
Third, reliance on a simple as-planned versus as-built comparison was discredited because the overall critical path changed repeatedly in schedule updates after the contractor’s initial baseline schedule. The contractor submitted 35 schedule updates, with the last one identified as the as-built schedule. Based on the contractor’s contemporaneous monthly updates, the driving critical path activities jumped from one SA to another. The MIP 3.1 schedule delay methodology does not adequately consider critical path shifts as contained in contemporaneous updates. Although the schedule delay expert could have analyzed shifting critical paths from update to update, the expert neither identified nor considered critical path shifts that were different from the critical path in the baseline.
Last, the MIP 3.1 schedule delay methodology does not allow for a proper assessment of concurrent delay. Concurrent delay is generally defined as:
Two or more delays that take place or overlap during the same period, either of which occurring alone would have affected the ultimate completion date. In practice, it can be difficult to apportion damages when the concurrent delays are due to the owner and contractor respectively.5
Based on the contractor’s contemporaneous monthly updates, not only did the driving critical path activities jump from one SA to another, most of the schedule delay and slippage on critical path activities throughout project execution lacked any causal linkage to the differing site condition issue that the contractor alleged was the primary cause of delay. The contractor’s schedule updates were replete with unexplained and/or concurrent, contractor-caused delay.
The contractor’s schedule delay expert had the obligation to identify, explain, justify, and/or allocate responsibility for unexplained and/or concurrent delays that the owner may or may not have caused. More appropriate schedule delay analysis methodologies utilize month-to-month schedule files and model impacts including concurrent delay on specific work activities for various windows of time.6 The omission of any analysis of obvious unexplained and/or concurrent, contractor-caused delays found in the contractor’s contemporaneous critical paths rendered the schedule delay analysis incomplete, inaccurate, and unsupportive of entitlement to a compensable delay.
3. THE CONTRACTOR INCORRECTLY CLAIMED CRITICAL DELAY TO THE START OF ITS TANK INSTALLATION WORKS BY FAILING TO CONSIDER AVAILABLE FLOAT IN THE BASELINE SCHEDULE
The contractor claimed critical delay to the start of its propane and butane tank installation works within a sub-area of a large refinery project. The claimed critical delays were based on a comparison of owner-responsible handover dates to actual handover dates. The contractor’s schedule delay expert identified the specific area access handover dates as represented by milestone activities within the contractor’s approved baseline schedule. This baseline schedule was included as an attachment to the signed contract agreement between the owner and contractor.
The actual area access handover dates were obtained from the contractor’s final monthly schedule update that contained as-built schedule date information. Table 3-1 summarizes the contractor’s claimed critical delay in calendar days (“CDs”), as quantified by its schedule delay expert, to the start of its propane and butane tank installation.
Table 3-1: Critical Delay Days to the Start of Propane Tank
and Butane Tank Installation
Description | Contractual Required Area Access Date or Start of Delay | Actual Area Access Date or End of Delay | Contractor-Claimed Delay in CDs |
---|---|---|---|
Delayed propane area handover | 01 August 2019 | 06 November 2019 | 97 |
Delayed butane area handover | 01 October 2019 | 11 January 2020 | 102 |
The contractor’s baseline schedule, a 25-page color printout in Primavera Project Planner (P6) tabular and bar chart format with a 30 April 2019 planned start date, represented the planned work activities that detailed the installation scope needed to complete the propane and butane tanks. P6 was the scheduling software that the contract documents required. Unfortunately, the electronic P6 schedule file (i.e., *.XER) for the baseline schedule was not available for further review. In the P6 tabular printout, the contractor’s baseline schedule had the following visible schedule data for each activity:
- Activity ID
- Activity description
- Original duration
- Early start date
- Early finish date
- Total float
The baseline schedule data was organized by groups of work such as key milestones, early works, civil works, foundations, tank installation, electrical, instrumentation, testing, and pre-commissioning. The specific baseline schedule handover activities included activity 7000-Access (“Area Access Handover by Owner – Propane Tank”) and activity 8000-Access (“Area Access Handover by Owner – Butane Tank”). Activities 7000-Access and 8000-Access were both start milestone activities. Activity 7000-Access had a planned start date of 01 August 2019, and activity 8000-Access had a planned start date of 01 October 2019.7 Table 3-2 summarizes the baseline schedule data with planned early start dates for activities 7000-Access and 8000-Access.
Table 3-2: Activities 7000-Access and 8000-Access Planned Early Start Dates
P6 Activity ID | P6 Activity Description | Planned Early Start Date8 |
---|---|---|
7000-Access | Area Access Handover by Owner – Propane Tank | 01 August 2019 |
8000-Access | Area Access Handover by Owner – Butane Tank | 01 October 2019 |
Although the contractor’s printout of the baseline schedule did not include corresponding planned late start date information, it did include total float values for all baseline schedule activities. The specific total float values for both activities 7000-Access and 8000-Access equaled 131 workdays (“WDs”).9 The planned late start dates were calculated based on the planned early start dates and corresponding planned total float values.10 Table 3-3 below summarizes the planned early start dates, planned total float values, and calculated planned late start dates.11
Table 3-3: Activities 7000-Access and 8000-Access Planned Early Start Dates,
Planned Total Float, and Calculated Planned Late Start Dates
P6 Activity ID | P6 Activity Description | Tank Ref. | Planned Early Start Date | Planned Total Float in WDs | Calculated Planned Late Start Dates |
---|---|---|---|---|---|
7000-Access | Area Access Handover by Owner – Propane Tank | Propane | 01 August 2019 | 131 | 31 January 2020 |
8000-Access | Area Access Handover by Owner – Butane Tank | Butane | 01 October 2019 | 131 | 01 April 2020 |
Based on the contractor’s last monthly schedule update file, the actual area access handover dates for activities 7000-Access and 8000-Access were 06 November 2019 and 11 January 2020, respectively. The table below compares the planned early start dates, calculated planned late start dates, and actual dates along with a calculated variance in calendar days between actual dates to early dates and actual dates to late dates.
Table 3-4: Comparison of Planned Early, Late, and Actual Dates
for Activities 7000-Access and 8000 Access
P6 Activity ID | P6 Activity Description | Planned Early Start Date | Planned Total Float in WDs | Calculated Planned Late Start Dates | Actual Start Date | Variance from Actual to Early Date in CDs | Variance from Actual to Late Date in CDs |
---|---|---|---|---|---|---|---|
7000-Access | Area Access Handover by Owner – Propane Tank | 01 August 2019 | 131 | 31 January 2020 | 06 November 2019 | 97 | (86) |
8000-Access | Area Access Handover by Owner – Butane Tank | 01 October 2019 | 131 | 01 April 2020 | 11 January 2020 | 102 | (81) |
As shown above, the contractor received actual area access for the propane tank on 06 November 2019, which was 97 calendar days after its early planned start date of 01 August 2019 and 86 calendar days before the calculated planned late start date of 31 January 2020. Further, the contractor received actual area access for the butane tank on 11 January 2020, which was 102 calendar days later than the planned start date of 01 October 2019 and 81 calendar days earlier than the planned late start date of 01 April 2020. The following table summarizes the contractor’s claimed critical delay in calendar days, as quantified by its schedule delay expert, and the calculated delay based on the contractor’s planned late start dates of its propane and butane tank installation.
Table 3-5: Critical Delay Day Comparison to the Start of Propane Tank
and Butane Tank Installation
Description | Contractor-Claimed Critical Delay in CDs | Delay Based on Contractor’s Planned Late Start Dates in CDs |
---|---|---|
Delayed Propane Area Handover | 97 | (86) |
Delayed Butane Area Handover | 102 | (81) |
When considering the contractor’s planned late start dates as derived from its planned early start dates and corresponding total float values in its approved baseline schedule, the owner provided actual area access for the propane tank and butane tanks before the actual access would have caused any critical delay. Having failed to consider available total float for these two area access milestone activities, the expert incorrectly claimed critical delay. The owner did not cause critical path access delay to the propane tank and butane tank installation works.
4. A DISCREPANCY BETWEEN THE CONTRACTOR’S REPORTED BUDGETED LABOR HOURS AND BUDGETED LABOR HOURS ASSIGNED TO SCHEDULE ACTIVITIES WAS UNEXPLAINED
The contractor alleged schedule delay and disruption to its sitework installation and subsequent utilities and building works due to encountering hard rock excavation greater than originally planned. The owner engaged the contractor to perform engineering, procurement, fabrication and delivery, construction, installation, pre-commissioning, and commissioning of numerous support buildings for a large refinery project. The contractor asserted that based on its initial site inspections and the information provided by the owner, it could not have reasonably expected the full extent of the hard rock material that needed to be ripped, excavated, removed, handled, and transported offsite.
The hard rock was encountered during early bulk earthwork operations and caused significant delay and disruption to the contractor’s cut and fill work activities and subsequent groundwork activities. Once it discovered the hard rock, the contractor responded by stopping to assess the magnitude of the actual hard rock material, submitting an approved rock excavation mitigation methodology, adding additional labor and heavy equipment needed to remove the hard rock materials, and changing its baseline schedule planned sequences to open more work fronts to mitigate schedule delay. The contractor then presented claims for schedule delay, time extension, recovery of compensable delay days, reimbursement for additional labor and equipment, added supervision costs, and loss of labor productivity.
The contractor’s schedule delay expert quantified schedule delay to work activities that the hard rock issue directly or indirectly impacted. The contractor’s approved baseline schedule was used as the key supporting project record for the starting point to measure schedule delay. The expert compared baseline schedule forecasted dates, durations, and logic flow to actual contractor performance for activities impacted by the hard rock issue.
However, the expert failed to identify, reconcile, explain, or consider noticeable labor hour discrepancies between the contractor’s monthly reported budgeted labor hours and the corresponding budgeted labor hours assigned to schedule activities in the contractor’s approved baseline schedule and schedule updates. These unexplained differences cast doubt on the reliability of the contractor’s approved baseline schedule as the starting point for measuring schedule delay.
4.1 PROGRESS PAYMENT PROCESS
The contract documents contained overarching requirements for the contractor to prepare and submit complete and accurate data to plan, schedule, measure, and track progress in the performance of the work. The contractor was to use the scheduling software package Primavera Project Planner (P6). Further, the contract documents required the contractor to submit a resource-loaded baseline schedule with assigned budgeted labor hours to ensure accurate forecasting of start and finish dates for the scopes of work as contained within the planned durations as well as to be used as the basis of monthly progress. In fact, the contractor’s approved baseline schedule contained budgeted labor hours assigned to individual work activities.
The owner and contractor agreed to a payment process that included contractor monthly progress reporting, as reflected by percent complete values obtained from individual work activities in the contractor’s P6 schedule files. The contractor exported its monthly P6 schedule progress data into a progress payment spreadsheet that computed monthly progress percentages.
These percentages were then applied to details in the contractor’s construction status reports, which included data on units of work, quantities, labor hours, and weighted percentages assigned to work types. These progress reports included columns that allowed for the calculation of progress using quantities installed multiplied by weighted averages. The reports also included detailed breakdowns of work types consistent with the work types in the baseline schedule.
Therefore, the contractor’s budgeted labor hours in its progress status reporting should have matched or closely correlated to the labor hours in its schedule work activities. The baseline schedule and subsequent schedule updates contained activity coding that allowed for an almost exact correlation to work types in the monthly progress reports. As detailed in the following sections, a significant disconnect was observed between the budgeted labor hours in these reports and the budgeted labor hours in the baseline schedule and subsequent schedule updates.
4.2 SITEWIDE CIVIL WORKS BUDGETED LABOR HOURS WERE OUT OF ALIGNMENT
The budgeted labor hours for civil-related work activities were grouped by work types and summarized. The contractor claimed that the hard rock issue directly delayed and impacted the civil-related work activities. The budgeted labor hours in the monthly progress reports were compared to those in the contractor’s baseline schedule and updates to gauge the level of accuracy and consistency between them. Table 4-1 below compares budgeted labor hours for the work scopes for clearing/grubbing, bulk earthworks, stormwater drainage, roadway infrastructure, landscaping, irrigation, and fencing.
Table 4-1: Comparison of Budgeted Labor Hours
for Sitewide Civil Works by Work Types
Work Type Category Description | Contractor Progress Status Report Work Type | Contractor Progress Status Report Budgeted Labor Hours | Assigned P6 Budgeted Labor Hours per Baseline Schedule and Updates | Budgeted Labor Hour Variance (Progress Report Hours Minus P6 Hours) |
---|---|---|---|---|
Clearing, Grubbing, and Bulk Earthworks | Civil | 17,855 | 7,963 | 9,892 |
Stormwater Drainage for All Buildings | Civil | 10,125 | 4,480 | 5,645 |
Roadway Infrastructure Works | Civil | 19,680 | 12,845 | 6,835 |
Sitewide Landscaping, Irrigation, and Perimeter Fencing | Civil | 9,308 | 4,114 | 5,194 |
Subtotal – Sitewide Civil Works | 56,968 | 29,402 | 27,566 |
As the table above shows, the budgeted labor hours were substantially out of alignment. The progress reports contained considerably more hours than the baseline schedule and schedule updates showed. For example, the clearing, grubbing, and bulk earthworks schedule activities, which the contractor claimed were directly impacted by the rock issue, had 7,963 budgeted labor hours in the baseline schedule and updates, approximately 45 percent of the 17,855 hours in the progress report.
The same trend occurred for stormwater drainage, roadway, landscaping, irrigation, and perimeter fencing work types. Consistently, the hours in the baseline schedule and schedule updates were significantly fewer than those in the progress reports. For the sitewide civil works analyzed, the contractor reported a total of 56,968 budgeted labor hours in its status reports compared to 29,402 hours in the baseline schedule and schedule updates. This is a variance of 27,566 hours, or almost half of the budgeted labor hours in the status reports.
If the hours reported in the status reports were correct, then the hours in the baseline schedule and schedule updates were too low. Therefore, the reliability of the contractor’s planned activity durations and forecasted start and finish dates was questionable. Before any alleged impacts from the rock issue, the sitewide civil works would have experienced significant delay because the original durations were too short because inadequate budgeted labor hours were assigned to work activities. Further, duration delays would cause delay to the start of successor work activities.
4.3 UTILITIES AND IN-GROUND WORKS BUDGETED LABOR HOURS SUBSTANTIALLY DIFFER IN SCHEDULES AND PROGRESS REPORTS
A comparison of budgeted labor hours for utilities and in-ground works for all buildings was performed. Work types for these scopes of work included sitewide wastewater infrastructure, water supply infrastructure, and in-ground services for buildings. Work types also included infrastructure for power, lighting, communication, security, and fire detection. The contractor claimed that the rock issue directly and/or indirectly delayed and disrupted these work types. Table 4-2 below is a comparison summary.
Table 4-2: Comparison of Budgeted Labor Hours for Utilities
and In-Ground Works by Work Types
Work Type Category Description | Contractor Progress Status Report Work Type | Contractor Progress Status Report Budgeted Labor Hours | Assigned P6 Budgeted Labor Hours per Baseline Schedule and Updates | Budgeted Labor Hour Variance (Progress Report Hours Minus P6 Hours) |
---|---|---|---|---|
Wastewater (Sewer) Headworks to Buildings | Utilities | 51,345 | 33,776 | 17,569 |
Water Supply Infrastructure to Buildings | Utilities | 12,365 | 8,920 | 3,445 |
Wastewater (Sewer) Infrastructure to Buildings | Utilities | 15,374 | 14,240 | 1,134 |
In-Ground Services All Buildings | Utilities | 5,632 | 2,890 | 2,742 |
Power & Lighting, Communications, Security, & Fire Detection Infrastructure All Buildings | Utilities | 48,588 | 25,986 | 22,602 |
Subtotal – Utilities/In‑Ground Works All Buildings | 133,304 | 85,812 | 47,492 |
As with the sitewide civil works, the progress reports show considerably more budgeted labor hours than those in the baseline schedule and schedule updates. All work type categories show significant discrepancies, which suggests problems with the baseline schedule and updates.
As a hypothetical example, a contractor budgeted and assigned 10,000 labor hours for a utility installation activity at a planned rate of 80 labor hours per workday in its baseline schedule. This rate was constrained by crew size and available equipment. The planned duration is equal to approximately 125 workdays, i.e., 10,000 assigned labor hours divided by 80 labor hours per workday. If the assigned 10,000 hours were 64 percent of the contractor’s correctly reported hours, then the assigned hours in the baseline schedule needed to increase to 15,625 hours.12 Based on a constrained planned rate of 80 labor hours per workday, the correct planned duration is 196 workdays, not 125.13 The difference is 71 workdays. Thus, the original duration is deficient by 71 workdays due to inadequate assigned hours.
For the utilities and in-ground works, the baseline schedule and schedule updates understated the durations for these work types by the following percentages:14
- Wastewater (sewer) to buildings: 66% of the progress reporting;
- Water supply infrastructure: 72% of the progress reporting;
- Wastewater (sewer) infrastructure for buildings: 93% of the progress reporting;
- In-ground services for buildings: 51% of the progress reporting; and
- Power, lighting, communications, security, and fire detection infrastructure: 53% of the progress reporting.
The progress report hours totaled 133,304, while the baseline schedule and schedule update hours totaled 85,812. The baseline schedule and schedule updates had 47,492 fewer hours than the progress reports had, or approximately 64 percent of the hours in the progress reports.
The expert did not recognize, explain, or consider these obvious variances. An unexplained shortfall of 47,492 hours in the baseline schedule and schedule updates calls into question the reliability of the contractor’s planned durations and forecasted start and finish dates for the utilities and/or in-ground service works. These works would experience delay because the original durations in the baseline schedule and schedule updates were too short. Delay from original duration deficiencies would also cause delay to successor work activities.
4.4 BUDGETED LABOR HOURS FOR FOUNDATIONS AND STRUCTURES SHOW LARGER UNEXPLAINED DISCREPANCIES
The budgeted labor hours for the contractor’s foundations and structures were analyzed and summarized into building groups one through three. The contractor’s schedule delay expert opined that delayed predecessor sitewide civil works, utility works, and in-ground service works delayed the start of these buildings. Moreover, the expert concluded that the delayed predecessor work indirectly extended building durations due to confusion, disruption, loss of planned sequencing, and labor inefficiencies. However, budgeted labor hour variances were discovered between the contractor’s construction progress status reports and corresponding baseline schedule and schedule updates, as shown in Table 4-3 below.
Table 4-3: Comparison of Budgeted Labor Hours for Group Buildings
Group Buildings Description | Contractor Progress Status Report Work Type | Contractor Progress Status Report Budgeted Labor Hours | Assigned P6 Budgeted Labor Hours per Baseline Schedule and Updates | Budgeted Labor Hour Variance (Progress Report Hours Minus P6 Hours) |
---|---|---|---|---|
Group 1 Buildings | Buildings | 145,832 | 93,570 | 52,262 |
Group 2 Buildings | Buildings | 58,224 | 32,523 | 25,701 |
Group 3 Buildings | Buildings | 47,713 | 26,311 | 21,402 |
Subtotal – Foundations & Structures for All Buildings | 251,769 | 152,404 | 99,365 |
The budgeted labor hours in the baseline schedule and updates were consistently fewer by significant margins than those in the progress report. The progress report hours totaled 251,769 for all three building groups compared to 152,404 in the baseline schedule and schedule updates. The baseline schedule and updates contained 99,365, or 40 percent, fewer hours than the progress reports.
The schedule delay expert missed this obvious discrepancy when evaluating and calculating the delay claims. If the hours recorded in the progress reports were accurate, then the hours contained in the baseline schedule and schedule updates were too low. Therefore, in its building delay quantification, the expert neglected to identify and quantify contractor-responsible start delay caused by insufficient original durations for predecessor sitework and utility works discussed in Sections 4.2 and 4.3, and it failed to identify, consider, and quantify contractor-responsible delay within the building’s original durations due to inadequately assigned budgeted labor hours. Based on these deficiencies, any opinions and conclusions regarding building delay are flawed.
4.5 CONCLUSIONS REGARDING BUDGETED LABOR HOUR DIFFERENCES
Analyzing the budgeted labor hours revealed a clear disconnect between the hours in the progress reports and those in the baseline schedule and schedule updates. Table 4-4 below shows the substantial variance between these contemporaneous project records.
Table 4-4: Comparison of Budgeted Labor Hours for the Sitework Installation
Description | Contractor Progress Status Report Budgeted Labor Hours | Assigned P6 Budgeted Labor Hours per Baseline Schedule and Updates | Budgeted Labor Hour Variance (Progress Report Hours Minus P6 Hours) | Budgeted Labor Hour Variance % (Baseline Hours/Progress Status Report Hours) |
---|---|---|---|---|
Sitewide Civil Works | 56,968 | 29,402 | 27,566 | 52% |
Utilities/In-Ground Works All Buildings | 133,304 | 85,812 | 47,492 | 64% |
Foundations & Structures for All Buildings | 251,769 | 152,404 | 99,365 | 61% |
Work Package Total | 442,041 | 267,618 | 174,423 | 61% |
The progress reports included a total of 442,041 hours compared to 267,618 in the baseline schedule and schedule updates, meaning the baseline schedule and schedule updates contained only 61 percent of the progress report hours. The expert should have at least identified these glaring variances.
A variance of this magnitude is problematic. Which contemporaneous project record is correct? Are the hours in the progress reports more accurate than those assigned to schedule activities? How much delay was caused by the contractor having insufficient hours assigned to activities in the baseline schedule and schedule updates? The contractor’s schedule delay expert failed to recognize, explain, or consider these obvious variances.
Further, the expert also should have provided a complete and comprehensive investigation, validation, and reconciliation of why the contractor reported such differing hours between the two contemporaneous project records. The analysis should have included, and not been limited to, the contractor’s original labor hour estimate, the basis for that estimate, the original estimated productivity rates and assumptions, and schedule basis documentation.
An unexplained shortage of 174,423 hours in the baseline schedule and schedule updates calls into question the reliability of the contractor’s planned durations and forecasted start and finish dates for the sitework installation and subsequent utilities and building works. If the budgeted labor hours in the progress report were accurate, then the hours in the baseline schedule and schedule updates were understated.
Thus, the expert’s assignment of delay quantification and responsibility for delay was flawed. Without a comprehensive investigation of the contractor’s contemporaneous project records, any conclusions or opinions by the contractor’s expert regarding schedule delay, disruption, and responsibility for same stemming from the alleged changed site conditions issue were erroneous and unreliable.
5. THE CONTRACTOR’S CLAIMED PLANNED QUANTITIES FOR GROUND IMPROVEMENT DID NOT RECONCILE WITH THE CORRESPONDING PLANNED QUANTITIES IN ITS BASELINE SCHEDULE
The contractor claimed schedule delay to its ground improvement scope due to alleged differing site conditions on a complex refinery project. The differing site conditions allegedly caused delay and disruption to the ground improvement installation works for dynamic compaction, rock and sand fill, lime stabilization, and controlled modulus columns. The contractor claimed critical path schedule delay and recovery of extended project overhead costs against the owner.
The contractor’s schedule delay expert quantified schedule delay in large part by comparing the contractor’s planned quantities to actual quantities installed as well as comparing baseline schedule durations and forecasted dates to as-built schedule data. In its report, the expert used the planned quantities that the contractor submitted numerous times from previously issued change order packages and request for equitable adjustment reports. Table 5-1 summarizes the planned quantities that the contractor claimed by ground improvement work type.
Table 5-1: Claimed Planned Quantities for Ground Improvement Works
Ground Improvement Description | Unit of Measure | Total Planned Quantity Claimed by Contractor |
---|---|---|
Dynamic Compaction | Squared yards | 393,455 |
Rock and Sand Fill | Cubic yards | 2,457,821 |
Lime Stabilization | Cubic yards | 327,056 |
Controlled Modulus Columns | Each | 3,977 |
The contractor reported planned quantities for its ground improvement installations in other contemporaneous project records. It used P6 scheduling software to prepare and submit its approved baseline schedule to the owner, as the contract required. The contractor assigned planned quantities to individual work activities that represented the entire ground improvement scope in its approved baseline schedule. The P6 schedule coding in the approved baseline schedule allowed work activities to be organized, grouped, and summarized in the ground improvement work types for dynamic compaction, rock/sand fill, lime stabilization, and controlled modulus columns.
When comparing the planned quantities that the contractor claimed against the planned quantities assigned to work activities in the baseline schedule, it was obvious that the planned quantities in the baseline schedule were considerably lower. Table 5-2 below shows the comparison.
Table 5-2: Comparison of Planned Quantities for Ground Improvement Works
Ground Improvement Description | Unit of Measure | Total Planned Quantity Claimed by Contractor | Total Baseline Schedule Planned Quantity Assigned to Work Activities | Variance between Planned Quantity Claimed versus Baseline Schedule Planned Quantity | Planned Quantity Variance % (Baseline Quantity/Claimed Quantity) |
---|---|---|---|---|---|
Dynamic Compaction | Squared yards | 393,455 | 286,988 | 106,467 | 73% |
Rock and Sand Fill | Cubic yards | 2,457,821 | 1,595,213 | 862,608 | 65% |
Lime Stabilization | Cubic yards | 327,056 | 177,020 | 150,036 | 54% |
Controlled Modulus Columns | Each | 3,977 | 2,139 | 1,838 | 54% |
The planned quantities assigned to work activities within the contractor’s approved baseline schedule were consistently understated. The dynamic compaction scope planned quantities were 73 percent of those claimed by the contractor. The rock and sand fill planned quantities were 65 percent of those claimed, and the planned quantities for both lime stabilization and controlled modulus columns were approximately 54 percent of those claimed. Planned quantities assigned to work activities directly flow into the accurate calculation of planned durations for ground improvement installation works.
As a hypothetical example, a contractor planned 300,000 cubic yards of material for a cut and fill activity at a fixed rate of 3,125 cubic yards per workday in its baseline schedule. The planned duration is calculated at 96 workdays.15 If a contractor claimed that the correct planned quantities totaled 500,000 cubic yards, then the baseline schedule contained only 60 percent of the correct planned quantities claimed by the contractor, i.e., 300,000 baseline quantities divided by 500,000 correct quantities. At a fixed rate of 3,125 cubic yards per workday, the correct planned duration should have been 160 workdays. Therefore, the cut and fill activity’s original duration of 96 workdays is deficient by 64 workdays, i.e., 160 workdays minus 96 workdays, due to a shortage of assigned quantities in the baseline schedule.
For the ground improvement works identified in Table 5-2, if the contractor’s claimed quantities were correct, then the corresponding planned quantities in the baseline schedule were incorrect. Further, the baseline schedule was deficient in terms of original durations, forecasted dates, and calculated total float values because insufficient planned quantities were assigned to the ground improvement installation works. Neither the contractor nor its schedule delay expert recognized, explained, evaluated, or factored in this obvious discrepancy when it calculated its schedule delay days.
Therefore, it was highly likely that a sizeable portion of schedule delay claimed by the contractor and calculated by its schedule delay expert was caused by deficiencies in the baseline schedule due to understated quantities instead of differing site conditions. Without a verifiable explanation and reconciliation for these obvious planned quantity disparities, supported by contemporaneous project records, the accuracy and validity of the baseline schedule used as a starting point for measuring schedule delay was in serious doubt, and the expert’s calculated schedule delay was unreliable.
6. CONCLUSIONS AND LESSONS LEARNED
Based on the analysis of schedule delay claims discussed above, the following are key conclusions and lessons learned regarding the validity and veracity of contractor schedule delay claims.
1. The contractor selected an inappropriate and inadequate schedule delay analysis methodology in support of its delay claims.
The contractor’s schedule delay expert used a schedule delay methodology suitable to a simple project with a short-term duration, but the contractor’s scope was complex and spread over a large, diverse geographical area that included eleven service areas. The original planned duration to execute the entire scope was 2.5 years, and the contractor planned to work multiple service areas in parallel. The selected schedule delay methodology did not adequately consider month-to-month critical path shifts.
The methodology also required minimal changes between the baseline and as-built schedules. Comparing the contractor’s baseline and as-built schedule files showed they were significantly different in terms of number of work activities and logic relationships. In addition, the contractor’s expert did not identify, justify, or allocate responsibility for unexplained or concurrent delays found on the critical and near-critical paths as reported in monthly schedule updates. The omission of any analysis of obvious unexplained and concurrent contractor-caused delays on the contractor’s contemporaneous critical paths rendered the schedule delay analysis incomplete, inaccurate, and unsupportive of entitlement to a compensable delay.
The lesson learned is that delay analyses on large, complex, and geographically diverse project scopes with numerous stand-alone work areas should be performed with rigorous schedule delay analysis methodology. Selected methodologies should consider increased month-to-month schedule detail, unexplained concurrent delay, and changes to the critical and near-critical paths in the contractor’s monthly schedule updates. More appropriate schedule delay analysis methodologies utilize month-to-month schedule files and model impacts including concurrent delay on specific work activities for various windows of time.
2. The contractor claimed critical delay to the start of its tank installation works but failed to consider baseline schedule available float.
When considering the contractor’s planned late dates as derived from its planned early start dates and corresponding planned total float values in its approved baseline schedule, the owner provided actual area access for the propane tank and butane tanks before the contractor would have experienced any critical path delay. The table below summarizes the contractor’s claimed critical delay in calendar days, as quantified by its schedule delay expert, and the calculated delay based on the contractor’s planned late start dates of its propane and butane tank installation.
Table 6-1: Critical Delay Comparison to the Start of Propane Tank
and Butane Tank Installation
Description | Contractor-Claimed Critical Delay in CDs | Delay Based on Contractor’s Planned Late Start Dates in CDs |
---|---|---|
Delayed Propane Area Handover | 97 | (86) |
Delayed Butane Area Handover | 102 | (81) |
The owner provided access to the propane area 86 calendar days before the contractor’s late start date and 81 calendar days before the contractor’s late start date for the butane area. Hence, the contractor did not experience critical schedule delay. The contractor’s schedule delay expert failed to correctly include available total float for start of the area access milestone activities for the propane and butane tank installation.
The lesson learned is that delay analysts must correctly incorporate and consider float values and information in the baseline schedule and schedule updates before claiming critical schedule delay.
3. The contractor’s contemporaneous progress status reporting contained large, unexplained budgeted labor hour discrepancies with its approved baseline schedule and subsequent monthly schedule updates impacted by alleged critical schedule delay.
A disconnect existed between the contractor’s reported budgeted labor hours in its construction progress status reports and those in its baseline schedule and schedule updates, as shown in Table 6-2 below.
Table 6-2: Comparison of Budgeted Labor Hours for the Sitework Installation
Description | Contractor Progress Status Report Budgeted Labor Hours | Assigned P6 Budgeted Labor Hours per Baseline and Updates | Budgeted Labor Hour Variance (Progress Report Hours Minus P6 Hours) | Budgeted Labor Hour Variance % (Baseline Hours/Progress Report Hours) |
---|---|---|---|---|
Sitewide Civil Works | 56,968 | 29,402 | 27,566 | 52% |
Utilities/In-Ground Works All Buildings | 133,304 | 85,812 | 47,492 | 65% |
Foundations & Structures for All Buildings | 251,769 | 152,404 | 99,365 | 61% |
Work Package Total | 442,041 | 267,618 | 174,423 | 61% |
The baseline schedule and schedule updates contained only 61 percent of the budgeted labor hours in the progress reports, and the contractor’s schedule delay expert failed to identify, explain, or consider these obvious variances. Further, the expert’s calculation of schedule delay should have included a complete and comprehensive investigation, validation, and reconciliation of why there were such differences between the two contemporaneous project records. Assigned budgeted labor hours to work activities have a direct link to accurate activity durations, forecasted dates, and float values.
If the hours in the progress report were accurate, then the hours in the baseline schedule and schedule updates were understated. The baseline schedule was short by 174,423 hours, or 40 percent. Because the baseline schedule was used as a starting point for measuring schedule delay, the calculation of schedule delay was off by 40 percent.
Thus, the expert’s assignment of delay quantification and responsibility for delay would be incorrect. Unless the discrepancies were fully explained and reconciled, any of the expert’s conclusions or opinions regarding schedule delay, disruption, and responsibility for same that stemmed from the alleged changed site conditions were unreliable.
The lesson learned is that when the baseline schedule is used as a starting point for measuring schedule delay but contains significantly fewer budgeted labor hours than other key contemporaneous project records, the delay analyst must recognize, consider, investigate, reconcile, explain, and rectify the shortfall. Otherwise, the basis for quantifying schedule delay will be challenged and deemed inaccurate based on a faulty baseline schedule.
4. The contractor’s claimed ground improvement planned quantities did not reconcile with the corresponding planned quantities in its baseline schedule.
The contractor’s schedule delay expert quantified schedule delay caused by alleged differing site conditions by comparing the contractor’s planned quantities to actual quantities installed as well as comparing baseline schedule durations and forecasted dates to as‑built schedule data. The expert used planned quantities from the contractor’s change order packages and request for equitable adjustment documents. However, the expert did not identify, explain, or reconcile obvious differences between the planned quantities claimed by the contractor and the planned quantities reported in its baseline schedule, as shown in Table 6-3 below.
Table 6-3: Comparison of Planned Quantities for Ground Improvement Works
Ground Improvement Description | Unit of Measure | Total Planned Quantity Claimed by Contractor | Total Baseline Schedule Planned Quantity Assigned to Work Activities | Variance between Planned Quantity Claimed versus Baseline Schedule Planned Quantity | Planned Quantity Variance % (Baseline Quantity/Claimed Quantity) |
---|---|---|---|---|---|
Dynamic Compaction | Squared yards | 393,455 | 286,988 | 106,467 | 73% |
Rock and Sand Fill | Cubic yards | 2,457,821 | 1,595,213 | 862,608 | 65% |
Lime Stabilization | Cubic yards | 327,056 | 177,020 | 150,036 | 54% |
Controlled Modulus Columns | Each | 3,977 | 2,139 | 1,838 | 54% |
The baseline schedule consistently showed fewer planned quantities, but the expert did not recognize, explain, or justify why, nor did the expert consider or factor in the amount of delay caused by having insufficient planned quantities assigned to work activities in the baseline schedule. It was highly likely that a sizeable portion of schedule delay claimed by the contractor and calculated by its schedule delay expert was caused by the deficient number of planned quantities in the baseline schedule, which would directly affect calculation of activity durations, forecasted dates, and total float values in the baseline schedule.
The lesson learned is that the delay analyst should provide a verifiable explanation and reconciliation for any planned quantity deficiencies in the baseline schedule. Otherwise, the accuracy and validity of the baseline schedule used as a starting point for measuring schedule delay is questionable, and any calculated schedule delay will be unreliable. The delay analyst must validate the baseline schedule.
About the Author
Ronald J. Rider, M.B.A., is a Senior Principal with Long International and has over 30 years of experience in construction project management and contract dispute resolution. Mr. Rider has performed CPM schedule development, project cost control, cost and labor hour variance modeling, impact identification and causation, change order pricing and resolution, retrospective schedule delay, time extension and acceleration analyses, concurrent delay assessments, and damages quantification. Mr. Rider’s work experience includes petrochemical, oil refinery, power, commercial, industrial, road/highway, transit, hospital/medical, airport and casino projects. He holds a B.S. degree in Construction Management from Colorado State University and an M.B.A. degree from the University of Colorado. Mr. Rider is based in the Denver, Colorado area and can be contacted at rrider@long-intl.com and (303) 346-5836.
1 Erst and Young, “Spotlight on Oil and Gas Megaprojects,” 2014, p. 6 of 16.
2 A hardstand is generally known as a paved area designed to take the load of heavy machinery and vehicles parked for a long period.
3 AACE® International Recommended Practice 29R-03, “Forensic Schedule Analysis,” 2011, p. 43 of 134.
4 AACE® International RP 29R-03, p. 44 of 134.
5 AACE® International Recommended Practice 10S-90, “Cost Engineering Terminology,” Rev. 24 August 2012, p. 20 of 114.
6 See AACE® International RP 29R-03, MIP 3.7 and MIP 3.9.
7 The early start date is generally defined as the earliest possible start date for a work activity to begin.
8 The contractor’s baseline schedule planned early start dates correspond to the same contractual handover dates found in the contract documents.
9 Total float values are generally defined as the number of workdays a work activity can be delayed without delaying the project finish date.
10 The contractor’s baseline schedule printout included a footnote reference that stated it planned a 5-day work week (i.e., Monday through Friday) and excluded all holidays.
11 The late start date is generally defined as the latest possible start date for a work activity to begin without delaying the project finish date.
12 The 15,625 hours were calculated by dividing assigned 10,000 budgeted hours by 64 percent.
13 The 196 workdays were calculated by dividing 15,625 hours by the planned rate of 80 labor hours per workday.
14 The percentage was calculated by dividing assigned P6 budgeted hours by progress report budgeted hours.
15 The 96 workdays were calculated by dividing 300,000 cubic yards by the fixed rate of 3,125 cubic yards per workday.
Copyright © Long International, Inc.
ADDITIONAL RESOURCES
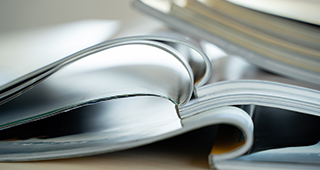
Articles
Articles by our engineering and construction claims experts cover topics ranging from acceleration to why claims occur.
MORE
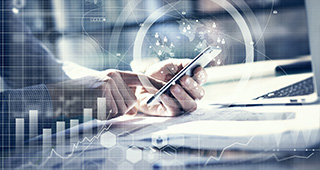
Blog
Discover industry insights on construction disputes and claims, project management, risk analysis, and more.
MORE
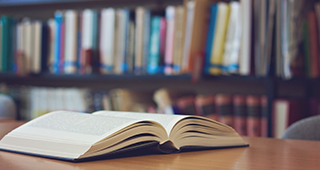
Publications
We are committed to sharing industry knowledge through publication of our books and presentations.
MORE