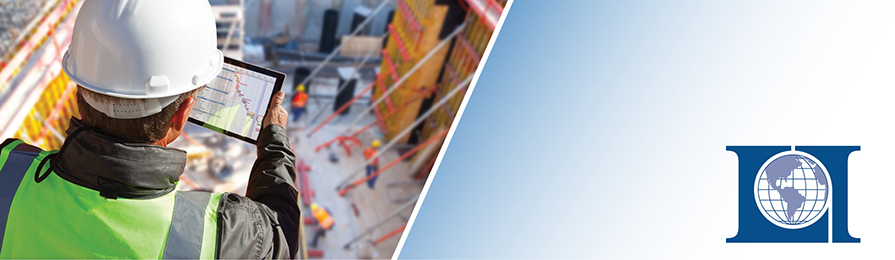
Schedule Mechanics – The Foundation of a Quality Schedule
This article discusses certain scheduling aspects, schedule metrics that are used to measure mechanical soundness, and a methodology for schedule quality assurance.
1. INTRODUCTION
Project Managers require schedules that accurately reflect the planned work and actual progress of a project. To realistically and logically model the planned execution of a project, the schedule must not only reflect the scope of work and execution plan but also be mechanically sound.
Schedule soundness pertains to multiple scheduling aspects, including schedule bases, activity descriptions, activity durations, activity types, relationships between activities, resources, and constraints. This article briefly discusses each of these scheduling aspects. Schedule metrics that are used to measure mechanical soundness and a methodology for schedule quality assurance are also discussed.
2. PMBOK DEFINITION OF A SCHEDULE
The Project Management Institute’s PMBOK defines the Project Schedule as, “An output of a schedule model that presents linked activities with planned dates, durations, milestones, and resources.”1 PMBOK defines a schedule model as, “A representation of the plan for executing the project’s activities including durations, dependencies, and other planning information, used to produce a project schedule along with other scheduling artifacts.”2 Due to the capabilities available in modern scheduling tools, the planning information is expanded to include constraints and other activity information. Most project schedules utilize the Critical Path Method (CPM), which PMBOK defines as, “A method used to estimate the minimum project duration and determine the amount of scheduling flexibility on the logical network paths within the schedule model.”3
3. SCHEDULE BASIS DOCUMENTS
While the project contract, schedule basis document, project scope of work, and project execution plan are not mechanical elements of the project schedule, they create the framework on which the mechanics are based and also may be used to document variances from and exceptions to best scheduling mechanics practices.
The project contract will often specify the contractual requirements for planning and scheduling and milestone completion dates that must be achieved during the project. This is an appropriate place to look for the mechanical criteria that may be measured as part of schedule quality assurance, schedule detail requirements, and other criteria expected from the project schedule network.
The project scope of work defines the work to be accomplished and may also define some constraints for which the project must make allowances. The entire scope of work includes the project design basis, project specifications, and design drawings. Full descriptions of the scope of work should be included in the project schedule basis. The scope of work is a primary source for identifying and defining schedule activities.
The project execution plan is a written description of how the project scope of work will be accomplished. The execution plan will likely include specific procedures that must be followed while accomplishing the work. The execution plan may also specify constraints which may impact the work. Like the scope of work, the execution plan is also a key source for identifying schedule activities.
The schedule basis memorandum is where the scheduler typically documents how the scope of work and execution plan have been used to develop the schedule network. The assumptions made, constraints identified, and exceptions and clarifications to contractual requirements should all be identified and documented in the schedule basis document.
4. ACTIVITY DESCRIPTIONS
Activity descriptions should be unique, specific, understandable in isolation, and detailed enough to support the schedule logic. During the execution of a project, many different schedule data views or barchart layouts are often developed to demonstrate a particular scenario or unique subset of work, and being able to understand the activity descriptions in isolation assures that these scenarios can be interpreted correctly. Specificity of activity task descriptions is important so that those using the schedule can easily understand what work scope is to be accomplished for progress to be accurately measured and so that relationships can be easily understood. It is also important that there are enough activities to make logic relationships clear and not require excessive use of relationship lags, which will be discussed later.
5. ACTIVITY DURATIONS
There are several different methods to determine activity durations. These include resource demand in relation to availability, windows of time during which a short duration task may be accomplished, field planning of duration based on experience, and others. With all methods, it is key that original durations be defined in such a way that remaining durations can be determined when statusing the schedule during execution.
5.1 RESOURCE DEMAND
Using resource demand for determining duration is the most desirable method for determining schedule duration. This method is especially effective when the activity is continuous once started. With this method, the original duration or remaining duration of an activity are easily calculated using total remaining work quantities divided by the production rate for the resource. For example, 500 cubic yards ÷ 50 cubic yards per day = 10 days. Productivity factors can be applied to production rates to increase the accuracy of calculated durations. Accordingly, this method results in the most defensible schedule durations and leaves little room for hidden contingency within activity durations.
5.2 WINDOWS OF TIME
Windows of time for task completion are often used when the exact timing of a task is not known, but is expected between two points in the schedule. Windows of time for short duration tasks can be very risky when the activity lies on or near a critical path. This can cause artificial critical paths to form and hide more critical items in other areas.
5.3 FIELD PLANNING
Field planning is probably the most common method for activity duration development. Using input from field personnel who will perform the work to estimate activity durations aids in schedule buy‑in and should result in reasonable duration estimates for activities. A risk with field duration estimates is the potential for field personnel to overstate estimated activity durations to ease their on‑time accomplishment of schedule tasks. This can create artificial critical paths that may hide truly critical activities.
6. ACTIVITY TYPES
There are several types of activities potentially used in project schedules, including:
- Task – An activity with a duration representing a scope of work to be accomplished.
- Milestones – An activity with zero duration representing the beginning or end of a task, series of tasks, phase, or other activity grouping.
- Hammock – An activity summarizing a group of other activities. The duration is usually defined as the period of time from the earliest start of the group to the latest finish of the group.
- Level of effort – A non‑driving activity whose duration is determined by the period of time from the earliest time where the activity is needed to the latest time it is needed. This type of activity is often used to represent support efforts in the schedule.
7. ACTIVITY RESOURCE LOADING
Activities in a schedule should be resource loaded to ensure alignment between project budgets and the schedule activity durations. Resource loading can include labor hours, equipment hours, material quantities, and other cost items. By loading resources into the activities, checks can be performed to ensure that all budgeted work items have corresponding schedule activities to monitor the progress of the work scope.
7.1 LABOR RESOURCES
Labor resources, in the form of man‑hours, should be loaded into the schedule so that labor demand curves can be generated from the schedule. These labor demand curves can then be used to determine the manpower hiring needs to accomplish the work and to identify areas where there may be resource constraints. By adding unit rates, the labor resources will also provide labor budgets for the schedule.
7.2 EQUIPMENT RESOURCES
Equipment resources are often loaded into the schedule to manage critical equipment usage. For example, heavy lift equipment may need to be carefully scheduled to support all lifting needs. This can be accomplished by loading the equipment as a resource and setting appropriate limits on availability. Equipment resources can also be rate loaded to provide schedule budgets.
7.3 MATERIAL QUANTITIES
Material quantities can be loaded into the schedule to provide a basis for activity budgets and also to create a basis for calculating physical schedule progress. This is often done outside of the schedule in tools specially designed for this purpose.
8. ACTIVITY LOGIC
The sequence of the work activities in a schedule network is determined by activity logic ties.
8.1 USE OF ONLY ONE START AND ONE FINISH ACTIVITY
All schedule networks should have only one start and one finish activity. The start activity defines the time from which the project schedule network is measured and the finish activity should represent the total project completion or the time at which all activities are complete. Between these two start and finish activities are the project activities which define the project scope of work.
8.2 RELATIONSHIP TYPES AND USE
The Precedence Diagramming Method (PDM) utilizes four predecessor and successor logic relationship types to define mandatory and discretionary or preferential logic relationships between schedule activities.
Every activity in the schedule should have at least one predecessor related to the start of the activity and one successor related to the finish of the activity. The only exceptions to this are the project start and project finish activities.
Without a start predecessor, there is nothing telling the activity to start other than the project start date or current data date. By default, no activity starts prior to the project start, so that is the default start predecessor should no others exist.
Without a finish successor, there is nothing in the schedule that tells the activity when it needs to be finished. Increases in duration of an activity without a finish successor will not drive out the project finish activity. By default, an activity without a finish successor should be tied to the project finish.
8.2.1 Finish‑to‑Start Relationships
Finish‑to‑start relationships are the most common type of schedule activity and the simplest when defining schedule logic. For a finish‑to‑start activity, the predecessor has to be completed before the successor can begin. This type of relationship is easily measured.
8.2.2 Start‑to‑Start Relationships
Start‑to‑start relationships indicate that the successor can begin once the predecessor has begun. Often times, this type of relationship will include a lag duration to allow for some of the predecessor work to commence and progress before the successor work commences. Start‑to‑start relationships should be minimized, when possible, by including an appropriate level of detail in the schedule. This can be accomplished by defining a task to represent the amount of predecessor work needed to be completed prior to the successor task and linking them with a finish‑to‑start relationship.
8.2.3 Finish‑to‑Finish Relationships
Finish‑to‑finish relationships indicate that the successor can finish once the predecessor has finished. Often times, this type of relationship will include a lag to allow for some of the successor work to continue on for a while after the predecessor work finishes. Finish‑to‑finish relationships also should be minimized, when possible, by including the appropriate level of detail in the schedule. This can be accomplished by defining a task to represent the amount of successor work needed to be finished after the predecessor task and linking them with a finish‑to‑start relationship.
8.2.4 Start‑to‑Finish Relationships
The start‑to‑finish tie is the rarest relationship used. One example of a start‑to‑finish tie is when the start of the new shift for a security guard permits the finish of the current security guard’s shift. If the next shift security guard doesn’t show up, the first shift security guard must continue his duty. This type of relationship is not commonly used and should typically be minimized or avoided completely.
8.3 RELATIONSHIP LAGS
A relationship lags is a duration assigned to a logic relationship to represent a period of time from when the relationship begins and ends. Lags are often used in summary schedules to represent pieces of work not appropriate for the level of detail of the schedule. They may also be used to simplify schedule logic.
Lags should be minimized wherever possible by adding schedule detail to support proper relationships without lags. The primary reason for this is that, in commonly available scheduling software, there is no mechanism to progress a relationship lag when updating a schedule. Once the lag duration becomes invalid, it must be changed to update the schedule, which compromises the integrity of the original plan.
9. CONSTRAINTS
Constraints are imposed start or finish dates assigned to an activity, which may override the scheduling calculations and cause the schedule network dates to be calculated differently than the activity durations and relationships alone would allow. There are many different constraints available in modern scheduling tools which have different effects on the activity relationships and float values. Constraints should only be used when absolutely necessary and that necessity should be clearly identified in the schedule basis document.
9.1 LOGIC LIMITING CONSTRAINTS
Logic limiting constraints put limitations on schedule logic without totally overriding the logic. Some typical logic limiting constraints include:
- Start no earlier than – forces the activity to start after a set date
- Finish no earlier than – forces the activity to finish after a set date
- Zero free float – forces an activity to start as late as possible without effecting the end date of the successor
9.2 LOGIC OVERRIDING CONSTRAINTS
Logic overriding constraints override schedule logic. Some typical logic constraining constraints include:
- Must start – forces the activity start on the indicated date
- Start on – forces the activity start on the indicated date
- Must finish – forces the activity finish on the indicated date
- Finish on – forces the activity finish on the indicated date
10. SCHEDULE QUALITY ASSURANCE PROCEDURES
The process for performing quality assurance reviews on project schedules includes evaluating schedule metrics to measure the schedule mechanics being used and comparing them against industry norms. Typical schedule metrics may include:
- Activity type summary – count of activities by type
- Activities per $1 million of cost – used to evaluate level of schedule detail
- Activities per month cycle time – used to measure detail consistency through the project life
- Average activity remaining duration – used to evaluate level of schedule detail
- Excessive activity duration
- Number of constrained activities
- Average activity float
- Float ratio – float/duration
- Open ends
- Excessive lag check
- Excessive float check
By evaluating these metrics during schedule development, areas for improvement can be identified and the schedule can start out on a solid foundation.
11. CONCLUSION
A mechanically sound schedule network creates a solid foundation for schedule monitoring, updating, evaluation, and revision. By having proper schedule metrics, critical paths are easily identified and project management is provided with accurate and reliable information to address schedule performance issues as they arise.
About the Author
Robin K. Long, PMP, was an Executive Consultant with Long International. Mr.Long has over 24 years of U.S. and international project management experience involving planning and scheduling, cost management, risk identification and management, estimating, project controls, contract strategy and administration, and construction supervision. His project experience includes refineries, petrochemical and chemical plants, offshore oil and gas facilities, oil sands and oil shale facilities, midstream oil and gas facilities, and LNG facilities. Before joining Long International, Mr.Long held multiple project controls and management positions for some of the world’s leading energy and EPC companies, including Anadarko Petroleum, ConocoPhillips, Enron, Atkins (Faithful & Gould), Raytheon Engineers and Constructors, and Fluor Corporation. These roles ranged from functional management positions, responsible for entire regions or disciplines, to individual contributor roles in planning and scheduling and cost management. Mr. Long is very proficient with a wide variety of software tools including Oracle Primavera Project Planner P6, Primavera P3 3.1, Primavera Risk Analysis, Microsoft Project, Microsoft Office Suite, Microsoft Access, SAP, and Acumen Fuse. For further information, please contact Long International’s corporate office at (303) 972-2443.
1 A Guide to the Project Management Body of Knowledge (PMBOK® Guide), Fifth Edition, 2013, Glossary.
2 Ibid.
3 Ibid.
Copyright © 2016 Long International, Inc.
ADDITIONAL RESOURCES
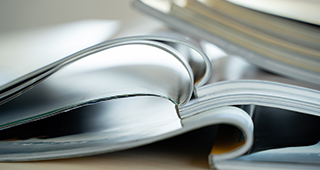
Articles
Articles by our engineering and construction claims experts cover topics ranging from acceleration to why claims occur.
MORE
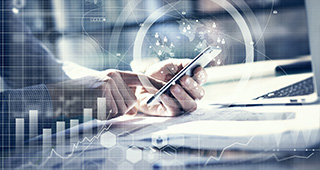
Blog
Discover industry insights on construction disputes and claims, project management, risk analysis, and more.
MORE
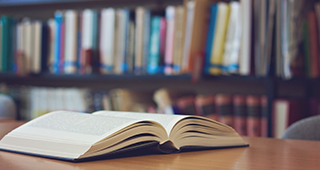
Publications
We are committed to sharing industry knowledge through publication of our books and presentations.
MORE