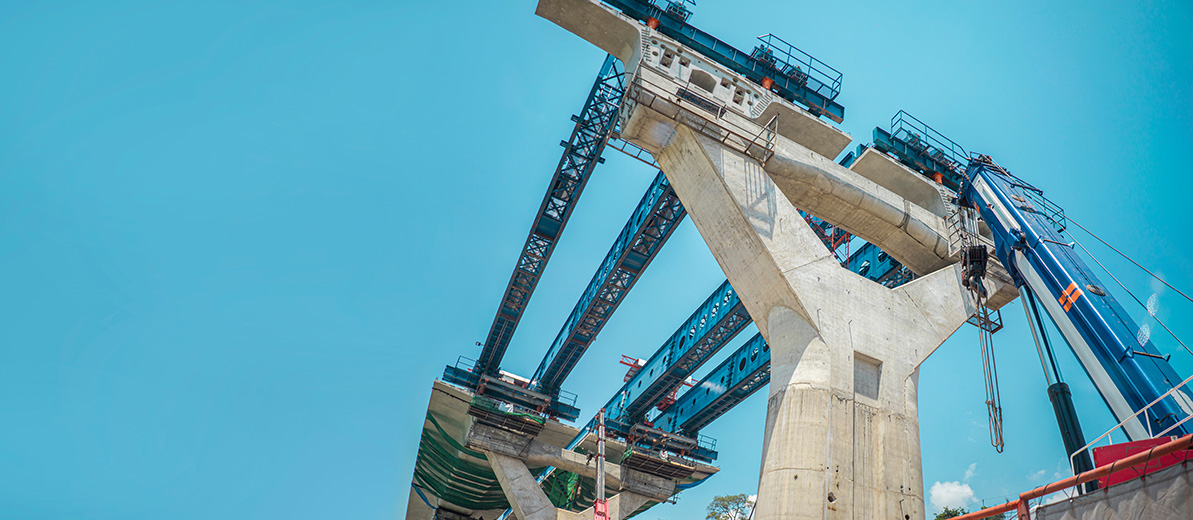
May 15, 2023
Non-excusable, Non-compensable Delays in Construction: Part 1
A contractor who fails to perform within the time specified in the contract or, if no time is specified, within a reasonable period of time, may be liable to the owner for resulting damages and may need to absorb its own increased cost of performance.1
Unless the circumstances preventing timely performance rise to the level of impossibility or commercial impracticability,2 the contractor may shoulder responsibility for unforeseen delays. As one court stated, “It is well-established that supervening circumstances making the performance of a promise more difficult and expensive than originally anticipated is not enough to excuse the promisor.”3
The owner and designer often do not know about contractor problems until they see a major slippage in the schedule. Even then, the exact reasons for the project delay are often unknown. The contractor may allege a variety of causes that are excusable and compensable. The owner may only realize the true causes of delay after an intensive analysis by an independent schedule delay consultant, which is often only performed if the contractor files a formal claim in arbitration or litigation. If the contractor does not file a claim, the owner probably will not perform the analysis. However, if the contract provides for liquidated damages, the owner may not need to identify the specific causes of delay to assess liquidated damages. Alternatively, the owner could make a claim for actual delay damages.
Delays that are attributable to the contractor most often stem from five major causes: (1) failure to evaluate the site or design adequately; (2) contractor management problems; (3) inadequate contractor resources such as cash, material, or labor; (4) construction defects; and (5) subcontractor failures. Examples of non-compensable, non-excusable delays that can result from the first two failures are discussed below, and the next blog post will focus on the last three failures.
Failure to Adequately Evaluate the Site and Design
Most construction contracts provide that the contractor should carefully review plans and specifications and visit the project site prior to submitting its bid proposal.4 However, normal estimating practices and bidding periods do not allow for a careful review of either before the contractor submits its bid. The owner may limit the pre-bid site inspection period to a single designated time,5 which may inconvenience the contractor in its pre-bid activities. Once the bid is submitted, it is too late to rebid the project to include any major omissions. Thus, the contractor who underbid the job and later learns of problems that it did not address in its bid may not have a viable recourse and may look for ways to make up the loss. Techniques that the low-bid contractor may pursue include bid shopping among potential subcontractors, “price squeezing” on designated subcontractors, substitution of less expensive material, and understaffing the work force. These cost-saving attempts may lead to delays and risk exceeding project time requirements.
Even if a careful evaluation is made of the plans and specifications, the low-bid selection method on most public projects incentivizes the contractor to take risks on design interpretation, hope for the best, and try to obtain a change order. The contractor may be obligated to inquire about patent design errors prior to bid submission, and failing to do so, proceeds at its own risk.6 Even if the design is not patently defective, the contractor must base its work plan and estimated costs on reasonable interpretations of the contract documents. Any delay resulting from unreasonable interpretations may be neither excusable nor compensable.7
Another problem area is the dimensions on existing, as-built drawings in rehabilitation work. If the contract documents indicate that the dimensions should be confirmed in the field, the contractor may proceed at its peril.8
Failure to evaluate soil conditions at the project site also leads to numerous disputes. Although many construction contracts provide for additional compensation for differing site conditions,9 the contractor may not always prevail. The trier of fact will often examine whether the contract documents or a site inspection would adequately alert the contractor to the subsurface soil condition. If so, the contractor may not recover on its claim.10 Also, if the contract documents do not misrepresent the soil condition, a contractor may not be able to recover for delays and other costs due to encountering conditions that are not unusual to the area.11 However, a reasonably thorough site inspection may not reveal subsurface problems.12
In performing the pre-bid site inspection, the contractor may be held responsible for determining conditions other than soil conditions, including but not limited to labor availability in the area, other projects that will compete for resources and materials, permitting requirements and normal time for approvals by the authorities, and normal weather conditions.
Contractor Management Problems
The contractor’s responsibility for the construction means, methods, techniques, sequences, procedures, and coordination13 is a continual challenge to its management resources. The general contractor is the planner, manager, scheduler, coordinator, supervisor, and superintendent. Its abilities to manage price, time, and performance are its stock in trade.
Often an increase in new work strains its management resources, spreading them too thin. Dealing with several major projects simultaneously and being unable to predict or control the acquisition of new work often results in delay in mobilizing its resources to begin a new project. The problem is more often the lack of a project superintendent than a lack of skilled laborers. While the owner is responsible for problems in obtaining site access, the contractor is responsible for delays in mobilizing the project.14
Many management failures occur in the coordination of subcontractors rather than management of the contractor’s own forces. The coordination of subcontractors begins with the project schedule, which is the general contractor’s responsibility. If delay results from a deficiency in the contractor’s scheduling of subcontractors, the delay is not excusable or compensable.15 Failure to coordinate the scheduling of subcontractors, such that a subcontractor cannot complete within the subcontract time limits, may be a breach of the subcontract.16
Another major management problem concerning subcontractors is the contractor’s failure to properly distribute responsibility among the subcontractors. Most project specifications are organized around the 16 subdivisions of the Uniform Construction Index: (1) general requirements, (2) site work, (3) concrete, (4) masonry, (5) metals, (6) wood and plastics, (7) thermal and moisture protection, (8) doors and windows, (9) finishes, (10) specialties, (11) equipment, (12) furnishings, (13) special construction, (14) conveying systems, (15) mechanical, and (16) electrical.17 These categories provide a useful distinction for much trade contract work but do not provide a foolproof method to coordinate the scope of subcontracts. The owner is not obliged to organize plans and specifications in such a manner as to permit the general contractor to distribute work among various trade subcontractors without interpretation and coordination.18 Coordination of the scope of the subcontracts with the project specifications is the responsibility of the general contractor.19
Procuring materials and equipment is also the responsibility of the contractor. Delay by the contractor in obtaining materials may not be excusable,20 even if it results from a materials shortage.21 The contractor is responsible for delays caused by a supplier’s failure to provide material or equipment,22 and the supplier may in turn be liable to the contractor for late equipment delivery.23 However, if a supplier encounters excusable delay, the contractor may have no recourse against the supplier but may be entitled to a time extension from the owner, although not additional compensation.
1 Kaltoft v. Nelsen, 106 N.W.2d 597 (Iowa 1960).
2 Compare Semrow v. Harmswood Stables N., Inc., 100 III. App. 3d 219, 426 N.E.2d 988 (1981) (severe weather sufficient to establish legal impossibility) and Tallman Pools of Georgia, Inc. v. Fellner, 160 Ga App. 722, 288 S.E.2d 46 (1981) with Prather v. Latshaw, 188 Ind. 204, 122 N.E. 721 (1919) (flooding that washed out portion of levee under construction by contractor did not render performance impossible, since contractor could complete work once flood subsided). Annot., 84 A.L.R.2d 12 (1962) discusses cases from throughout the United States that apply the doctrines of impossibility and impracticability of performance, including many construction cases. See also Section 2-615 of the Uniform Commercial Code (1978), which codifies the doctrine of commercial impracticability in connection with contracts for the sale of goods.
3 Barnard-Curtiss Co. v. United States, 301 F.2d 909, 912 (Ct. Cl. 1962).
4 See U.S. Government Form 23-A (Construction Contract), General Provisions, Clause 13, 41 C.F.R. § 1-16.901 23A (1983); AIA Document A201-1976, ¶¶ 1.2.2 and 4.2.1.
5 See BECO Corp., Comp. Gen. Dec. No. B217573 (May 15, 1985).
6 Fortec Constructors, ASBCA No. 27479, 83-2 B.C.A. (CCH) ¶ 16,759 (1983).
7 Wilson Pac. Constr. Co., ASBCA No. 28128, 84-1 B.C.A. (CCH) ¶ 17,109 (1983).
8 Meaott Constr. Corp. v. State, 92 A.D.2d 730, 461 N.Y.S.2d 605 (1983).
9 See U.S. Government Form 23-A (Construction Contract), General Provisions, Clause 13, 41 C.F.R. § 1-16.901 23A (1984); AIA Document A201-1976, 11 12.2.1.
10 McDaniel Bros. Constr. Co., ASBCA No. 23917, 83-1 B.C.A. (CCH) ¶ 16,237 (1982).
11 Covco Hawaii Corp., ASBCA No. 26901, 83-2 B.C.A. (CCH) ¶ 16,554 (1983).
12 Singleton Contracting Corp., GSBCA No. 7008, 84-1 B.C.A. (CCH) ¶ 17,137 (1984).
13 See AIA Document A201-1976, ¶ 4.3.1.
14 Burns v. Hanover Ins. Co., 454 A.2d 325 (D.C. App. 1982).
15 William F. Klingensmith, Inc., GSBCA No. 5520, 83-1 BCA (CCH) ¶¶ 16,159, 16,479 (1983).
16 Able Elec. Co. v. Vacanti & Randazzo Constr. Co., 212 Neb. 619, 324 N.W.2d 667 (1982); Hunter Bros. Systems, Inc. v. Brantley Constr. Co., 332 S.E.2d 206 (S.C. 1985).
17 Uniform Construction Index, Construction Documents and the Project Manual (Construction Specifications Institute, 1980).
18 H. Fair Assocs., Inc., ASBCA No. 26950, 82-2 BCA (CCH) ¶ 16,112 (1982).
19 Centex Corp., ASBCA No. 26773, 83-2 BCA (CCH) ¶ 16,829 (1983); Dawson Constr. Co., Inc., ASBCA No. 29447, 85-1 BCA (CCH) ¶ 17,862 (1985).
20 Malor Constr. Corp., IBCA No. 1688-6-83, 84-1 B.C.A. (CCH) ¶ 17,023 (1984); Appeal of Karl Kraus Constr. Co., GSBCA No. 2808, 69-2 B.C.A. (CCH) ¶ 7960 (1969).
21 Allied Paint Mfg. Co. v. United States, 470 F.2d 556 (Ct. Cl. 1972).
22 Howard L. Dressler Co., GSBCA No. 3616-9, 73-1 B.C.A. (CCH) ¶ 9818 (1972); Cline Constr. Co., ASBCA No. 28600, 84-3 B.C.A. (CCH) ¶ 17,594 (1984).
23 Usemco, Inc. v. Marbro Co., 60 Md. App. 351, 483 A.2d 88 (1984).
RECOMMENDED READS
Excusable, Non-compensable Delays
This post discusses excusable, non-compensable delays, which entitle contractors to time extensions but not damages.
READ
Excusable, Compensable Delays
This post discusses excusable, compensable delays, which entitle contractors to both compensatory damages and time extensions.
READ
An Overview of Excusable Delays
This blog post discusses excusable delays in construction, including compensable and non-compensable delays.
READ