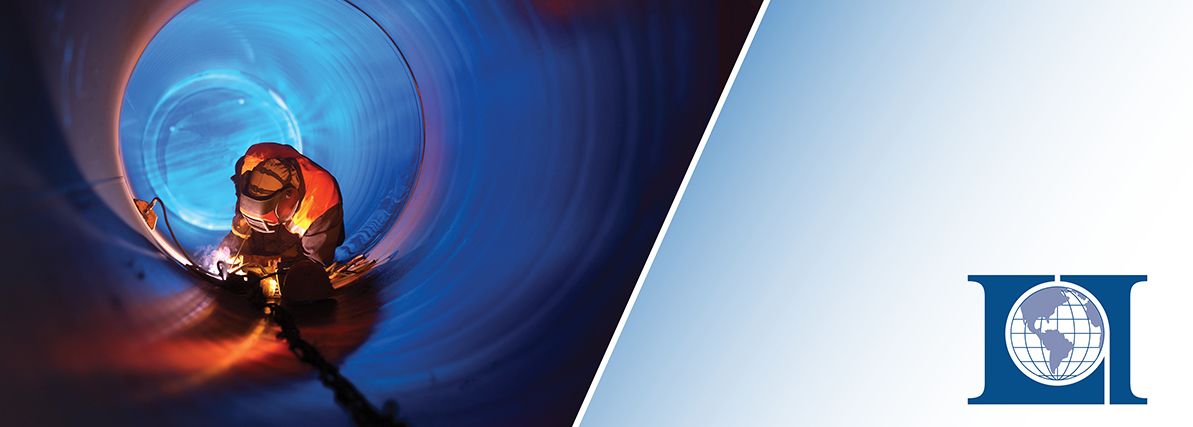
Modeling Productivity Loss Using System Dynamics to Understand and Quantify Cumulative Impact Damages
When changes are introduced during construction execution, individually and cumulatively, these changes can dramatically affect project performance and outcome. This article presents system dynamics modeling as a way to analyze the effects of scope changes on construction projects.
1. ABSTRACT
Identifying the cause-and-effect dynamics that result in productivity loss when scope changes and other disruptive impacts are introduced on construction projects has been a topic of discussion for many years. In recent years, the issue of productivity disruption resulting in the phenomenon known as cumulative impact continues to remain prevalent because of the difficulty for contractors to identify, quantify, and show causation for impacts and damages.1,2
A project is a system requiring fully functioning processes, procedures, tools, and resources. When any of these aspects do not work efficiently, especially from many unanticipated changes, a cascade of problems can occur. When changes are introduced during a construction project using the design-bid-build delivery (DBB), engineer, procure, construct (EPC),3 design-build (DB), turnkey, or other prominent contracting methodology, cumulatively, these changes can dramatically affect project performance.
With system dynamics modeling, it is theorized that a construction contractor’s ultimate productivity impacts can be calculated by simulating the primary causal influences and the resulting feedback loops.
Identifying and quantifying the cause-and-effect relationships of changes to mitigate or avoid their impact is vitally important to the construction industry.
2. INTRODUCTION
Identifying and evaluating the effects of changes and other disruptive events in construction has been a topic of discussion and debate for many years, especially those changes and other events that delay contractors and disrupt their productivity.
Managing projects involves a complex and integrated array of decisions, actions, and communications necessary for successful completion. A project is a system4 requiring fully functioning processes, procedures, tools, and resources. When any of these aspects of a system do not work efficiently and effectively, as the result of unanticipated changes and other disruptive events, a cascade of problems can occur. Richard Hooker noted in the 1500s that “Change is not made without inconvenience, even from worse to better.”5 This understanding regarding the effects of change remains the same in today’s world, especially in the construction industry. When changes are introduced during construction execution, individually and cumulatively, these changes can dramatically affect project performance and outcome.
In this article, the effects of scope changes can be analyzed using system dynamics modeling, primarily for projects delivered using a DBB methodology, but a DB methodology is also considered. Factors considered include how rework resulting from quality issues affects project outcome as well as other change types not resulting from quality problems.
While a project is underway, this topic is important because by identifying and quantifying the cause-and-effect relationships among factors that resulted from changes and other disruptive events, contractors can better prepare and plan for ways to mitigate or avoid their impact. With a better understanding of why productivity disruptions occur on construction projects, the construction industry can better forecast and manage the impacts of change.
Keywords: productivity, construction, change, system dynamics, rework, disruption, cumulative impact
3. PROBLEM STATEMENT
Considering the money at stake and the magnitude of complexity involved with construction, construction projects can be especially challenging when there are disputes concerning contractor performance. According to Baccarini:
Construction projects are invariably complex and since World War II have become progressively more so. In fact, the construction process may be considered the most complex undertaking in any industry. However, the construction industry has displayed great difficulty in coping with the increasing complexity of major construction projects.6
Because of the challenges the construction industry has had coping with complex projects, not all projects end well. Over the past several years, hundreds of millions of dollars have been lost in the United States due to disputes related to construction projects. Additionally, millions of dollars have been spent trying to prove or disprove a contractor’s entitlement to damages resulting from disputed changes to the work undertaken.7 The money and valuable time spent fighting for what a contractor or owner believes it is entitled to represent lost opportunities to pursue more productive and profitable endeavors.
Often, the issues surrounding a construction contract dispute are convoluted, integrating the hard quantitative effects and the softer “human” effects,8 making it difficult for a contractor to convincingly argue its case. Through the use of systems thinking and system dynamics (SD) modeling, the causes of construction disputes can be identified in ways that prove liability and allow for the equitable apportionment of damages to the contractor that has experienced productivity losses. Because an SD model can capture not only the quantitative effects of changes and other disruptive events, but also the softer human effects, as Howick9 notes, the result of the model outlined here is to facilitate analysis of the complexity associated with most construction contract disputes, especially those involving cumulative impact.
4. DISCUSSION
In this section, the following topics are discussed:
- What Is Systems Thinking?
- System Dynamics and the Rework Cycle
- Construction Changes
- Looking at DBB Projects Beyond the Rework Cycle
- Evaluating Changes on DBB Projects
4.1 What Is Systems Thinking?
Systems thinking has always been an integral part of the construction process, primarily in the form of systems engineering or systems architecture. These systems design processes can be evidenced by the modular design of the Great Wall of China, the use of bamboo scaffolding systems, and many concrete forming systems, for example. What is new is that the concept of systems thinking is now being applied to the management of construction projects, more specifically, the concept that construction projects are, in fact, complex, dynamic systems.
Before discussing systems thinking and system dynamics further, a system should be defined. There are many similar definitions, but one that applies well to project thinking, as well as most other aspects of our lives, is as follows:
A system is defined as a collection of parts that interact with one another to function as a whole. However, a system is not the sum of its parts – it is the product of their interactions.10
Peter M. Senge, one of the world’s leaders in systems thinking, describes systems thinking with this example:
A cloud masses, the sky darkens, leaves twist upward, and we know that it will rain. We also know the storm runoff will feed into groundwater miles away, and the sky will clear by tomorrow. All these events are distant by time and space, and yet they are all connected within the same pattern. Each has an influence on the rest, an influence that is usually hidden from view. You can only understand the system of a rainstorm by contemplating the whole, not any individual part of the pattern.11
Simply put, systems thinking looks at components that interact in some complex way and creates a result that could not exist by aggregating the results from each element working individually. We must look at our surroundings close-up and far away, in the past, present, and future, to understand how we fit into systems. Systems thinking evaluates our worldview in the context of our surroundings and the people with whom we directly interact and looks at the interactions and relationships within the system. Although this may sound like living in an Aldous Huxley novel, nearly all aspects of our lives are part of various systems.
… few realize how pervasive are systems, how embedded in systems we are in everything we do, and how influential are systems in creating most of the puzzling difficulties that confront us.12
To think in terms of systems, we must understand the systems we live in. These are a few examples of systems that we may not think of as such but very much are:
- Our families
- Social and professional circles
- Cities
- Businesses
- Religions and cultures
- Societies
- Governments
- The United Nations
- The airline industry
- A software package
The list can continue, but its intent is to stimulate thinking about how our lives are intertwined within systems. The effects of the interactions among relationships within a system may take seconds to play out, or they may take years. Sometimes it is difficult to see how we as individuals are part of any system. Senge states:
… [s]ince we are part of that lacework (of systems) ourselves, it’s doubly hard to see the whole pattern of change. Instead, we tend to focus on snapshots of isolated parts of the system, and wonder why our deepest problems never seem to get resolved.13
4.2 System Dynamics and the Rework Cycle
System dynamics is a modeling technique meant to capture and simulate the systems in our lives. Dr. Jay Forrester, known as the creator of system dynamics modeling, describes system dynamics as using:
… concepts drawn from the field of feedback control to organize available information into computer simulation models. A digital computer as a simulator, acting out the roles of the operating people in the real system, reveals the behavioral implications of the system that has been described in the model.14
One of the primary objectives of systems thinking and system dynamics modeling is to analyze complex problems and frame them in manageable ways.
One of the earliest applications of system dynamics modeling on a real project management problem helped determine how approved scope changes on a construction project cumulatively affected final project performance. The U.S. Navy awarded the project’s firm-fixed-price contract to Ingalls Shipbuilding in 1970. Ingalls’ scope was to design, procure, and construct a fleet of 30 destroyers. The project resulted in severe delays and significant cost overruns, leading to a dispute between the U.S. Navy and Ingalls Shipbuilding. Ingalls brought a claim to the U.S. of US$500 million.15 Ingalls felt that there was a ripple effect caused primarily by delays and disruption on the project due to thousands of owner-initiated design changes. The Navy’s position was that it paid the direct costs for each change, and that any resulting delay and disruption resulted from either Ingalls’ mismanagement of the project or deliberately underbidding to win the project.16
Ingalls spent many years trying to substantiate the ripple effect using traditional methods; however, it could not capture the combined effect of the quantitative and qualitative causes that led to the delay and disruption. Ultimately, Ingalls brought in a consultant to help it look at the problem from a different perspective because the traditional project management tools, which were exclusively quantitative-based, could not effectively explain the factors that led to the delay and disruption. After some investigation, the consultant determined that most of the delay and disruption came about as the result of rework: rework of design in many cases, rework of construction, and a combination of both. The consultant developed the following flow diagram (Figure 1)17 to illustrate how work, once initiated, would flow and how it would be diverted from being complete once a change was initiated:
Figure 1: Stock Flow Diagram for Rework (Cooper, 1980)
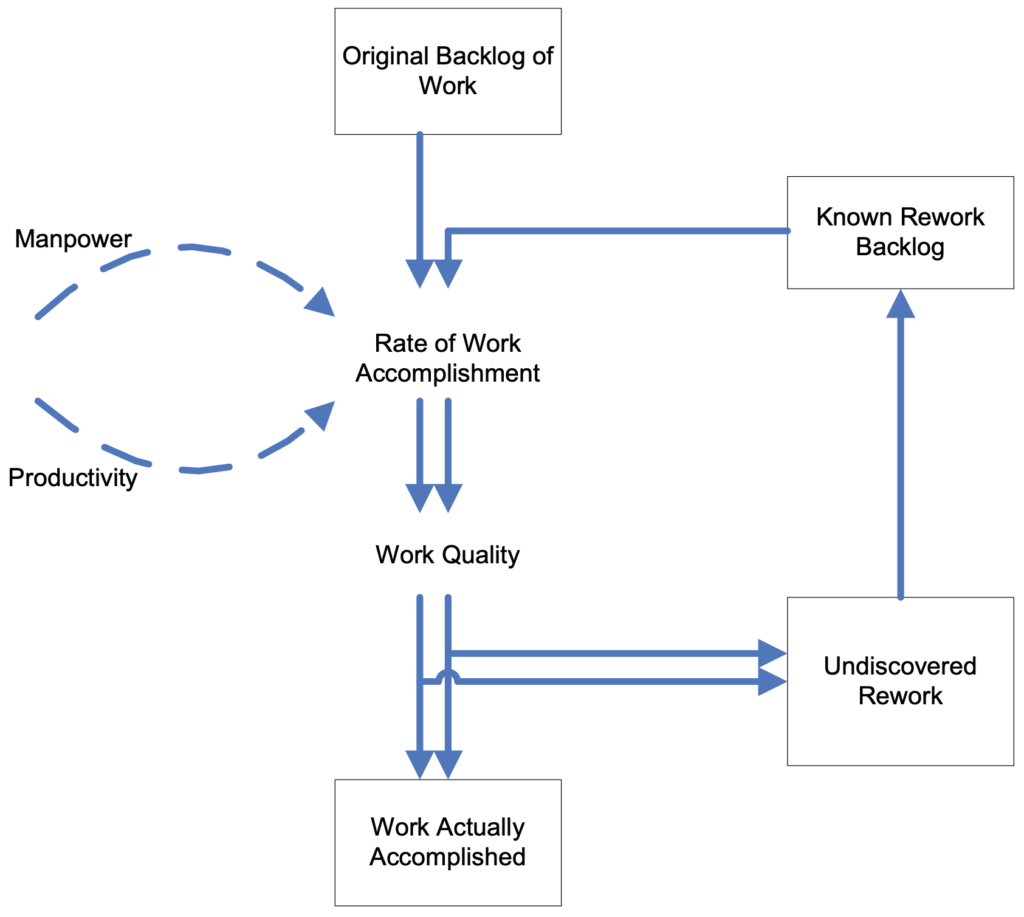
This model, originally developed by Ingalls’ consultant, evolved into what is called the “rework” cycle. There have been several iterations of the rework cycle; one of the more notable adaptations is found in Figure 2, created by Lyneis and Ford:18
Figure 2: The Rework Cycle (Lyneis and Ford, 2017)
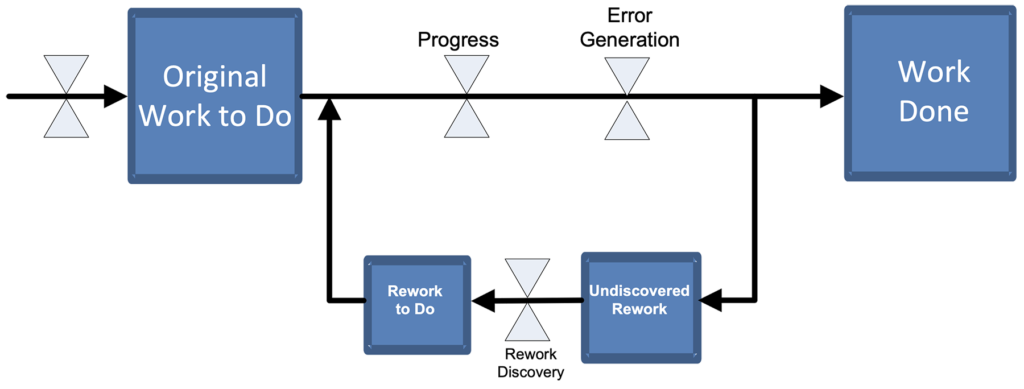
Its recursive nature is one of the rework cycle’s most significant and applicable attributes. Lyneis and Ford note:
The rework cycle’s recursive nature in which rework generates more rework that generates more rework, etc., creates problematic behaviors that often stretch out over most of a project’s duration and are the source of many project management challenges.19
In the figure above, the rectangles, called stocks, signify accumulations of work not being actively processed, and the directed pipes represent the flow of activity. The pipes can be viewed as conveyors of work activity. Activities feed and drain work accumulations, changing their magnitudes.20 In the context of the construction phase of a DB project, for example, the “Original Work to Do” stock represents an accumulation of construction work that has not been started but has been fully designed and is ready to be constructed. The “Work Done” stock represents construction work completed with no quality issues. As construction work starts, accumulated work found in the “Original Work to Do” stock increases, and as work is completed, work accumulates in the “Work Done” stock. The hourglass shapes, sometimes called levers, represent points of input where the flow of work activity can be adjusted. Levers are valuable to the modeler as input adjustments can be made to reflect the reality of a project to better understand the current environment, or what-if data can be inserted to see how certain decisions might play out. For example, the lever called “Error Generation” represents the point in the construction process at which errors are inserted. According to Lyneis and Ford,21 “[A] fraction of the work being done at any point in time contains errors.”
The rework cycle is valuable with projects delivered using the DB delivery method or any of their variations. On a DB project, design deficiencies are issues of concern for the construction contractor, especially since one of the techniques used with this type of delivery method is to “fast track” the work or start construction before the design is finished. Design deficiencies are a concern to the construction contractor because quality errors causing rework are its financial responsibility. Because rework is one of the biggest concerns on DB projects, the advantage of the rework cycle is that it helps management model the flow of work and rework, whether due to scope changes or quality issues.
However, the disadvantage of the above rework cycle is that it does not consider all types of changes that occur on construction projects, specifically those that do not cause rework but can equally create delay and disruption. This disadvantage is true with any project delivery methodology.
Models have been developed that consider changes other than those associated with quality issues and rework. For instance, Park and Pena-Mora22 developed a stock-flow diagram, Figure 3, that includes the rework cycle and addresses changes resulting from contractors’ Requests for Information (RFIs):
Figure 3: Generic Process Model Structure – Stock Flow Only (Park & Pena-Mora 2003)23
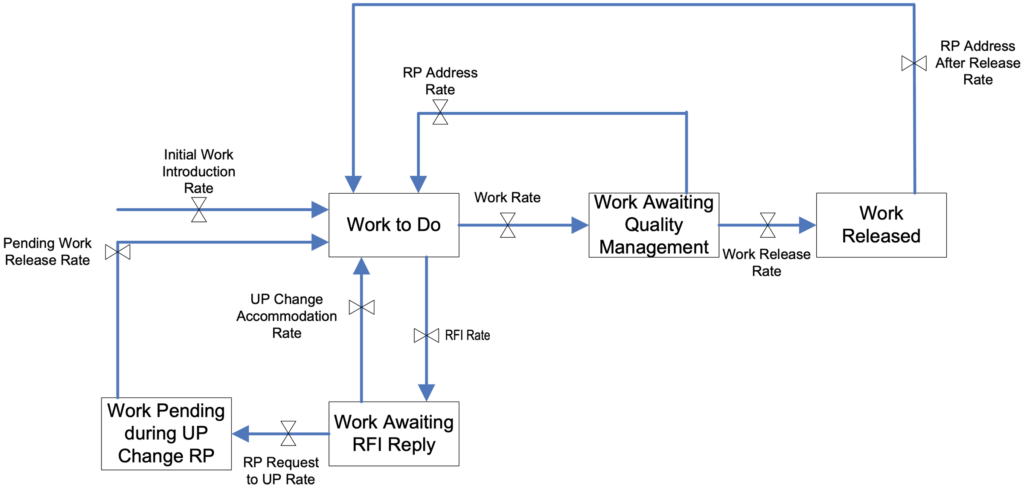
However, the Park and Pena-Mora model was developed in the context of projects with design-build delivery. This model has limitations when put into the context of a project delivered using the DBB method. The limitation of the Park and Pena-Mora model, like the rework cycle, is that it also does not allow for all types of change. The Park & Pena-Mora model, however, is an improvement over the rework cycle in that it not only allows for changes that result in rework, but also changes that result from contractor RFIs.
4.3 Construction Changes
Changes on projects often create tension between the parties of a contract, even creating mistrust and poor relationships between these parties. However, in industries where projects are the norm, it is now typically understood that change is endemic, brought on by an explosion in the development of technology and communications.24 According to AACE International, a change in scope is defined as “Alteration or variation to the project scope of work or service, cost, price, and/or the schedule for completing the work.”25 On construction projects, resources include manpower and equipment.
Changes, which can be singularly or collectively documented as change orders, occur for many reasons on construction projects. On the surface, each change to a construction contract is unique when compared to all other changes on the same project. However, most changes share common characteristics and can be classified into common categories. According to a study by the U.S. Inspector General,26 the causes for changes fall primarily into the following categories with their respective frequencies:
Design deficiencies | 42% |
Unforeseen conditions, including differing site conditions | 19% |
Changes in scope directed by the owner | 12% |
Undefined requirements | 5% |
Other categories | 22% |
Other studies researching the most frequent causes of changes on construction projects have had similar results.27,28 The U.S. Inspector General study and other studies clearly show that design deficiencies, also known as design errors and omissions, are the most frequent cause of changes during the construction phase of projects. There is no discrimination on whether the construction phase is delivered using the DBB or DB approaches. It makes sense that the DB contractor’s most significant concern would be design deficiencies because any resulting delays and/or disruptions must be managed internally and cannot be passed on to the customer.
4.4 Looking at DBB and DB Projects Beyond the Rework Cycle
Until recently, very little has been written concerning how changes impact DBB or DB contracts using systems thinking or system dynamics modeling. Over the past decades, many papers have been published addressing changes other than those that create rework during the construction phase.
This article proposes a system dynamics model that demonstrates how a culmination of all scope changes on a construction project that has experienced delay and disruption may result in a ripple or cumulative effect.
From the owner’s or contractor’s perspective, it is most valuable to model the cause-and-effect relationships of actions taken or not taken and decisions made, whether vicious cycles are predicted or beneficial cycles develop. Understanding this allows management to make more informed decisions that reduce risk and improve the chances that the project’s outcome is better than originally expected. The power of system dynamics can show all of this, along with the associated impacts.
For the analyst seeking to show the cause-effect linkage in a cumulative impact of changes claim, the task is even more difficult. By an earlier definition, cumulative impact is “exclusive of that local disruption that can be ascribed to a specific change,”29 or stated another way, cumulative impact cannot be caused by a single change. Additionally, court and board decisions have shown that simply demonstrating that numerous changes existed and that the contractor suffered a loss of productivity is not sufficient for recovery. This dichotomy is difficult to overcome.
In Luria Bros. & Co. v. United States, the court stated: “It is a rare case where loss of productivity can be proven by books and records; almost always it has to be proven by the opinion of expert witnesses.”30 Proving causation in direct disruption or cumulative disruption claims most often requires a qualified expert and detailed and complete contemporaneous project documentation.
For a project delivered using the DBB method, the only rework that the contractor has to be contractually worried about occurs during the construction phase by its own labor forces. Contrary to DB projects, the DBB contractor’s profit margin is not at stake for quality problems that occur during the previous design and procurement phases or as the result of owner-directed changes that affect construction work already in place. The owner is typically responsible for any changes not caused by the DBB contractor.
However, the contractor must be conscious of the impacts of all changes on a project, whether caused by the owner, another party, or self-inflicted. Just as was pointed out in the Navy v. Ingalls Shipping case, even though the owner and contractor may have executed change orders that rightfully address the direct impacts that a contractor incurred as the result of owner-caused changes, the accumulation of changes may not address the potential cumulative effect that is typically unknown until the project is complete. This is a concern regardless of the delivery method if the contractor is responsible for any delays for which the owner cannot be liable.
A valuable illustration of the cause-effect linkage of a claim is the cause-effect matrix. For any given owner-caused problem, one can graphically trace the effects to the contractor’s work. Figure 4 displays simple cause-effect matrices. The first matrix shows that a single problem, defective specifications, results in hydrostatic test failures. The second matrix has three initial causes, two intermediate effects, and two resulting problems.
Figure 4: Simple Cause-Effect Matrices
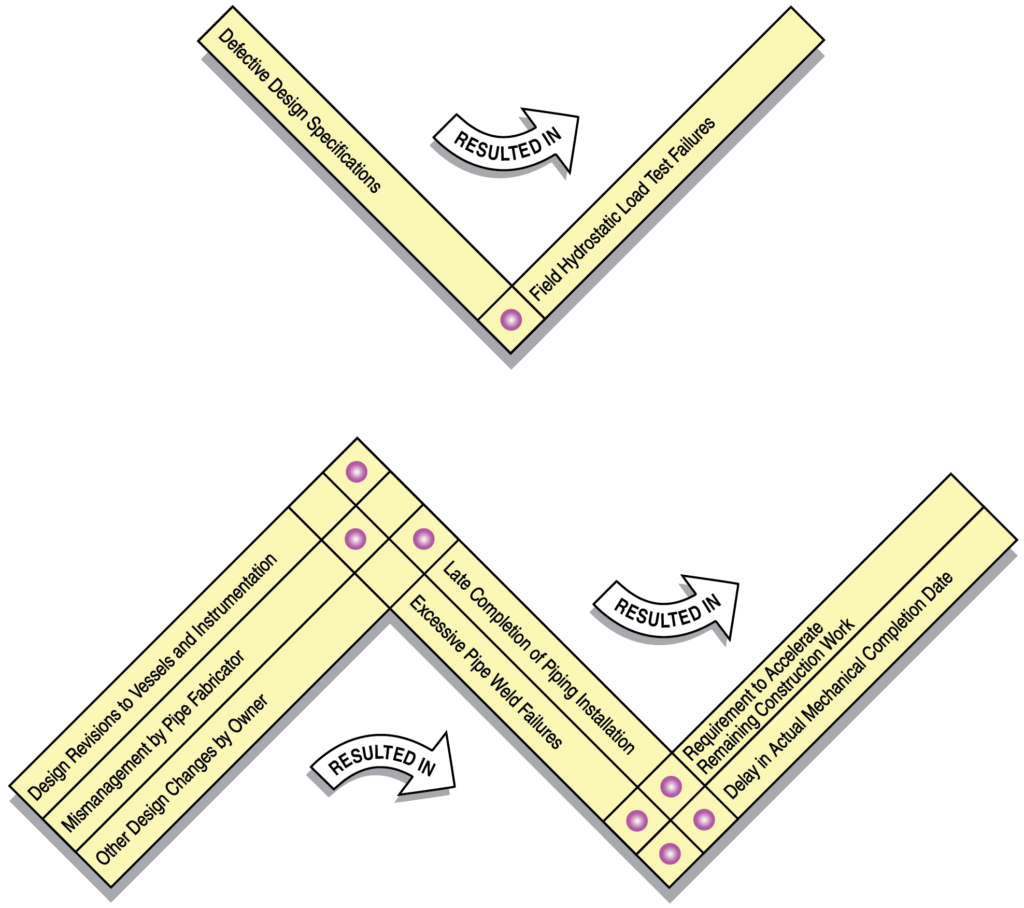
As multiple causes and their resultant effects are added, the matrix ultimately becomes much more complicated. Figure 5 shows a typical cause-effect matrix for a highly impacted project. Primary and secondary causes, including contractor-caused problems, are shown to have multiple and duplicative effects, the end result being a cost overrun. Even though it is complex, Figure 5 can still be broken down into the same type of simple relationships that are shown in Figure 4.
Figure 5: Typical Cause-Effect Matrix for a Delay/Disruption Construction Claim
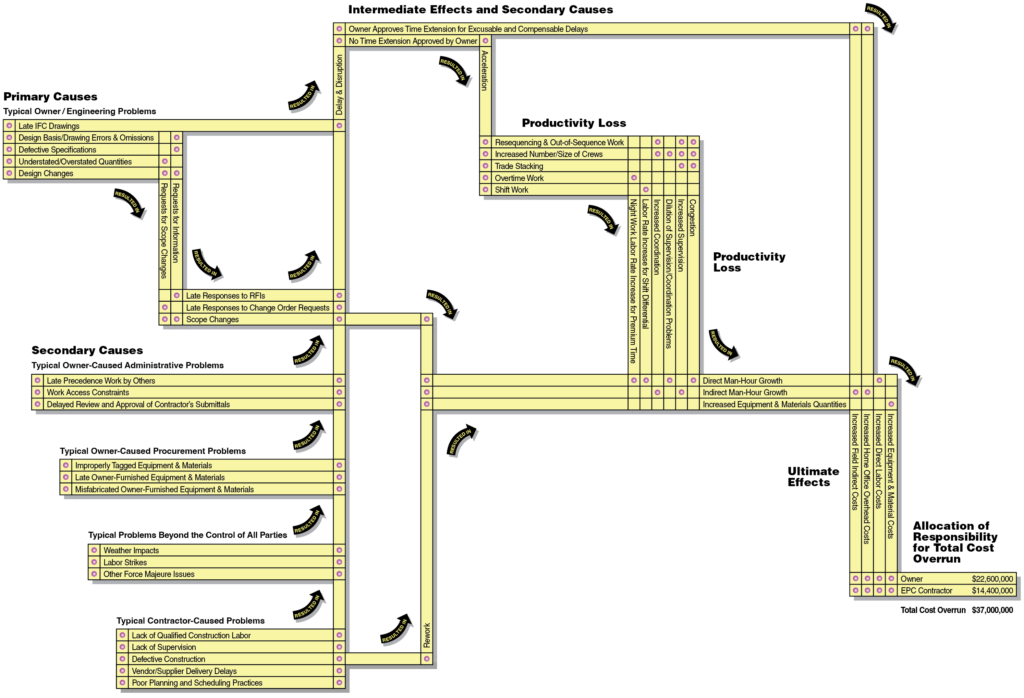
Tracing one path through this matrix tells a factual story: design changes resulted in the contractor requesting scope changes; the owner was late in responding to many change order requests, which resulted in delay and disruption; the owner did not approve the proper time extensions, which resulted in the contractor accelerating its work; and the acceleration caused trade stacking and congestion, which led to direct man-hour growth and increased direct labor costs, a portion of which are being claimed against the owner. Each of the causes has a similar factual story, the ultimate effect being increased costs.
Using a system dynamics approach to determine the effect of changes, a model was developed that addresses most types of changes on a construction project delivered using the DBB method as shown in Figure 6. It is adapted from the rework cycle that Cooper first developed and Lyneis and Ford later adapted, as well as other sources. However, it now integrates a new part to the process that addresses changes that are not exclusively quality or rework related.
Figure 6: Stock Flow Diagram – Design-Bid-Build Construction Delivery
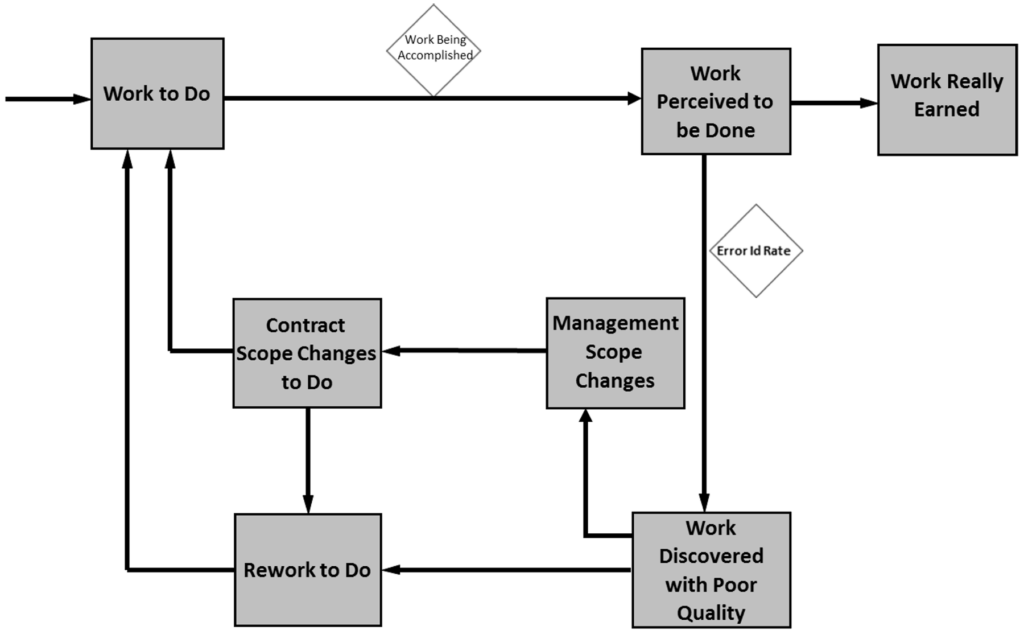
The value this model provides is that it allows management to take a more complete look at the impacts of all changes on a construction project delivered using the DBB delivery method, which would also apply to the DB and other delivery methods.
Taking the DBB stock-flow diagram a step further in the system dynamics modeling process, as shown in Figure 7, feedback loops are added to the stock-flow diagram to illustrate how potential external influences on the workflow process might impact how work is accomplished.
Figure 7: DBB Construction Change Stock Flow Diagram and Feedback Loops
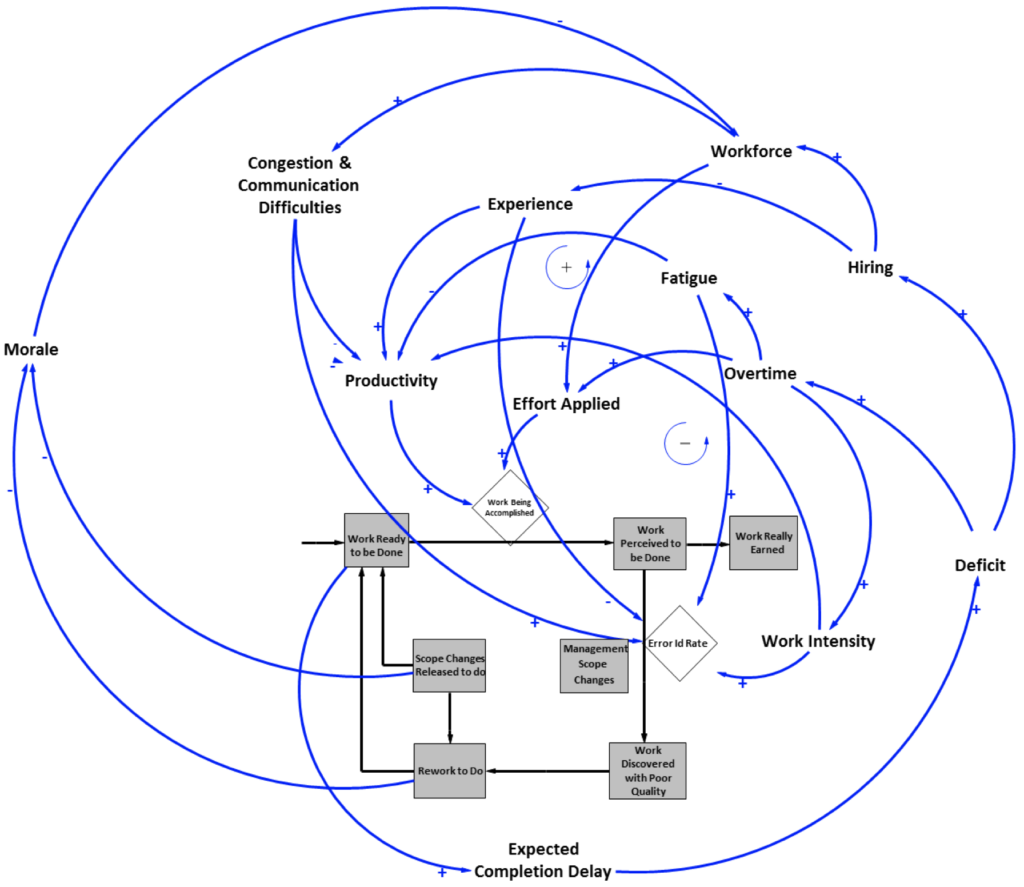
In system dynamics modeling, inputs and outputs from the influences that affect the operation of the model can be called “connectors.” Information connectors carry information needed to arrive at a decision.31 The labeled boxes between the connectors are causal influences that can affect the items they are connected to. These influences reflect what can and often does happen on projects where changes, even if directly captured within change orders, affect how a project is managed. For instance, on the right-hand side of the model, projects can experience a perceived labor resource deficit that causes or is forecasted to cause a delay. When this circumstance arises, there are typically three options that management can choose from to accelerate the project back onto schedule: 1) hire more workers, 2) have the existing workers work overtime, or 3) have the existing workers work with more intensity; that is, increasing their effort. Each of these influences would affect the project differently, with potentially positive and negative consequences.
This model has been shown to work and reflect what would be expected on a DBB construction project and was the concept of a Ph.D. dissertation.32 The model in this study (Figure 7) is not portrayed as the solution to cumulative impact situations. Still, it provides insight into the cause-and-effect dynamics of construction projects that have experienced the cumulative impact phenomenon.
5. CONCLUSION
Construction is one of the most unique industries in our global society because of the inherent project complexities and risks, often difficult to manage with minimal or no changes. With the insertion of scope changes on construction projects, the complexity and risks only increase. Depending on the project, this increased complexity and risk can be slow and somewhat predictable; or it can grow exponentially fast, leaving project management leadership feeling like it is on a night-time roller coaster ride, not knowing which direction the project will turn next.
Project management tools like CPM scheduling and Earned Value Management were developed to help project and construction managers forecast their projects’ ultimate schedule and cost outcomes. However, these tools alone cannot account for the cause-and-effect relationships and impacts of feedback looping from management decisions concerning, for example, the addition of more workers, more overtime, and more work intensity when a project is delayed, etc. The construction industry has long suffered from the inability to capture data and forecast project outcomes resulting from these softer but equally impactful influences.
Systems thinking and system dynamics modeling have been used to solve management problems across the last five decades, yet they are tools that are just starting to catch on in the construction industry. Because construction projects are becoming increasingly complex and have huge budgets never contemplated a decade ago, better dissection and understanding of project dynamics are vital for all stakeholders. Although no simulation models can precisely and accurately portray what will happen next on a project or why a particular input resulted in a seemingly unrelated output, simulation models like system dynamics are valuable because they help us understand the behaviors of project systems. They do this better than other project management tools and provide more insight into better decision-making. System dynamics modeling is an excellent tool to use during the planning process, during project execution, or forensically after a project is complete.
About the Authors
Stephen P. Warhoe, Ph.D., P.E., CCP, CFCC, is a Senior Principal with Long International and has a proven record as a testifying expert on delay, productivity loss, cost damages, and construction and project management. His background is rooted in years of practical experience planning, controlling, and managing major design and construction projects as large as well over US$4 billion in value. With over 35 years of experience in project controls, risk management, project management, construction management, and dispute resolution, he is a recognized expert in schedule delay analysis, productivity loss, project controls, and construction dispute avoidance and resolution. Dr. Warhoe is also a recognized construction expert on disputed projects valued well over US$6 billion and individual disputes well over US$3 billion. Dr. Warhoe also specializes in productivity loss analysis and quantification determination using system dynamics modeling, on which he wrote his Ph.D. dissertation. As recognition for his expertise and respect in the project controls field, he was elected president of AACE International from 2008 to 2009 and was made an Honorary Life member in 2019. He was the primary author on two of AACE’s Recommended Practices related to the change management process and the elements necessary for practitioners to demonstrate entitlement to a change order request or claim. He has also contributed to several other Recommended Practices published by AACE International and is currently the Vice President of AACE’s Technical Board. Dr. Warhoe is based in the Seattle, Washington, area and can be contacted at swarhoe@long‑intl.com and (206) 451-4320.
Richard J. Long, P.E., P.Eng., is Founder of Long International, Inc. Mr. Long has over 50 years of U.S. and international engineering, construction, and management consulting experience involving construction contract disputes analysis and resolution, arbitration and litigation support and expert testimony, project management, engineering and construction management, cost and schedule control, and process engineering. As an internationally recognized expert in the analysis and resolution of complex construction disputes for over 35 years, Mr. Long has served as the lead expert on over 300 projects having claims ranging in size from US$100,000 to over US$2 billion. He has presented and published numerous articles on the subjects of claims analysis, entitlement issues, CPM schedule and damages analyses, and claims prevention. Mr. Long earned a B.S. in Chemical Engineering from the University of Pittsburgh in 1970 and an M.S. in Chemical and Petroleum Refining Engineering from the Colorado School of Mines in 1974. Mr. Long is based in Littleton, Colorado and can be contacted at rlong@long-intl.com and (303) 972-2443.
1 Warhoe, S. and Long, R. (2023). “Demonstrating Entitlement to Cumulative Impact Claims in Construction,” AACE Recommended Practice 130R-23, April 2023.
2 See Long, R. et al (2014). “Cumulative Impact and Other Disruption Claims.” Virtualbookworm.com Publishing, Inc., College Station, TX.
3 EPC is a form of the design-build (DB) delivery methodology, and all references to DB in this article equally apply to project delivery using the EPC methodology.
4 Wideman, M. (2010). “Wideman’s Comparative Glossary of Project Management Terms, v. 3.1., “Project.” Retrieved August 6, 2012, from http://www.maxwideman.com/pmglossary/PMG_P09.htm#Project.
5 Pickavance, K. (2005). Delay and Disruption in Construction Contracts. London, LLP (Richard Hooker (born March 1554) quoted by Samuel Johnson in the preface to A Dictionary of the English Language (1755)).
6 Baccarini, D. (1996). “The Concept of Project Complexity – A Review.” International Journal of Project Management 14(4): 4.
7 Fullerton, R. (2005). “Searching for Balance in Conflict Management: The Contractor’s Perspective.” Dispute Resolution Journal, (February/April 2005): 1 to 8.
8 Howick, S. (2003). “Using system dynamics to analyse disruption and delay in complex projects for litigation: can the modelling purposes be met?”: Journal of the Operational Research Society 54: 222-229.
9 Id.
10 Maani, K. E. and R. Y. Cavana (2007). Systems Thinking, System Dynamics – Managing Change and Complexity, Pearson Education New Zealand.
11 Senge, Peter M. (2006). The Fifth Discipline, Doubleday.
12 Forrester, J. W. (1991). “System Dynamics and the Lessons of 35 Years.” The Systemic Basis of Policy Making in the 1990’s.
13 Senge, Peter M. (2006). The Fifth Discipline, Doubleday.
14 Forrester, J. W. (1991). “System Dynamics and the Lessons of 35 Years.” The Systemic Basis of Policy Making in the 1990’s.
15 Sterman, J. D. (2000). Business Dynamics – Systems Thinking and Modeling for a Complex World, Irwin McGraw-Hill.
16 Id.
17 Cooper, K. G. (1980). “Naval Ship Production: A Claim Settled and a Framework Built.” Interfaces 10(6): 20-36.
18 Lyneis, J. M. and D. N. Ford (2007). “System dynamics applied to project management: a survey, assessment, and directions for future research.” System Dynamics Review 23(2/3): 33.
19 Id.
20 Richmond, B. (2004). An Introduction to Systems Thinking: iThink Software, iSee Systems.
21 Lyneis, J. M. and D. N. Ford (2007). “System dynamics applied to project management: a survey, assessment, and directions for future research.” System Dynamics Review 23(2/3): 33.
22 Park, M. and F. Pena-Mora (2003). “Dynamic change management for construction: introducing the change cycle into model based project management.” System Dynamics Review 19(3): 213-242.
23 In the model, RP refers to reprocessing of work, and UP refers to upstream work.
24 Turner, J. R. (2009). The Handbook of Project-Based Management: Leading Strategic Change in Organizations, The McGraw-Hill Companies, Inc.
25 AACE International (2023). Cost Engineering Terminology, Recommended Practice 10S-90, Revised May 2023, AACE International.
26 U.S. Inspector General, Office of. (1982). Audit of Construction Contract Change Orders. U. S. Department of Transportation.
27 Diekmann, J. E. and M. C. Nelson (1985). “Construction Claims: Frequency and Severity.” Journal of Construction Engineering and Management 111 (No. 1, March): 8.
28 National Research Council – Building Research Board, Committee on Construction Change Orders (1986). Construction Contract Modifications – Comparing the Experiences of Federal Agencies with Other Owners. Washington D.C.
29 Centex Bateson Constr. Co., VABCA Nos. 4613, 5162, 5165, 99-1 BCA ¶ 30,153 (1998), aff’d, Centex Bateson Constr. Co. v. West, 250 F.3rd 761 (Fed Cir. 2000 at 149,258 (citing Triple “A” South, 94-3 BCA ¶ 27,194, ASBCA No. 46,866 (1994) at 135,523)).
30 Luria Bros. & Co. v. U.S., 177 Ct. Cl. 676, 369 F.2d 701, 713 (1966) at 713.
31 Richmond, B. (2004). An Introduction to Systems Thinking: iThink Software, iSee Systems.
32 See Warhoe, Stephen P., (2012). Applying Earned Value Management to Design-Bid-Build Projects to Assess Productivity Disruption: A System Dynamic Approach, Dissertations.com Publishing, Boca Raton, FL, U.S.A.
Copyright © Long International, Inc.
ADDITIONAL RESOURCES
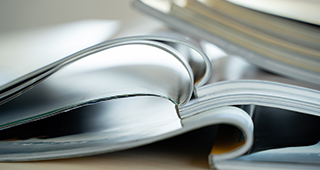
Articles
Articles by our engineering and construction claims experts cover topics ranging from acceleration to why claims occur.
MORE
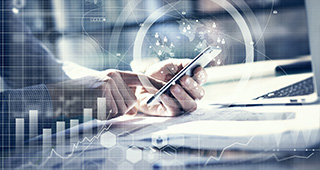
Blog
Discover industry insights on construction disputes and claims, project management, risk analysis, and more.
MORE
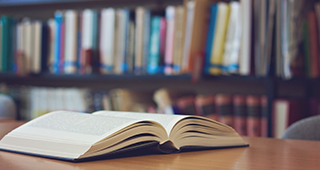
Publications
We are committed to sharing industry knowledge through publication of our books and presentations.
MORE