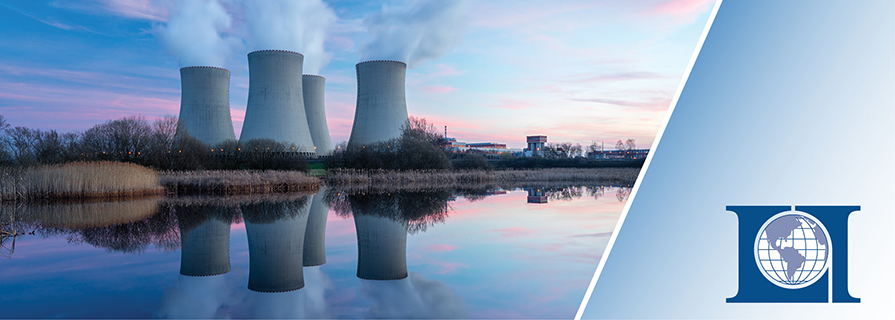
STO Scope Management for Nuclear Power Plant Construction to Mitigate Claims
This article explores how STO (Shutdown, Turnaround, and Outage) scope management principles can mitigate claims and improve scheduling in nuclear power plant construction projects. While these techniques help control emergent scope during plant outages, applying them incorrectly in construction may lead to delays and cost overruns. The article evaluates whether adapting outage management to new-build projects can reduce risks and enhance performance in the U.S. nuclear industry.
1. INTRODUCTION
The 1979 Three Mile Island accident effectively sent the American nuclear power industry back to the Dark Ages. Between 1974 and 1982, U.S. electric utilities canceled more than 120 nuclear power plant projects, often halting construction projects that were already well underway.1 While public concern over safety was indeed a factor in local utility decision-making, utilities nearly always cited project economics as the key reason for cancellations. Construction of nuclear facilities had been, almost without exception, undermined by significant cost and schedule overruns. In the 1980s and 1990s, the financial fallout from nuclear projects led many U.S. utilities into severe financial distress, including the record-setting Washington Public Power Supply System (WPPSS) default on $2.25 billion in municipal bonds in August 1983.2
There are now signs that the American nuclear Dark Age may be ending. Public opinion has shifted in favor of renewable energy sources. Licensing requirements are being streamlined. Subsidies and incentives have been passed into law. The 2005 Energy Policy Act passed by Congress provided $13 billion in subsidies and incentives for the first six new plants alone, and the federal government also tripled loan guarantees to $55 billion in order to jump-start construction. The U.S. Department of Energy (USDOE) projects a 45% growth in electricity demand by 2030. To maintain its share of total power production, the U.S. nuclear industry must construct as many as 50 new nuclear plants during the next 15 years.
The U.S. Nuclear Regulatory Commission (NRC) has already received applications for 30 additional reactor blocks and, after some initial false starts in Texas and Maryland, new projects are finally underway. In 2010, the first $8.5 billion in loan guarantees were allocated to the first two new plants to be commissioned since the 1970s and, in February 2012, the NRC approved the construction of two new 1,000 MWe plants.
In theory, several key technological and regulatory advances now make nuclear power a more attractive investment. Current plants are more cost-effective to run; next-generation reactors are safer and more reliable; streamlined licensing processes reduce the lag time between investment decisions and the start of construction; and standardized construction is expected to provide construction efficiencies. Yet, while more favorable public opinions regarding nuclear power, improved regulatory environments, increasing energy demand, and standardized modular designs may help to initiate more nuclear projects, none of these factors will guarantee the completion of these projects on time and on budget.
Consider, for example, the schedule and budget performance for the initial projects of this new American nuclear construction era. The expansion of NRG’s South Texas Project from two units to four units, begun in 2007, was shelved in 2015. NRG cited macro-economic concerns and decided to focus instead on thermal district energy systems. The expansion of Calvert Cliffs 3 in Maryland was also hampered by financing costs in 2010 and the later restructuring of Areva in 2015.
Nuclear projects are generally financed on balance sheets, which means they must be built in a way that does not threaten their long-term economic viability. The revival of nuclear power generation as a viable base-load, non-polluting, and carbon-free source can be achieved only if we can first find new ways to build on-time, on-budget, cost-effective plants. Even under the best regulatory conditions, no nuclear plant will be built if capital costs per megawatt of installed capacity end up totaling almost four times the cost per megawatt of gas-fired base load capacity.
Nuclear power plant construction experts struggling with this issue, both in the U.S. and abroad, have focused heavily on design simplification and modularization. Greater standardization is expected to lead to higher efficiency. In addition, modularization is expected, as in other areas of the construction industry, to facilitate cost savings via offshoring much of the construction process to yards, where work can be completed under more controlled and potentially less environmentally sensitive conditions, and in locations with lower labor costs than those at the civil construction site.
Yet modularization is not a panacea. As discussed in a previous article, modularization comes with its own challenges, including quality control issues and delivery delays compounded by distances. For the U.S. nuclear industry, modularization might meet with further social or regulatory resistance to any apparent or actual offshored manufacturing of sensitive nuclear technology. Paradoxically, modularization can compound, rather than mitigate, the disruptive effects of uncontrolled scope changes on a construction schedule and can, thus, increase the likelihood of complex protracted litigations.
Complex construction claims and related delays and cost overruns often arise from uncontrolled scope changes termed “scope creep.” Scope creep can undermine the success of a project by hampering productivity, requiring rework, disrupting resource allocation, and defeating acceleration attempts. When combined with acceleration, overtime, night shifts, and other recovery measures, scope creep typically results in a higher rate of defective work and extended testing and commissioning, lost productivity, extended durations, and additional cost claims. The more complex the construction and supply chain of a nuclear project, the more disruptive the effect of scope creep. While modularization incentivizes design standardization and manufacturing improvement, it is not, in itself, sufficient to guarantee delivery of a project on time and on budget. If not firmly coupled to scope discipline, modularization may in fact create a more fertile ground for construction claims and delays.
The most important factor in developing an economically viable nuclear construction industry may, thus, not be modularization or design simplification (although these may be part of the solution), but rather scope discipline, scrupulously documented, tracked and enforced by a scope audit group independent from the project management leadership.
Although this framework already exists on shutdown projects, it has not yet been systematically implemented in the context of new build construction. Project Managers who coordinate maintenance outages for online nuclear facilities have been tightly focused on scope management and developing rigid organizational techniques to control the emergent scope from impacting outage performance. For cost and schedule management purposes, it is proposed that the scope control techniques developed for shutdown and outage management also be implemented in the context of new nuclear power plant construction. Disciplined control of emergent scope is a promising claim mitigation and scheduling technique but if applied outside the inflexible project control framework developed by shutdown managers, it could, instead, add to the woes of the U.S. nuclear industry.
2. THE NEW CONSTRUCTION PERFORMANCE IMPERATIVE
Industry initiatives for developing best practice standards on nuclear power plant construction projects have been evolving over the past four decades. Unfortunately, the renewed focus on construction performance and scheduling pioneered in the late 1990s by the Electric Power Research Institute (EPRI) seems to have been lost amid complex engineering and regulatory debate over consensus-based initiatives such as the Generation IV International Forum (GIF).
The fulfillment of EPRI’s goal (construction time reduced to three years or less, from groundbreaking to fuel loading) requires more sophisticated delivery and claims mitigation techniques than a mere cost-based approach solely based on benchmarking. As suggested by EPRI’s URD program, construction management should follow a “simplification” process similar to design standardization. However, while the promise of design standardization has been at least partially realized through a production modularization and offshoring framework, no equivalent project delivery framework has apparently been researched and adopted.
2.1 EPRI’S PUSH FOR AN ACCELERATED CONSTRUCTION SCHEDULE
The NRC has historically focused primarily on ensuring worker safety, not on speed of construction. Since 1973, The Electric Power Research Institute (EPRI), a nonprofit organization funded by the electric utility industry, has emerged to complement NRC’s safety emphasis with additional attention to design, construction, and operation efficiency. EPRI has initiated several programs to incorporate optimized fabrication and construction practices into new design development.
Working closely with utilities, nuclear industry groups, regulatory agencies, and major vendors, EPRI has supported the design of Advanced Light Water Reactors (ALWRs) that are far simpler, safer, and more economical than conventional units. The EPRI program, launched in the 1980s, has addressed the broad institutional issues, such as public acceptance, financing, and regulatory reform, needed to revitalize the nuclear industry in the United States. With construction of the first ALWR reactors still a distant future prospect, EPRI has focused particularly on design solutions and operational costs.
EPRI worked with domestic and international utility companies to define the characteristics that advanced plants should have in order to meet those companies’ needs. The result was the Utility Requirements Document (URD), which specifies the technical and economic concepts for a simplified plant. The new plant was to be:
- simpler and have higher design margins and enhanced safety features;
- economically competitive with other forms of generation;
- standardized; and
- pre-licensed by the NRC.
More critically, this new kind of nuclear power plant was to be built in less than 54 months (4.5 years). In fact, EPRI claimed in 1994 that construction time could and should be reduced to three years or less, from groundbreaking to fuel loading.
Gains in productivity and reduced construction time were supposed to be achieved by: 1) the use of accelerated and well-controlled construction schedules, 2) standardized design, and 3) modular construction.3
The URD provided detailed specifications for standardized design, which would improve efficiency by allowing contractors to benefit from repetition. The simplified modular design was also to result in fewer valves, less safety-grade piping, fewer pumps, and less control cable. The use of fiber optic cable was also expected to significantly reduce the need for copper cabling; this would reduce construction time. Finally, the simplified designs would allow for an extensive modular approach in which the basic reactor and balance-of-plant components would be fabricated in a factory, then shipped by rail or barge to the construction site for assembly.
Despite EPRI’s thoughtful approach to the details and implications of design modularization, less attention seems to have been paid to the improved management systems required to implement the “accelerated and well-controlled construction schedules”4 envisioned by EPRI. In 1994, EPRI suggested the adoption of advanced information systems and a widespread simplification of all the activities normally associated with plant construction and operations.
Process improvement and simplification has been a constant focus of maintenance teams since an operator of nuclear power plants in Sweden explored, in the middle of the 1990s, the possibility of adapting manufacturing workflow task management to replace paper-based sign-off processes. These practices later became subject to research interest as comprehensive review of best practices for turnaround planning and management became possible. Research papers in the 2010s started to aggregate guidelines and recommendations based on existing best practices to support managers and engineers involved in turnarounds. These studies identified gaps and commonalities between turnaround practices and developed systematic methodologies for turnaround planning and management processes. No similar level of interest has been invested in the study of the gaps and commonalities between turnaround best practices and plant construction best practices.
EPRI has not yet dedicated significant research resources to further developing recommendations regarding the activity simplification and accelerated schedule it proposed in the 1990s. For a project to obtain true benefits from any systematic simplification of activities – i.e., from limiting the number of activities to be scheduled, tracked, and executed – the project must first implement protocols to prevent that number of activities from being increased via mid-project scope creep, whether caused by poorly defined scope or by emergent scope.
The construction of two advanced light water reactors by Hitachi-Toshiba-GE at Tokyo Electric Power Company’s (TEPCO’s) Kashiwazaki-Kariwa site, northwest of Tokyo, Japan proved that the URD initiative’s 54‑month goal was feasible. The first (KK‑6) reactor started construction on November 3, 1992, and was commissioned on November 7, 1996, 48 months later. The second (KK‑7) reactor also took 48 months to complete from the start of construction on July 1, 1993, to commissioning on July 2, 1997.
In 2010, EPRI hailed the performance of the Hitachi-Toshiba-GE JV as the benchmark for future construction in the U.S. and the case study for the benefit of modular construction. The plant design includes 193 modules, ranging from 5 metric tons (5.5 tons) to 650 metric tons (717 tons).5 The applicability of the EPRI benchmark study to the U.S. nuclear industry, however, may be questionable. In Japan, Hitachi-GE has been building with modules since the 1980s. Modular fabrication requires experienced manufacturers, and experienced nuclear industry manufacturers are in short supply in the U.S. It remains uncertain whether a U.S. modular fabricator/contractor team would be able to match the Hitachi-Toshiba-GE team’s impressive scheduling accomplishment. Suppliers would either be offshore, if experienced, or inexperienced, if local. Even if the Hitachi-Toshiba-GE team players were operating in the U.S., the regulatory environment is quite different, which may affect schedule performance.
2.2 FROM URD TO GIF: DIMINISHED FOCUS ON OPERATIONAL SIMPLIFICATION AND SCOPE MANAGEMENT?
On the heels of the EPRI-supported URD, the USDOE began pursuing an initiative to develop standards for fourth-generation nuclear technology. Generation IV International Forum (GIF) meetings began in January 2000 when the USDOE’s Office of Nuclear Energy, Science and Technology convened a group of senior governmental representatives from nine countries to begin discussions on international collaboration in the development of Generation IV (Gen IV) nuclear energy systems. GIF has preselected six nuclear reactor designs, with the selection process based not only on technical grounds (including safety), but also on cost, with the goal of making nuclear power better able to compete on economic grounds with natural gas and other traditional sources for generating electricity.
Toward that end, in 2007, GIF issued a cost model6 with two key mandates: 1) that construction scheduling for new projects be modeled and estimated based on past performance, and 2) that new projects rely on modularization as a means of standardizing and controlling costs. EPRI’s benchmark report on Modularization of Equipment issued in 2010 endorsed this approach.7
GIF’s requirement for realistic schedules based on past performance altered EPRI’s initial focus on the development of new information and management systems required to implement “accelerated and well-controlled construction schedules.”8 While in 1994 EPRI had recommended adoption of advanced information systems and a widespread simplification of all activities normally associated with plant construction and operation, 13 years later this focus on simplified activities (with its implied awareness of the significance of scope control) disappeared from GIF’s cost model.
Neither of GIF’s two requirements is entirely unproblematic. Modularization, first, can solve some productivity and quality assurance problems, but it can also significantly increase delivery risk and related claims.9 Second, the on-off-on chronology of nuclear construction in the United States greatly complicates the GIF recommendation to rely on past data to model and estimate for new projects.
The Gen IV cost model requires use of historical data for planning and estimating purposes. However, it is not clear what historical data would be most reliable for these purposes. Most obviously, there has been little nuclear construction in the U.S. since 1979. Additionally, the construction industry as a whole has seen enormous changes in the past three or four decades, suggesting that past data may have little value. Because there has been limited nuclear construction in the U.S., most know-how and most relevant suppliers and contractors are now based in Europe or the Asia-Pacific region. Although the nuclear energy industry pioneered modularization in the 1970s, most American suppliers later ceased doing business or moved operations overseas. It must be noted as well that prior to 1979, many U.S. nuclear projects had failed from a delivery perspective, which limits the predictive value of information from those projects.
Many international projects have also failed in strict project-delivery terms. While we know quite a bit about international projects that have failed, we know less about successful projects. There has been little industry-wide reporting of organizational performance, construction productivity, and progress data for successful nuclear power plant construction projects. While it is relatively easy to learn from troubled projects, including those from the 1970s, it is much harder to derive best practices from the few projects completed on time and budget. Moreover, as suggested above, the successful Japanese projects documented in EPRI’s 2010 benchmarking study may be of limited applicability to the U.S. market.
To move toward more successful project delivery outcomes, investments are needed not only in technical design but in developing: 1) the organizational structures needed to deliver the project on time and 2) the planning techniques or methods needed to achieve that goal. Instead of reaching backward to past new-build nuclear projects built late and over budget, this planning technique/methodology might more appropriately be adapted from existing and well‑documented best-practice models for outage operations. It is understood, however, that outage‑planning systems have been designed for projects with limited duration and scope, long pre-construction planning periods, and repetitive scope, within a relatively controlled environment. Consequently, the transfer of knowledge to the new-build environment would require significant adaptation.
A renewed focus on the development of new information and management systems required to implement “accelerated and well-controlled construction schedules” is all the more critical for the North American nuclear industry given that modularization is unlikely to yield immediately the full benefit of design standardization and off-site construction.
Mismanagement of scope changes and related disruption claims often results in protracted and complex construction disputes. An inadequate assessment of the unique challenges that new construction projects will face during this transition period could result in project delivery failures, soaring costs, and significant delays.
2.2.1 The U.S. Modularization Conundrum
The nuclear industry has utilized prefabricated and preassembled modules for many years. U.S. projects in the 1970s had already implemented many of modularization’s key strategies. A critical change, however, has occurred since the 1970s – heavy manufacturing has now moved outside of the U.S. Today modularized construction means stretching the project site footprint over an international network of suppliers and yards. This is not a concern for bulk-commodity supplies. However, it is a critical risk for the nuclear industry, which relies on fabrication yards for supplying unique components based on stringent and localized quality requirements.
The emerging coordination around the joint development of the next generation of nuclear technology – initiated by the EPRI-supported URD and now under the auspices of the Generation IV International Forum10 – may lead, in time, to simplification of plant design and reduced construction time. In theory, multiple modules can be fabricated while the civil engineering work is progressing at the site, in preparation for receiving the modules. This approach reduces site congestion, improves accessibility for personnel and materials, and can shorten the construction schedule. It can also significantly reduce on-site workforce requirements.
The impacts of offshoring on modular construction have been most pronounced in the U.S. In the 1940s, the war effort involved U.S. manufacturers in pioneering heavy industrial modular construction on a large scale.11 In the 1970s, the U.S. still had substantial heavy infrastructure, but U.S. forging capacity has not been significantly upgraded since. When the first- and second-generation nuclear power plants were built in the U.S., their modular components came primarily from integrated U.S. suppliers, such as Westinghouse, who required little from external suppliers. Today most fabrication takes place at a range of international suppliers, while U.S.-based vendor companies such as Westinghouse, Areva, and CB&I are solely focused on design, engineering and project management.
Steelmaker ArcelorMittal, based in Luxembourg, now owns the U.S. company that in the 1970s and 1980s built most U.S. reactor pressure vessels. China, Japan, South Korea, India, Europe and Russia are all well ahead of the U.S. in terms of modular fabrication capabilities. Today’s very heavy forging capacity operations are in Japan (Japan Steel Works), China (China First Heavy Industries, China Erzhong, SEC), France (Le Creusot), and Russia (OMZ Izhora). New heavy forging capacity is being built in Japan (JSW and JCFC), China (Shanghai Electric Group), South Korea (Doosan), Czech Rep (Pilsen), and Russia (OMZ Izhora and ZiO-Podolsk) – not in the U.S.12
Managing quality and capability challenges along the supply chain is crucial to reliable and efficient delivery of new projects. Yet in the U.S., manufacturing capability for safety-related components and systems has been eroded with the general geographical shift in heavy industry and the scarcity of new U.S. nuclear projects since the 1980s. Meanwhile, in emerging industrial countries, vendors have been slow to upgrade to meet the stringent requirements expected in the nuclear industry.
Even as its supply chain has grown increasingly complex and has moved to manufacturing hubs with limited experience in ASME and European nuclear safety standards, the industry is attempting to move towards co-generation for higher economic returns. Thus, instead of dissipating reactor heat, the next generation reactor would produce steam for large industrial applications such as hydrogen production or desalination. As such, Gen IV nuclear plants would be competing with gas-fired cogeneration plants for industrial applications.
2.2.2 Limited Focus on Project Delivery Techniques
The weakened U.S. manufacturing base challenges EPRI’s and GIF’s assumptions regarding the initial cost benefits of modularization. The GIF cost-estimating guidelines include all relevant life‑cycle costs, including deployment, i.e. design, construction, and commissioning. This cost structure comes from pre‑1993 USDOE data, derived from earlier Oak Ridge National Laboratory nuclear energy plant databases (NECDB). The previous cost models used by USDOE were based on onsite reactor system construction, at a central construction site, with limited use of modular fabrication, under a single regulatory regimen. In contrast, the new cost model requires:
- just-in-time site work;
- multi-modular BOP systems;
- both monolithic and modular concepts for reactor;
- modular systems using factory construction of subsystems and onsite installation sequencing.
The delivery model upon which the cost model is based relies on “traditional U.S. business practices” – a delivery model that apparently requires separate prime contractors for engineering, site construction, modular fabrication, and fuel cycle facilities.13 The possibility of using an integrated vendor to construct the facilities is not excluded. However, the nuclear industry must also manage changes and scope growth risks and should reassess traditional practices. Historical data regarding the U.S. nuclear field points to cancelled projects, construction delays, and cost overruns. Non-traditional shutdown and outage management practices, such as emergent scope management through tracked and auditable organizational processes, on the other hand, have led to significant productivity and operational gains. GIF’s cost model remains, however, silent regarding which construction model and techniques will deliver the expected cost saving of modular design.
A cost-based approach to new-build construction that is solely based on benchmarking projects built under non-transferable operational conditions may not realize the initial objective of EPRI: that construction time could be reduced to three years or less, from groundbreaking to fuel loading. An accelerated delivery model will be critical to delivering competitive nuclear assets. As suggested by EPRI’s URD program, project delivery should follow a “simplification” process similar to design standardization – i.e., a widespread simplification of all the activities normally associated with plant construction and operations.
However, more R&D resources should be invested towards articulating a working model that effectively simplifies the project planning process. The directly related issue of scope control has been, in recent years, the cornerstone of turnaround and outage management. Reviewing these scope control and simplification techniques developed for outage management, and adapting these to new-build construction, may be critical to successfully delivering the next generation of nuclear plants in the U.S.
3. CAN THE OUTAGE/STO SCOPE CONTROL MODEL FULFILL EPRI’S SCHEDULE ACCELERATION MANDATE?
The fulfillment of EPRI’s goal (construction time reduced to three years or less, from groundbreaking to fuel loading) requires more sophisticated delivery and claims mitigation techniques articulating a working model that effectively simplifies the project planning process, controls scope creep, and delivers the promises of planning simplification. The directly related issue of scope control has been, in recent years, the cornerstone of turnaround and outage management. Reviewing these scope control and simplification techniques developed for outage management, and adapting these to new-build construction, may be critical to successfully delivering the next generation of nuclear plants in the U.S.
The implementation of “accelerated and well-controlled construction schedules”14 requires the widespread simplification of all activities normally associated with plant construction and operations. Delivery efficiency, then, requires tight scope management. Furthermore, no delivery organizations have been more focused on scope management than outage teams.
Shutdown teams, operating under tight constraints, have become highly effective, process-oriented and disciplined. Outage operations have seen operational improvement by implementing lean construction strategies and embracing detailed production planning, pre-planning and training. More critically, substantial investments have been made in the organizational and technical capabilities of maintenance departments.
The transfer of technical best practices between shutdown management and new build construction is not, however, self-evident. Such a transfer requires a sustained focus on accompanying organizational capability building. Insufficient attention to key differences in project context seems, in some cases, to have had unintended detrimental consequences. When applied to the “uncontrolled” scope of a new-build construction project, the minutiae of shutdown scheduling can result in project control paralysis. The worst-case scenario result of such a misguided implementation is an unmanageable Level 3 schedule with over 75,000 detailed activities, developed without an equivalent investment in project controls and claims management capability building.
3.1 CURRENT STATUS OF CONSTRUCTION PERFORMANCE
In 2016, more than 60 new nuclear plants are under construction around the world. Many more are in development. These plants must overcome a number of regulatory, economic, technical, and social challenges prior to licensing. However, first and foremost, they must be built on time and within budget. Delays in construction are a key factor behind rising costs. And because nuclear power is already more expensive than other sources of electricity generation, these delays and overruns further undermine the claim that special nuclear subsidies are an essential part of the world’s climate change strategy.
Yet the industry restart has so far been a rough one. The four projects at the top of USDOE’s list are all experiencing cost overruns, reactor engineering difficulties and JV disputes – even prior to project starts. In fact, all five new reactor projects now under construction in the U.S. are reporting delays and cost overruns.
Among these troubled nuclear projects is the Bellefonte Nuclear Power Plant. Construction of Plant started in 1974 at the Hollywood site in Alabama. When construction was halted in 1988, 14 years later, Unit 1 was only 88% complete and Unit 2 was at 58%. After contemplating a construction restart in 2011, the Tennessee Valley Authority determined that it would be unlikely to need a large plant like Bellefonte for the next 20 years. $2.5 billion has been spent to date.
Construction of the Watts Bar nuclear power plant began in 1973 and was also suspended in 1985. Unit 2 was 80% complete when construction on both units was stopped. Unit 1 was finally completed in 1996, and Unit 2 was completed in 2015. America’s first new nuclear power plant to be built in the 21st century thus took 43 years to complete, and the last phase was completed behind schedule and $200 million over budget. The first construction phase of Unit 2 amounted to $1.7 billion. Unit 2 completion work (the last 20% plus post-Fukushima safety upgrades) was planned to cost an additional $2.5 billion. Final costs totaled $4.7 billion. Critics of nuclear power have said that the rising cost of Watts Bar reflects the industry’s ongoing problems in bringing projects to completion at forecasted prices. Cost overruns in the past at nuclear construction projects – with final costs sometimes running to more than 10 times the original forecast – have made Wall Street investors and many utilities wary about building more nuclear power plants.
New Hampshire’s Seabrook power plant, in operation since 1990, is still half-completed (Unit 2 is an empty steel shell). In Washington State, only one of the five plants started in the 1950s by Energy Northwest (then called Washington Public Power Supply System) has been completed and is in operation. Construction on Washington’s nuclear power plants was halted mid‑project in 1982 when costs ballooned to $24 billion, $8 billion over budget, causing the largest municipal debt default in U.S. history.
Public opposition on safety grounds remains a factor for public utilities considering a return to nuclear power. Local opposition to LILCO’s Shoreham reactor in New York resulted in its shutdown only a few hours after commissioning. Nevertheless, cost remains the overriding factor. The U.S. nuclear power industry has been plagued by construction delays and cost overruns for the last 40 years.
Cost overruns are not, however, only a U.S. concern. While on certain Chinese projects’ reported construction performance has been spectacular, there are now eight reactors throughout the world that have been listed as “under construction” for more than 20 years. Experts are reporting that 75 percent of nuclear reactors under construction worldwide are facing delays, which, in turn, make those projects much more costly. As for the other 25 percent, serious doubts have been raised regarding compliance with local and international safety regulations.15 According to the World Nuclear Industry Status Report 2014, other countries are in no better position than the United States when it comes to delivering nuclear reactor projects on time and on budget. Through September 15, 2014, at least three out of four (49 of 66) reactors under construction around the world were running behind schedule, most of them significantly delayed (several months to several years):
- Long-delayed construction projects include three Russian units, two Mochovce units in Slovakia, and two Khmelnitski units in Ukraine.
- One reactor, the Indian Kudankulam-2 unit, has been listed as “under construction” for 12 years.
- Due to massive opposition, work on two Taiwanese units at Lungmen was stopped in April 2014 after about 15 years of construction.
- For the first time, major delays have been officially admitted relating to projects in China. 21 of the 28 units under construction in China are experiencing delays between several months and over two years.
- France’s Flamanville‑3 is running about $7 billion over its initial budget and now projected to cost more than $11 billion.
All of the 18 remaining units under construction worldwide were started within the past three years or have not yet reached projected start-up dates. This makes it difficult to assess whether or not these projects are on schedule. Globally, long-delayed reactor projects are billions of dollars over budget. The nuclear industry cannot sustain such large cost overruns in the context of cheap fossil fuels and competing clean generation sources.
3.2 LEARNING FROM SHUTDOWN
The reasons behind nuclear projects’ gradually increasing construction times are not well understood. Continuously increasing safety requirements may have played a role (as we see directly in the case of the Watts Bar project, where post-Fukushima safety upgrades added time and $150 million of extra costs). Yet for most projects, the impact of safety requirements should have been mitigated by design simplification and modular fabrication. In fact, the real driving factor behind increasing construction times and costs appears to be increasing system complexity and its interplay with scope and design management during construction.
The countries with the best construction times have also the worst safety records. Construction times over the past decade were significantly shorter in Japan and South Korea than elsewhere, with 4.4 years and 4.5 years on average to completion for the four units built in each country.16 However, recent history has raised doubts in both countries over quality control issues, with Japan having to reinvent a Nuclear Regulation Authority and South Korea recovering from a major scandal involving widespread forging of safety-relevant quality-control documents.
This undesired tradeoff of diminished safety for higher efficiency, by contrast, has not been seen in shutdown and live maintenance projects, where we have seen substantial simultaneous progress in reliability, performance, and risk management.
Operational shutdowns, turnarounds, and outages (STOs) command significant capital and operating budgets. Once a nuclear plant achieves commissioning, time is a critical resource. Every day that the reactor is down costs a large amount of money in lost earnings – and this damage is immediately quantifiable, measured, and tracked. STOs thus attract the attention of shareholders and boards of directors, and impact inventory supply chains and customer relationships. They are “whole business events.” Considering all the potential ramifications, well‑executed STOs can represent a source of competitive advantage. They can drive commercial performance, boost morale, bring recognition to high-performing teams, and accelerate individuals’ careers.
The corollary to this success, of course, is that poorly executed STOs can cost an organization millions of dollars in lost revenue, drive up operating costs, and cause permanent damage to the careers of those involved. This has long been true but is amplified in the current operational environment, where most organizations are operating with reduced workforces and resources.
Turnarounds are unique maintenance projects with a high probability of scope change, time delay, and cost overrun. Negative effects stemming from such uncertainties can be mitigated by following best practices for turnaround planning and management. An outage operation’s task‑driven, detailed construction schedule – based on time increments as small as 15 minutes or even one minute – is an incredibly effective tool, but only when integrated within an organization that has the ability to maintain and implement such a planning tool. The minutely planned STO schedule, the glue of outage activities, would be ineffective without implementing management technologies: process flow and detailed procedure, performance monitoring of both trending and predictive indicators, almost daily review of shutdown key performance indicators, and continuous lean process improvement through precision planning and scheduling and execution.
Ultimately, all these techniques are based on a single shared concept: scope management. It is well accepted that a shutdown must be scheduled (when and who executes what), that all the activities must be planned (what, how, all the tools, spare parts and materials, lock out tag out etc. identified), and all the maintenance crews trained to perform these activities before the shutdown begins. However, every shutdown also has a time for freezing its scope, as well as processes in place for controlling scope increase. After the freezing point in time, no new activity is accepted without first passing a formal review process. Key Performance Indicator (KPI) measurements are used to challenge shutdown organization and prevent scope creep. The number of added activities (new or revised scope) after the freezing point in time and during the shutdown is measured.
STO projects typically recognize three categories of work scope: known scope, anticipated scope, and emergent scope.
- Known scope – deterministic certainty.
- Anticipated / contingent scope – quantifiable statistical probability or known unknown, based on estimates from inspections and other condition-based analytical results.
- Emergent scope: unknown unknown, e.g., differing site conditions, resulting in claims.
To a great extent, the precise scope of work remains unknown right up to the beginning of a turnaround, when the equipment is disassembled and examined. Despite considerable improvement in techniques for predicting corrosion rates and other operating wear and tear, there remains an element of surprise when equipment is opened and cleaned for inspection. Radioactivity can compound the potential disrupting effect of emerging work.
This emergent work must then be addressed with limited execution time. In order to minimize loss of production, STOs have a very dense schedule of parallel activities. An STO schedule should in fact be almost completely near-critical, with multiple critical or near-critical paths, and few lags.
Management of the emergent scope is, therefore, the most critical function of shutdown management. Each emergent scope item is verified and approved by STO and departmental heads.
Emergent scope classified as safety critical is always addressed. However, emergent scope classified as core performance critical and reliability critical (i.e., need shutdown to complete) and other activities may be delayed to the next STO (they would then become ‘known scope’) or may be transferred to the routine (online) maintenance log. Such items may cause a decrease in performance but not prohibit operation.
Non-critical items are then assessed from performance, reliability, and cost perspectives. They can be deferred and then added to the “known/anticipated” scope of the next maintenance schedule. Deferred emergent scope, thus, becomes known/anticipated scope for the next shutdown.
The most critical role of STO Project Managers is to manage the trade-offs required to maximize the overall outage effectiveness (i.e., address critical emergent scope) while staying within the constraints of budget and time. This scope management discipline is so engrained in the STO operational culture that a Project Manager is generally referred to as the “Scope Manager.”
Most STO organizations have three organization charts developed during the two-year planning process leading up to the outage start. These are created in the following sequence during various points in the process:
- Scoping organization chart
- Planning organization chart
- Execution organization chart
Given ongoing reductions in personnel, the typical STO organization follows a matrix organization model rather than a pure functional organization model. Members from other areas in the STO organization are involved with scoping, planning, and execution. Typically, all members belong to a Plant Turnaround Services (PTS) department, which is solely dedicated to managing the planning, preparation, and execution of the plant turnaround maintenance – i.e., the project team and its project services group.
Balancing reduction in planned scope to allow for necessary emergent repairs based on inspections is a joint decision. The Project (Scope) Managers give their recommendations but the final decision is taken by the STO Superintendent. His or her decision is then reviewed and ultimately approved/rejected by the plant functional managers and Plant Director.
One critical aspect of the PTS’s scope management function is continuity and ownership. It is not an ad-hoc or short-lived structure, managed and staffed by contractors on the EPCM model. The PTS thus avoids the agency conflict associated with EPCM management, namely cost‑reimbursable EPCM contracting without at-risk normative culture and with limited incentive to manage emergent scope.
The plant functional managers and Plant Director generally comprise the turnaround steering committee team. They provide direction, oversight, and guidance to the execution team and ensure that the turnaround meets the needs of the business. More importantly, the steering committee ensures that the scope aligns with the budget for the turnaround.
The steering committee monitors scope management KPIs and manages an STO construction audit team. The construction audit team is generally under the direct control of the steering committee, not the STO Superintendent (or Project Director). One of the functions of this team is to ensure that the planning and execution process, including scope management, is being complied with.
The STO construction audit team is entirely independent from the turnaround delivery and does not have direct responsibilities for the turnaround being reviewed. It is often desirable to include independent consultants hired directly by the steering committee from outside the plant or project organization for some, if not all, of the audits.17
3.3 APPLICABILITY CHALLENGES
A construction project is exposed to much more variability than the controlled work environment of an already completed/enclosed facility.
A construction project involves a larger number of contractors, with more complex and short-term relationships. The competitive bidding process further undermines the potential for improved efficiency with each iteration and training, as competitive bidding may mean that a less experienced contractor gets the job. On a shutdown project (which typically is not bid on a competitive basis) a premium is put on long-term relationships and proven performance. Obviously, differing site conditions, weather, and geographic distances also play a role. Instead of careful on-site modeling under the planners’ eyes, most construction activities for a new-build project are happening elsewhere, whether on-site or overseas.
The disconnect between the complexity of the project schedule and the capability of the delivery organization to maintain such a schedule and then coordinate the work requires a heightened focus on scope control. Finally, while unanticipated STO scope can sometimes be deferred and added to the “known/anticipated” scope of the next turnaround, unanticipated scope typically cannot be deferred for construction projects.
4. CONCLUSION
To fulfill the promise of an American nuclear power Renaissance, it is imperative to address construction management and planning technologies. More attention must be placed on the management systems required to implement “accelerated and well-controlled construction schedules.”18 In 1994, EPRI recommended a widespread simplification of all activities normally associated with nuclear power plant construction and operations. Scope simplification and control are at the core of power plant outage management.
In order to reduce construction project delays, more planners with outage experience should oversee new-build construction. However, accelerated scheduling requires tight scope control and the organizational capability to fulfill this mandate. In turn, scope control and operational efficiency require a paradigm shift towards a renewed focus on delivery efficiency, i.e., the transfer of lean shutdown practice to new-build construction.
At a minimum, these changes entail the formal recognition of “scope” as the third component of project controls and the incorporation of a scope management function into the projects’ organization matrix. This function should be directly controlled and audited by the project stakeholders and staffed with independent consultants. Functionally, this entity would be similar to an independent construction assurance and claims management group.
Benchmarking suggests that the U.S. nuclear power plant Renaissance will face substantial project delays and cost overruns. It is, therefore, essential to implement organizational processes that will prevent or mitigate delays and cost overruns, including outage scope management principals.
About the Author
Charles P. Fournier, J.D., CCA was a Managing Director with Long International. Mr. Fournier has over 15 years of experience in U.S. and international engineering and construction management and dispute resolution consulting, including construction contract dispute analysis, claims preparation, arbitration and litigation support, expert testimony, schedule control, commercial negotiation, risk assurance, construction audit, and contractual process engineering. He is a bilingual French-English business strategy and construction advisory professional with extensive experience leading teams that solve client problems involving dispute resolution, claims negotiation, and performance audits. Mr. Fournier focuses his practice on owners, engineering firms, and contractors in the petroleum refining, petrochemical, oil and gas, power/cogeneration, mineral processing, industrial, building, and infrastructure market sectors worldwide. For further information, please contact Long International’s corporate office at (303) 972-2443.
1 Edward Kee, “How Nuclear Projects Fail,” Nuclear Economics Consulting Group, October 8, 2014.
2 Charles P. Alexander, “Whoops! A $2 Billion Blunder: Washington Public Power Supply System,” Time, August 8, 1983, https://content.time.com/time/subscriber/article/0,33009,955183-1,00.html
3 John Douglas, “Reopening the Nuclear Option,” EPRI Journal, Vol. 19, No. 8, December 1994, http://eprijournal.com/wp-content/uploads/2016/01/1994-Journal-No.-8.pdf.
4 Douglas, “Reopening the Nuclear Option.”
5 Modularization of Equipment for New Nuclear Applications: Testing and Preservation, EPRI, May 10, 2010, https://www.epri.com/research/products/1021178.
6 The Economic Modeling Working Group of the Generation IV International Forum, Cost Estimating Guidelines for Generation IV Nuclear Energy Systems, Rev. 4.2, September 26, 2007, https://www.gen-4.org/gif/upload/docs/application/pdf/2013-09/emwg_guidelines.pdf.
7 Modularization of Equipment, EPRI.
8 Douglas, “Reopening the Nuclear Option.”
9 Charles Fournier, “Claims Management Challenges in the ‘Modularized’ Project Execution Environment,” Long International, March 2016.
10 The Generation IV International Forum, “Generation IV Systems,” https://www.gen-4.org/gif/jcms/c_59461/generation-iv-systems.
11 For example, eighteen American shipyards built 2,710 Liberty ships between 1941 and 1945, the largest number of ships produced to a single design. See Wikipedia, “Liberty ship,” https://en.wikipedia.org/wiki/Liberty_ship.
12 World Nuclear Association, Heavy Manufacturing of Power Plants, April 2016, http://www.world-nuclear.org/information-library/nuclear-fuel-cycle/nuclear-power-reactors/heavy-manufacturing-of-power-plants.aspx.
13 The Economic Modeling Working Group of the Generation IV International Forum, Cost Estimating Guidelines, p. 45.
14 Douglas, “Reopening the Nuclear Option.”
15 Japanese and South Korean nuclear projects are often cited as the most efficient (they provide most of the construction data benchmarked by EPRI). The nuclear industries in these two countries, however, have recently been plagued with allegations of fraudulent safety inspections and widespread compliance breaches with safety requirements during construction.
16 World Nuclear Industry Status Report 2014, p. 33.
17 Rod Olivier, “Complete Planning for Maintenance Turnarounds Will Ensure Success,” Oil and Gas Journal, April 28, 2002, http://www.ogj.com/articles/print/volume-100/issue-17/special-report/complete-planning-for-maintenance-turnarounds-will-ensure-success. See also, generally, Mohammad Raoufi and Aminah Robinson Fayek, “Process Improvement for Power Plant Turnaround Planning and Management,” International Journal of Architecture, Engineering and Construction, Vol. 3, No. 3, September 2014, pp. 168–181, http://journals.iasdm.org//index.php/ijaec/article/viewFile/265/248.pdf.
18 Douglas, “Reopening the Nuclear Option.”
Copyright © 2019 Long International, Inc.
ADDITIONAL RESOURCES
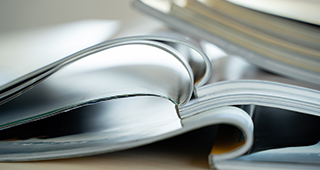
Articles
Articles by our engineering and construction claims experts cover topics ranging from acceleration to why claims occur.
MORE
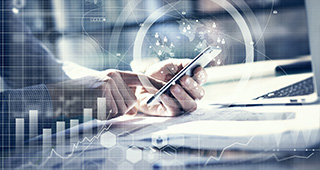
Blog
Discover industry insights on construction disputes and claims, project management, risk analysis, and more.
MORE
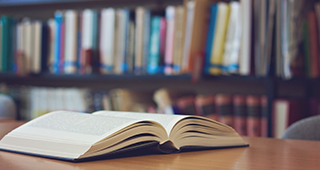
Publications
We are committed to sharing industry knowledge through publication of our books and presentations.
MORE