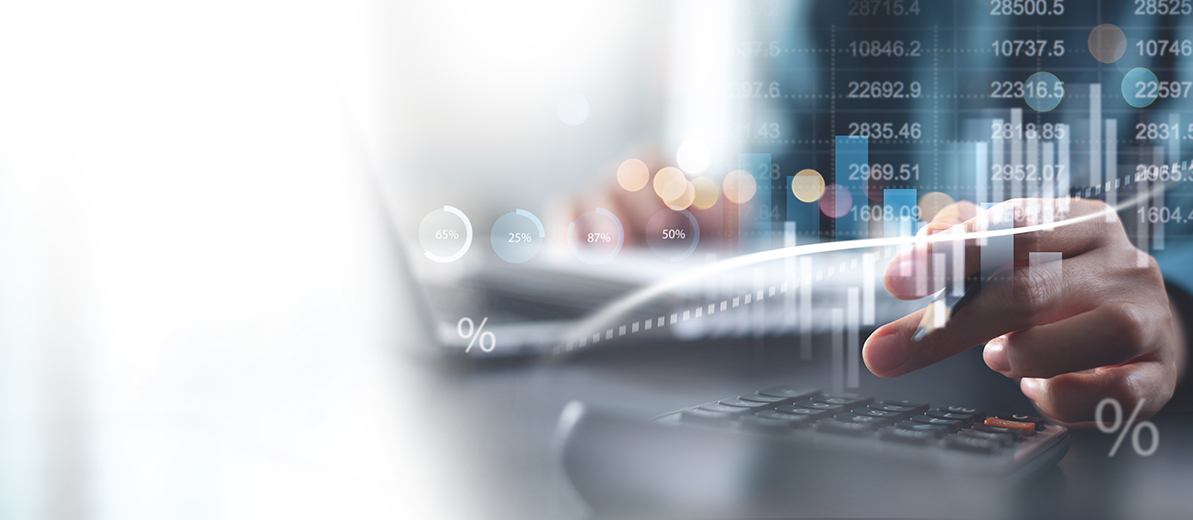
July 21, 2025
Costs, Damages, and Cost Estimating Terminology
This is the first blog post in a six-part series that defines terms commonly used in Engineering, Procurement, and Construction (EPC) project management, construction management, and claims. This post defines language related to costs, damages, and cost estimating. Future posts will cover labor and productivity, scheduling and delay, claim and contract types, and project and construction management.
A/B Estimates of Damages – The A/B Estimate method is generally utilized in cases where the changed work or the cause of the delay or disruption related to the changed work is straightforward. For example, a lump sum contractor bids on a chemical plant expansion assuming that a large pressure vessel is to be located at grade with its own foundation. After the job begins, the contractor discovers that the engineer has relocated the vessel in the structure above grade because of other process changes made by the owner. The contractor in such a case can prove its damages by subtracting an independent estimate of the work as planned (the “A Estimate”) from the new estimate of the work with the vessel relocated (the “B Estimate”). The “B Estimate” is a fair and reasonable estimate of the value of the work, at the time of the bid, if the contract documents had contained an adequate description of the problems and changes that occurred during the course of the work. The contractor’s damages under this method would be the difference between the two estimates.
Activity-Based Costing (ABC) – Activity-Based Costing identifies activities in an organization and assigns the cost of each activity resource to all products and services according to the actual consumption by each: it assigns more indirect costs (overhead) into direct costs. In this way, an organization can establish the true cost of its individual products and services to identify and eliminate those that are unprofitable and lower the prices of those that are overpriced. The methodology assigns an organization’s resource costs through activities to the products and services provided to its customers. It is generally used as a tool for understanding product and customer cost and profitability. As such, ABC has predominantly been used to support strategic decisions such as pricing, outsourcing, and identification and measurement of process improvement initiatives.
Actual Cost – Cost sustained in fact, based on costs incurred, as opposed to a standard, predetermined, forecasted, or estimated Cost. Actual Costs to date include costs of Direct Labor, Direct Material, and other direct charges, specifically identified to appropriate Cost Accounts as incurred, and overhead costs and general administrative expenses reasonably allocated to cost accounts.
Actual Cost of Work Performed (ACWP) – The cost incurred and recorded in the accounting system for performing the work within a specific time period.
Bid Error – An error made by the contractor in preparing its bid proposal/cost for performing contract work. Bid errors may include, but are not limited to, incorrect labor rates, labor productivity factors, overhead rates, schedule duration assumptions, estimated quantities, and technical assumptions for which the contractor is responsible.
Budget – The estimated costs, obligations, and expenditures for performing the project; also called the performance measurement baseline budget.
Budgeted Cost of Work Performed (BCWP) – The earned dollar value of work accomplished during the measurement period. The method used to calculate earned value can be either objective or subjective.
Budgeted Cost of Work Scheduled (BCWS) – The sum of budgets for the work scheduled to be accomplished within a given time period.
Code of Accounts – A logical, hierarchical breakdown of a project into controllable elements for purposes of cost control and reporting.
Contingency – The amount budgeted to cover costs that may result from incomplete design, unforeseen and unpredictable conditions, or uncertainties. The amount of the contingency depends on the status of design, procurement, and construction and the complexity and uncertainty of the component parts of the project.
Control Budget – The control budget is a restatement of the original bid estimate in a form that facilitates comparisons between budget and actual costs. The control budget is normally prepared after bid opening and before construction starts. The control budget is not the contractor’s bid. The bid proposal is the price sheet used in the contract as the basis of payment for work performed. The contractor prepares an estimate of costs, overheads, and anticipated profit (the total of which becomes the bottom line of its bid), but the makeup of individual cost elements becomes hidden when assigning values (prices) to each bid item. Bid unbalancing is common. In addition, payment is usually based on units of work completed and not for interim steps along the way. An example of the latter is payment for concrete—paid for by the cubic yard, in place. No separate payment is usually made for forming, pouring, finishing, etc. For this reason, the control budget (which shows separate estimated costs of forming, finishing, and placement of concrete), and not the bid schedule, is to be used as the basis for comparison for calculations of damages using the discrete damages/cost variance analysis approach.
Thus, the control budget is a restatement of the original bid estimate and commercial proposal in a form that facilitates detailed cost account comparisons and reporting between budget and actual costs, quantities, man-hours, and unit productivity rates. The control budget is normally prepared after the owner accepts the contractor’s commercial tender, and before project-specific engineering and construction begin on a turnkey engineering, procurement, and construction (EPC) project. The control budget delineates the contractor’s total estimated costs (by cost elements such as labor and material), quantities, and man-hours into cost accounts comprising the project scope of work defined by the project work breakdown structure.
Control/Cost Account – Often used interchangeably, the terms “cost account” and “control account” refer to the management control point at which actual costs are accumulated and performance is determined. It represents the defined work assigned to one responsible organizational element according to the work breakdown structure and must contain the specific Scope of Work, definite schedule, assigned budget, unique identification, and method of measuring performance. The control account concept is applicable to all projects. Large projects may have a series of control accounts that may be divided into work packages and planning packages. Small projects may have only one control account consisting of a single charge number.
Cost Baseline – A budget that has been developed from the base cost estimate for the scope baseline and has been time-phased in accordance with the project schedule. The cost baseline is referred to as a baseline since it is integrated with the scope and schedule baselines and subject to formal change control. Normally it also contains direct and indirect budget, management reserve budget, undistributed budget and higher-level budgets, and a contingency amount.
Cost Benefit Analysis (CBA) – Process of quantifying costs and benefits of a decision, program, or project (over a certain period), and those of its alternatives (within the same period), in order to have a single scale of comparison for unbiased evaluation. Unlike the Present Value (PV) method of investment appraisal, CBA estimates the Net Present Value (NPV) of the decision by discounting the investment and returns.
Cost Contingency – The amount appropriated to cover costs that may result from incomplete design, unforeseen and unpredictable conditions, or uncertainties. The amount of the contingency will depend on the status of design, procurement, and construction and the complexity and uncertainty (risk) of the component parts of the project. Cost contingency is not a substitute for making an accurate assessment of expected cost.
Cost Estimate – A result or product of an estimating procedure that specifies the expected dollar cost required to perform a defined Scope of Work, activity, or project. A cost estimate may constitute a single value or a range of values.
Cost Estimate Types – Cost estimates are grouped into four general categories:
- Planning Estimates, often referred to as Rough Order of Magnitude or Ball Park Estimates, are intended to grossly approximate the value of a given task or program. Planning cost estimates are of a low confidence level, since they are based on loosely defined project parameters, drawings, plans, definition, and data with respect to scoping the overall schedules, statement of work, equipment lists, and delivery requirements. Because of this, a significant risk allowance/contingency is usually added to planning estimates for undefined work and other unknowns. Planning estimates are generally required early in the program definition cycle for the purpose of go-no-go decisions. The amount of estimating detail is minimal, and normally only a top dollar value is provided. Planning estimates are submitted for information purposes only and do not represent a formal commitment.
- Budget Estimates are normally required for funding, fiscal planning, or procurement decisions. Budget estimates are often derived through the use of preliminary functional organization estimates and gross parameters and are based upon substantially well-defined data and ground rules but require additional definition before a firm price can be quoted. An allowance for undefined work and unknowns is generally added to budget estimates. Budget estimates denote pricing accuracies that are superior to Planning Estimates but still do not represent a firm commitment.
- Firm Cost Estimates are based on well-defined plans and data and are usually in response to a customer firm request for a proposal that has a near-term go-ahead. Firm estimates require the submission of the greatest amount of substantiating detail, and the preparation of an extensive backup package, to support contractual negotiations.
- Not To Exceed (NTE), or Not Less Than (NLT), Estimates are commitments from a contractor as to the maximum amount (or minimum credit) required to accomplish (or delete) a specific task, item, or procurement. NTE/NLT estimates are prepared from Planning, Budget, or Firm Estimate information. The amount of Contingency or NTE/NLT allowance added is strictly an estimator or management judgment factor.
Delta Estimates Damages Method – The Delta Estimate method is no different than adding up a number of individual Change Order requests to derive the total claim amount. The Delta Estimate becomes difficult to apply if several problems and their effects are interrelated. Also, the Delta Estimate method is often criticized because the sum of the parts may exceed the whole (cost overrun). For example, contractors often calculate overall increases in labor costs by using multiple causes of lost productivity, such as excessive and sustained overtime; stacking of trades; overcrowding; effect of multiple changes; temperature; and others.
Each of these causes of productivity loss is evaluated, and the calculated loss from each cause is summed, to yield the overall productivity loss claim. However, without comparing the resulting total labor increase to the actual labor man-hour variance between the contractor’s control budget and the total actual labor man-hours expended, including consideration for approved and pending changes, the calculation of the sum of the parts may yield a result that is greater than the whole variance. An owner should insist on a review of the contractor’s job cost report to evaluate the actual variance between the control budget man-hours and actual labor man-hours for individual work activities.
Destruction or Damage to Completed Work – Destruction or damage to completed or partially completed work that stops, delays, disrupts, or hinders the contractor’s ongoing or planned work or requires the contractor to perform extra or additional work. If such damage occurs as a result of weather problems, the contractor may have to recover its costs through its insurance policy. Depending on which party is contractually responsible for site security, the contractor may be entitled to a compensable delay if such damage occurs through vandalism or other similar acts after normal working hours and if the contractor was not responsible for other concurrent delays at that time.
Destruction or Damage to Tools, Equipment, Materials, or Supplies – Destruction or damage to the contractor’s tools, equipment, materials, or supplies that stops, delays, disrupts, or hinders its ongoing or planned work, or requires the contractor to purchase, repair, or replace damaged items. If such damage occurs as a result of weather problems, the contractor may have to recover its costs through its insurance policy. Depending on which party is contractually responsible for site security, the contractor may be entitled to a compensable delay if such damage occurs through vandalism or other similar acts after normal working hours and if the contractor was not responsible for other concurrent delays at that time.
Direct Cost – Any cost that is specifically identified with a particular project or activity, including labor, equipment, materials, supplies, or other costs directly benefiting the project or activity.
Discrete Damages/Cost Variance Analysis Damages Method – By applying a variation of the Delta Estimate and Modified Total Cost methods, the claimant can go one step further to provide convincing proof of the damages incurred using an approach known as the Discrete Damages/Cost Variance Analysis method. This analysis method, in addition to evaluating cost growth for each cost account, considers quantity, man-hour, cost, unit price, and unit productivity variance information for each account based on a comparison of the current budget and actual values for these incises. For example, an account impacted by the direct consequences of significant man-hour growth for scope changes, and bid errors for quantity and productivity variations, may explain the vast majority of the cost variance (cost overrun) in the account. Residual labor costs, if any, may be attributable to rework, acceleration inefficiencies, and indirect cumulative impact or disruption which are evaluated separately. Because of the comprehensive nature of this type of analysis, it relies heavily on the contractor’s contemporaneous detailed cost records and reports, and the current budget versus actual quantity, man-hour, and cost variance data derived for each account from this information.
The method involves the specific distribution of all costs incurred on the project rather than quantifying only certain parts of the cost or damage analysis as may be done in the other methods. The credibility of this method is established by separating the cost growth that results from bid error, non-compensable problems, and compensable problems, and then identifying individual compensable problems with specific costs tied to each problem. In addition, the cost growth for each claim problem is applied to each relevant cost account to demonstrate that the “sum of the parts” of each claim does not exceed the whole cost overrun for each cost account.
Equipment-Factored Estimate – An estimating method by which the costs of the major items of installed equipment are estimated and totaled. Estimating factors are then applied to the total of the equipment costs estimate for other costs, such as the costs of civil work, piping, electrical, instrumentation, and indirect costs to derive the total estimated costs for a project. This type of estimate is most often used at the early planning stages of a process plant or power plant project.
Escalation – Use of a price index to convert past to present prices or to convert present to future prices. Cost increases as a result of inflation.
Estimate at Completion (EAC) – Direct and indirect costs (Actual Cost of Work Performed, or ACWP) actually charged to the Work Breakdown Structure (WBS) element to-date, plus the estimate of costs (direct and indirect) for authorized work remaining. The term “Latest Revised Estimate” (LRE) is synonymous.
Estimate to Complete (ETC) – The cost and schedule estimates for completion of all remaining scope.
Fee – Fee represents an agreed-to amount beyond the costs for work performed and is commonly also referred to as profit. In most instances, fee reflects a variety of factors, including risk. Fee may be fixed at the outset of performance, as in a Cost Plus Fixed Fee (CPFF) arrangement, or may vary (within a contractually specified minimum-maximum range) during performance, as in a Cost Plus Incentive Fee arrangement.
General and Administrative (G&A) Costs – Indirect expenses, including a company’s general and executive offices, the cost of staff services such as legal, accounting, public relations, financial, and similar expenses, and other general expenses related to the overall business.
Global Claim – See the following definition:
Global claims may be defined as those where a global or composite sum, however computed, is put forward as the measure of damage or contractual compensation where there are two or more specific matters of claim or complaints, and where it is said to be impractical or impossible to provide a breakdown or sub-division of the sum claimed between those matters. ‘Total actual cost’ or ‘total cost’ are American expressions used…to describe those claims, whether in respect of one only or more than one matter of complaint, where the alleged total costs of [the contractor] … is compared with the contract value or price, and the difference then put forward as representing the measure of damage or additional cost caused by one or more matters complained of. Where more than one separate matter is relied on, as is very often the case, a total cost claim will also, therefore, constitute a global claim as above defined.1
Indirect Cost – The cost incurred by an organization for common or joint objectives that cannot be identified specifically with a particular part of a project or activity.
Jury Verdict Damages – The Jury Verdict method provides the courts another way to calculate damages when the contractor or owner does not present discrete damages. The term “Jury Verdict” is misleading in that most cases that have received damages awards on a Jury Verdict basis involve decisions by courts or Boards of Contract Appeals, not juries. In these cases, judges and board panel members serve the role of a jury and as triers of fact, hearing testimony and weighing evidence, and awarding damages based on an approximation of damages suffered.
Liquidated Damages – Liquidated damages (also referred to as liquidated and ascertained damages) are damages whose amount the parties designates during contract formation for the owner to collect as compensation upon a specific breach (e.g., late performance) by the contractor. When damages are not predetermined/assessed in advance, then the amount recoverable is said to be actual damages to be agreed to or determined by a court or tribunal in the event of breach.
A Liquidated Damages clause may not be enforced if its purpose is to punish the contractor in breach rather than to compensate the owner (in which case it is referred to as a Penal or Penalty clause). One reason for this is that the enforcement of the term would, in effect, require an equitable order of specific performance.
For a Liquidated Damages clause to be upheld, two conditions must be met. First, the amount of damages identified must roughly approximate the damages likely to fall upon the owner as a result of delay. Second, the damages must be sufficiently uncertain at the time the contract is made, so that such a clause will likely save both parties the future difficulty of estimating damages.
Management Reserve – The portion of a project’s or contract’s total allocated budget withheld for management control purposes, rather than designated for the accomplishment of a specific work element or set of work elements.
Modified Total Cost Damages Method – The Modified Total Cost approach is a damages analysis method whereby the claim amount is produced by calculating the difference between an adjusted in-place value and an adjusted bid amount. The adjusted in-place value is determined by taking the project’s in place value (total field costs plus overhead, profit, and bond) and adjusting it downward for identified contractor-caused performance errors and other noncompensable costs.2 The adjusted bid amount is determined by adjusting the original bid (contract) amount for executed Change Orders and identified bid errors. The Modified Total Cost method is similar to the Jury Verdict method, except that the contractor presents the claim value by adjusting the total costs for noncompensable costs and bid errors rather than the “jury” or “trier of fact” making these adjustments.
Overhead – Overhead, overhead cost, or overhead expense refers to an ongoing expense of operating a business. The term “overhead” is usually used to group expenses that are necessary for the continued functioning of a business but do not directly generate profits. Overhead expenses are all costs on the income statement except for direct labor and direct materials. Overhead expenses include accounting fees, advertising, depreciation, insurance, interest, legal fees, rent, repairs, supplies, taxes, telephone bills, travel, and utilities costs.
Parametric Cost Estimating – A cost estimating methodology, using statistical relationships between historical costs and other program variables such as system physical or performance characteristics, contractor output measures, and manpower loading, etc. This estimating technique employs one or more cost estimating relationships for the measurement of costs associated with the development, manufacture, and/or modification of a specified end item based on its technical, physical, or other characteristics.
Progress Payments – Payments made to a contractor, during the life of a Fixed Price Contract, on the basis of a percentage of the contractor’s incurred total cost or total direct labor and material cost. The amounts are usually based on actual expenditures and work performed at a particular stage of completion, or are a predetermined value based on the completion of certain milestones.
Quantum Meruit – For various reasons, the contractor may be unable to recover damages under the original contract. When this occurs, the contractor may pursue recovery under a quasi-contractual remedy known as quantum meruit, which simply means “as much as one deserves.” Such situations may occur when the contract is found to be unenforceable or when the contractor performs extra work that the original contract does not cover. Where quantum meruit recovery is sought, the contractor will set forth its determination of the reasonable value of the benefit conferred upon the owner. The court will usually consider all competent evidence of actual contractor expenditures in determining that reasonable value.
A contractor may recover under a theory of quantum meruit if it can prove substantial performance on the contract and a good-faith endeavor on its part to perform fully under the contract. An intentional departure from contract requirements is per se not in good faith unless 1) the defendant at least in part causes the failure, or 2) the departure is so trifling as to be de minimis. Additionally, a party seeking recovery under a theory of quantum meruit that has been terminated wrongly is excused from proving substantial performance of the entire contract, but it must prove substantial performance and an intention to completely perform up until the date of termination. Quantum meruit may apply when an express contract is abandoned. Courts will seek a remedy such that the contractor is to be paid the reasonable value of its work.
Total Cost Claim – A total cost claim contends that the claimed costs are not caused by the actions or inactions of the contractor and are caused only by the factors for which the owner is responsible and does not detail separate damages as being the result of each specific event. To succeed in a total cost claim, the contractor must do the following:
- Show the bid to be reasonable.
- Show the actual costs to be reasonable.
- Establish that all events contributing to the loss are compensable.
- Demonstrate that there is no other way to calculate the claim.
- Demonstrate that the contractor did not contribute to the increased costs in any way.
Total Estimated Cost – The budgeted costs for land, design, construction, equipment, escalation, and contingency for a given project.
Undistributed Budget – Budget within the performance measurement baseline applicable to the work effort that has not yet been identified to both a responsible organization and a Work Breakdown Structure (WBS) element.
Unit Cost – Usually total cost divided by units of production but can consist of smaller elements and their associated unit costs that make up the total unit cost.
Variable Costs – Raw material costs, by-product credits, and those processing costs that vary with plant output (such as utilities, catalysts, and chemicals, packaging, and labor for individual operations).
Variance – The difference between the expected/budgeted/planned and actual results.
1 Pickavance, Keith, Delay and Disruption in Construction Contracts, 3rd ed., T&F Informa (UK) Ltd, London, 2005, p. 764, paragraph 19.5, citing Duncan Wallace, Ian, QC (ed.), Hudson’s Building and Engineering Contracts, 11th edn, 1995, Sweet & Maxwell, at p. 1086.
2 See Great Lakes Dredge & Dock Co. v. United States, 96 F. Supp. 923 (119 Ct. Cl. 1951); Sovereign Construction Company, Ltd., ASBCA No. 17792, 75-1 BCA ¶ 11,251, at 53,606.
ADDITIONAL RESOURCES
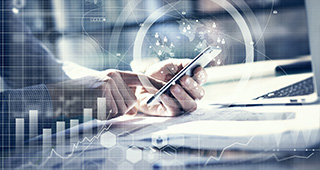
Blog
Discover industry insights on construction disputes and claims, project management, risk analysis, and more.
MORE
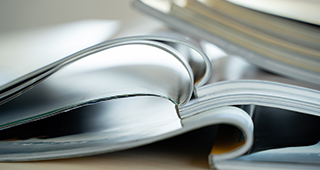
Articles
Articles by our engineering and construction claims experts cover topics ranging from acceleration to why claims occur.
MORE
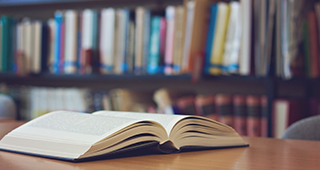
Publications
We are committed to sharing industry knowledge through publication of our books and presentations.
MORE
RECOMMENDED READS
A Tale of Two Claims: Same Contract, Two Fates
The success of a claim often hinges not on what happened in the field, but how it was documented, analyzed, and communicated.
READ
The Role and Benefit of a Consultant in a Construction Project: Part 1
This is the first blog post in a two-part series on the role and benefit of a construction consultant.
READ
Integrated Cost and Schedule Risk Analysis
This article illustrates how an integrated cost and schedule risk analysis can improve cost and schedule forecasts and prioritize risks for further mitigation.
READ