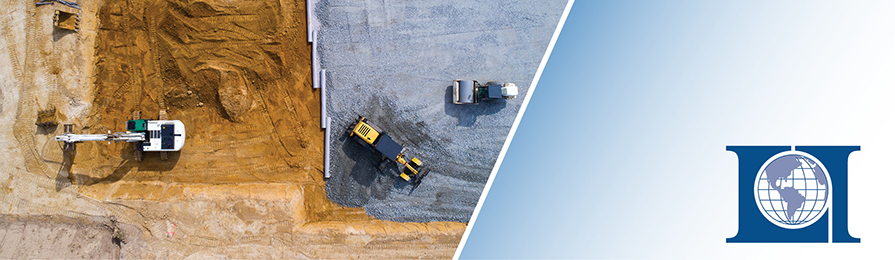
Key Elements for Successful Schedule Management
The purpose of this article is to help put into perspective the key considerations that should be given to the scheduling program on projects to achieve the optimal balance between scheduling effort and scheduling quality.
1. INTRODUCTION
The project schedule is fundamental to the success of any construction project and represents the approved plan for the execution and completion of the contracted work scope. An accurate schedule serves many important functions and benefits on a project. The project schedule:
- Communicates to the parties the proposed strategies required to complete the project, including the detailed listing of the tasks, steps, sequences, and the durations of the work to be performed during the project’s lifecycle;
- Coordinates the direction and timing of work, i.e., getting everyone on the same page;
- Provides a checklist of the project tasks to be performed, which helps to reduce the occurrence of oversights and omissions;
- Identifies the critical and near-critical paths, and the float that are projected for completing the project;
- Identifies the responsibilities that the parties share in completing the project;
- Identifies the restraints on the project that are known at the time;
- Provides a timeline of the important and contractual milestone dates that are identified for the project;
- Provides a means to assess the resource requirements and allocations for the project. This helps to identify the critical resource needs and bottlenecks that the project may experience;
- Provides a baseline from which performance and progress for the project can be measured;
- Serves as a tool in helping to identify issues and impacts that may be associated with the potential changes to the contractual work scope for the project;
- Provides a means to simulate the potential impacts that may result from different options for a proposed change;
- Identifies and establishes the schedule risks for the project so that they may be effectively managed;
- Provides a historical accounting and record of the work that was actually performed on the project, compared to that which was initially planned.
A challenging aspect of project scheduling is to strike the optimal balance between expending too much time and resources in trying to develop and maintain the “perfect” schedule versus expending too little time and few resources on the schedule development resulting in a poor quality schedule that underrepresents or misrepresents the contractual work scope and is inaccurate and dysfunctional. The intent of this article is to help put into perspective the key schedule optimization considerations that should be given to the program on projects to achieve the optimal balance between scheduling effort and scheduling quality.
2. SCHEDULE LIMITATIONS AND OBJECTIVES
The objectives for schedules typically vary between projects. The scheduling objectives are dependent upon a number of influences and factors, including the following:
- Project management’s direction and preferences;
- Contractually defined schedule planning and reporting requirements;
- Accountability and allocation of responsibility;
- Imposed constraints relative to the budget and resources that are dedicated to project planning and controls;
- Level of active input and support by the parties that are directly involved with the project;
- Available project detail and scope definition;
- Scheduling staff experience.
Ultimately, it is important that the schedule is reasonable, executable, and sufficiently detailed and accurate to provide management with a tool that reflects the actual status of the project, and not just support a general statement that the project is simply “on track.”
Schedules which are deficient in detail and accuracy serve little value on a project. The work is continually performed out of sequence and cannot be tracked. Therefore, the performance of the work against the baseline plan is unmeasurable. It is also difficult, if not impossible, to accurately assess potential changes to the work scope and impacts to the schedule. Because the schedule is imprecise, the status of the work progress to date is not measurable. As a result, the work that remains to be completed cannot be reasonably assessed or forecasted.
On the other end of the spectrum, the accuracies of the schedules that are determined to be exhaustively detailed are also questionable. The scheduling effort surpasses the point of practicality; the resources become fully expended and overwhelmed; and, the project becomes all-consumed with managing the schedule, instead of using the schedule to manage the project. If the magnitude of the schedule is too large and detailed, an exorbitant amount of energy is required to maintain and update the schedule. The accuracy of these schedules is often compromised and the information is out of date because of the project’s inability to support the scale of the effort. Finding the happy medium relative to the effort expended on schedule development is a challenge on any project.
3. KEY ELEMENTS THAT CONTRIBUTE TO SUCCESSFUL SCHEDULE MANAGEMENT
A successful schedule requires a number of components and considerations. These scheduling elements should be regarded as best practices and include the following:
3.1 CONTRACTUAL REQUIREMENTS
The scheduling and reporting requirements vary between projects. It is prudent that the contractor develops a scheduling program that complies with the contractual requirements and that the owner reviews and critiques the contractor’s schedule submittals to ensure that the schedules and updates provided are in accordance with the provisions established in the Contract. By conforming to the contractual requirements, the schedule will provide a documented accounting of the contractor’s baseline plan and an accurate record of the actual progress. The schedule is intended to serve as a document whose basis is used in protecting the interests of the parties should a delay or acceleration issue or dispute come into question.
3.2 WORK BREAKDOWN STRUCTURE (WBS)
Creating the schedule starts with a breakdown of the planned tasks that are identified for the project into definable and manageable categories. The WBS provides a common framework to use as a basis for organizing, planning, and controlling the work for the total scope of a project. It also serves as a basis for linking the schedule activities with the resources. With the breakdown of the work into WBS classifications, complex schedules become more manageable. Certain considerations should be given to the level of detail of the WBS so that the coding is supportive of the project and the schedule and remains controllable. Considerations for defining the level of detail of the WBS include:
- The duration of the schedule activities in the lowest level of detail of the WBS should not be longer than the contractual reporting period. For example, if the established reporting period for the project is once a month, then the duration for any single activity should be less than one month long;
- It should be possible to estimate the cost and duration of each WBS element;
- Every WBS element should have a definable beginning and end date;
- Activities can be assigned to specific individuals and parties by responsibility;
- The level of detail for the activities is reasonable and it would be impractical to breakdown the work any further;
- The execution performance of the activities can be measured;
- The work packages defined by the WBS are each unique and do not overlap one another:
- Each WBS level must be easily rolled up to the next higher level.
3.3 PROJECT SCOPE
The schedule is only as good as the level of detail of the information that is available at the time. If the project’s design is conceptual, preliminary, or incomplete, then the schedule on which this information is based is similarly incomplete. As the design detail progresses and becomes more developed and definitive, it is important to periodically update the schedule with this information.
Encompassing the full work scope that is defined for the project, the schedule should reflect the activities and work sequences that are based on the collective input from all parties, including project management, engineering, field supervision, the contractor, and subcontractors, etc. It is important that the input from others is solicited and included in the schedule because this effort helps to avoid future schedule conflicts as well as encourages the parties’ collective ownership and acceptance of the schedule.
3.4 SCHEDULE LOGIC
The logic for a schedule includes the activity durations, the interrelationships between the activities, and the relationship lag and lead durations. Typically, the logic for a schedule is based on a company’s, team’s, or individual’s experience on similar types of projects. It is essential to recognize that although two projects maybe similar, there are variables that make them different and may cause the performances between projects to differ. For example, different owners may have different requirements and demands. A change in the location between two projects may also present different challenges and constraints.
The project’s cost estimate may also serve as a basis for developing the durations of the work activities. Depending upon the level of detail of the estimate, the man hours, and perhaps the crew compositions for the work activities may be determined. Estimating the durations may be as simple as taking the total man hours that are estimated for an activity and dividing this number by the total number of laborers that comprise the crew to calculate crew hours. Taking this quantity of crew hours and dividing by the number of work hours per day yields the total number of work days estimated for the activity. This activity duration can then be adjusted to account for crew inefficiencies, standby time, contingencies, etc. If the cost estimate identifies the man hours, but does not address the composition of the crew, the number of people that comprise a given crew can be estimated, based on experience.
Assessing the logic requirements between the activities in a schedule involves determining the sequence and establishing the types of relationships between activities. The objective in developing the logic is to accurately estimate the types of activity connections that are required to complete the work efficiently. The interrelationships between the tasks are primarily based on the planner’s previous experience, in addition to taking into account any requirements or factors that are specific to the project, and which drive the sequence and completion of the work. If the logic in the schedule is incorrect, the activities will be started out-of-sequence and may possibly be delayed.
3.5 CRITICAL PATH
Once the activities have been identified and the logic ties have been addressed, the schedule’s critical path is ready for review. The critical path is defined as the chain of activities in the schedule with the lowest Total Float that comprises the longest continuous sequence of activities through the schedule from project start to completion. A schedule may contain more than one critical path. It is important to note that as a project progresses, the schedule’s critical path can change. In an accurate schedule, the critical path activities should realistically represent the scope of work for the project which cannot be delayed without extending the project completion date. If the critical path includes minor inconsequential activities, whose inclusion on the critical path is questionable, then any constraints and logic controlling the critical path activities should be reevaluated to ensure the validity and reasonableness of the critical path.
3.6 RESOURCE LOADING AND LEVELING
The resources in schedules usually include craft labor, construction equipment, permanent materials, and process equipment. The resource loaded schedule offers a count of the total quantity of resources that are required for all activities. Often, the labor man hours and the major material quantity requirements are evaluated and tracked in the schedule. Once the resources are loaded, an assessment is completed to determine whether the man hours and permanent material quantities can be supported by the project. Peaks and valleys relative to resource demand may exist initially and require leveling. There are several ways that the resources for an activity in a schedule may be leveled. These include:
- Distributing the resources in the activity differently. For example, non-linear front-end loading, instead of linear level loading;
- Possibly starting the activity earlier or later;
- Revising the logic tie of the activity’s successor from finish-to-start (FS) to a start-to-start (SS), or a finish-to-finish (FF) logic tie, if the successor can be started before the work for the activity is 100 percent complete;
- Completing material fabrication and staging work during periods of the project that are determined to have low resource requirements;
- As a final resort, consider extending the duration of the activity.
3.7 SCHEDULE ACCURACY
It is essential for the scope of work for the project to be fully represented by the listing of the activities in the schedule and in the WBS. An inaccurate schedule offers no benefit to a project. At a minimum, the time and costs that a party may have saved in preparing an incomplete schedule will be required to be expended in making corrections and possibly developing a re‑baseline of the schedule. In the meantime, the project suffers in having to rely on a tool that does not represent the project.
An incomplete or inaccurate schedule poses a number of problems to a project. First, the actual work progress remotely follows, or does not follow the plan defined in the schedule. The work progress is continually completed out of sequence from that planned. The schedule’s critical path frequently changes. Consequently, it is difficult to assess the health of the project and whether the contractual milestone and completion dates will be achieved. Problems and issues are not readily apparent and cannot be forecasted or acted upon in timely manner. It is difficult to predict and manage resource and equipment requirements and usage because the erroneous schedule has forced the project into a reactive mode. Lastly, it is hard to conduct a delay impact analysis or simulate the impacts of different alternatives for a proposed change without an accurate schedule.
3.8 DEVELOPING AND MAINTAINING THE CHANGE CONTROL PROCESS
Performance on a project cannot be effectively measured and credited unless an approved baseline schedule is developed. In addition, the impact of potential and approved changes to the contract scope of work cannot be evaluated without an approved baseline schedule and an established change process. The baseline schedule on a project serves as a contractual document that is approved and accepted by all parties involved in the project. Any revisions, modifications, adjustments, or changes should be regulated and approved by the project’s owner. The process for completing the updates and changes in the schedule, and the schedule reporting requirements and cycles, should be clearly addressed in the Contract for the project.
For projects in which the change control process is ill-defined or ignored, the schedule becomes a meaningless document that serves little benefit or purpose, other than possibly meeting the minimum submittal requirements for the project. Without the change regulation, the accurate record of the work scope initially planned versus the work scope for the project that was actually completed is deficient. The schedule, then, cannot be readily used as a basis of record in resolving issues or disputes on the project.
4. CONCLUSION
In conclusion, the success of schedule management on a project is dependent on accurate information and a dedicated planning process. A number of other important elements, however, are also required to support a productive scheduling program. Many projects, although well planned, fail as a result of insufficient attention given to the scheduling effort. Relative to planning and scheduling, sufficient consideration should be given to:
- Adequately defining the schedule activities, sequences, and relational logic between the activities;
- Sufficient identification of the work packages in the WBS;
- Accurate estimation of the activity durations;
- Sufficient schedule detail to adequately support the scope of the project;
- Established change order control and schedule progress updating procedures;
- Timely schedule updating and reporting;
- Open distribution and communication of accurate schedule information to all parties.
The effort and resources that are committed to supporting the scheduling program on a project must be adequate, yet reasonable, to meet the requirements of the project. A scheduling program that is overly complex and onerous to maintain is as likely to fail as a scheduling program that is too simple and lacking in commitment and support. Successful scheduling programs have sufficient and experienced resources, dedicated support, and a manageable structure.
5. REFERENCES
Wikipedia, “Work breakdown structure,” May 8, 2016, https://en.wikipedia.org/wiki/Work_breakdown_structure.
David Brown, “Top 10 Steps to Schedule Management,” EC&M, March 1, 2008, https://www.ecmweb.com/maintenance-repair-operations/article/20889409/top-10-steps-to-schedule-management.
Ron Holohan, “6 Steps to Successful Schedules,” ProjectSmart, https://www.projectsmart.co.uk/scheduling/6-steps-to-successful-schedules.php.
Kiron D. Bondale, “The Benefits of an Accurate Project Schedule,” PMHut, April 24, 2010, https://pmhut.com/the-benefits-of-an-accurate-project-schedule.
Sam Palani, “5 Steps to Project Scheduling,” Stepping Into Project Management, October 11, 2011, http://www.steppingintopm.com/2011/10/5-steps-to-project-scheduling.html.
AACE International, AACE CCC/CCE Certification Review Course, 2011.
About the Authors
James M. Bolin was a Senior Executive Consultant for Long International and retired in 2020. He has over 35 years of experience in all aspects of project and construction management, pre-construction planning, and project cost/schedule controls. His qualifications include claims and change order analysis and resolution, preparation of fixed-cost proposals and budget baseline planning, site management and coordination, prime and subcontract development and administration, materials expediting and procurement, and critical path method (CPM) delay analysis, schedule development, progressing and reporting. This diverse expertise has been obtained through involvement on numerous project types, including: oil production facilities, pipelines, pump stations, water and wastewater treatment plants, mineral processing facilities, water storage, hydroelectric plants, hospital/medical, transit, airports, communications, and environmental remediation. The value of these projects has ranged from US$50,000 to over US$10 billion. For further information, please contact Long International’s corporate office at (303) 972-2443.
Andrew Avalon, P.E., PSP, is Chairman and CEO of Long International, Inc. and has over 35 years of engineering, construction management, project management, and claims consulting experience. He is an expert in the preparation and evaluation of construction claims, insurance claims, schedule delay analysis, entitlement analysis, arbitration/litigation support and dispute resolution. He has prepared more than thirty CPM schedule delay analyses, written expert witness reports, and testified in deposition, mediation, and arbitration. In addition, Mr. Avalon has published numerous articles on the subjects of CPM schedule delay analysis and entitlement issues affecting construction claims and is a contributor to AACE® International’s Recommended Practice No. 29R-03 for Forensic Schedule Analysis. Mr. Avalon has U.S. and international experience in petrochemical, oil refining, commercial, educational, medical, correctional facility, transportation, dam, wharf, wastewater treatment, and coal and nuclear power projects. Mr. Avalon earned both a B.S., Mechanical Engineering, and a B.A., English, from Stanford University. Mr. Avalon is based in Orlando, Florida and can be contacted at aavalon@long-intl.com and (407) 445-0825.
Copyright © Long International, Inc.
ADDITIONAL RESOURCES
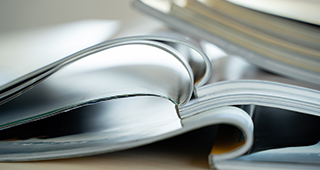
Articles
Articles by our engineering and construction claims experts cover topics ranging from acceleration to why claims occur.
MORE
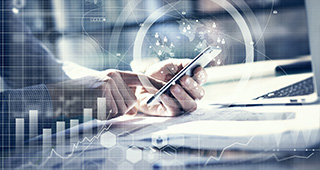
Blog
Discover industry insights on construction disputes and claims, project management, risk analysis, and more.
MORE
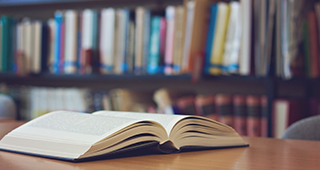
Publications
We are committed to sharing industry knowledge through publication of our books and presentations.
MORE