
Considerations for Successful Project Commissioning and Start-Up Planning and Execution
Successful commissioning and start-up phases are typically indicative of the future success of ongoing operations. Therefore, they require appropriate focus and resource allocation to ensure overall project success. This article offers a high-level overview of typical commissioning and start-up activities and their associated key considerations.
1. INTRODUCTION
Commissioning and start-up follow the construction phase of typical engineering, procurement, and construction (EPC) projects. During commissioning, newly installed equipment and systems are brought online, integrated, and tested against the design requirements (typically without the introduction of chemicals, in the case of chemical processing plants). In the subsequent start-up, chemicals are introduced, and the system is brought online to facilitate performance testing, followed by turnover to the permanent operations organization. The project commissioning and performance tests are designed to demonstrate that the installed system satisfies the design requirements and the performance test requirements as specified in the contract.
This article provides a high-level overview of what commissioning is in construction, the typical start-up activities, and their associated key considerations. The provision of complete, detailed descriptions of all commissioning and start-up activities for multiple project types and industries is beyond the scope of this article.
Many studies have shown that successful start-ups and subsequent operation of newly built systems have direct relationships to the quality of the commissioning work.1 It has been reported that the cost of starting up new chemical processing facilities can be as much as 8% to 12% of the capital project costs and that good start-up planning and execution can save 1% to 3% of the total project cost.2 However, industry benchmarking data indicate that commissioning and start-up efforts and performance often fall below expectations.3 Clearly, commissioning and start-up are critical project activities that require appropriate focus and resource allocation to ensure overall project success.
Project commissioning and start-up procedures comprise of several phases, as shown below in Figure 1, and as follows:4
- Pre-commissioning: typically performed by the contractor, includes de-energized verification and testing including flushing of piping and motor bumps to verify proper rotation direction;
- Commissioning: typically performed by the owner, includes energized testing of equipment and integrated systems, typically using air and/or water instead of actual process chemicals;
- Start-up: typically performed by the owner, includes integrated system start-up, addition of chemicals, and ramp up to steady state; and
- Performance testing: typically performed by the owner, includes execution of performance tests designed to demonstrate that performance of the fully integrated system satisfies all contract performance requirements.
Figure 1: Phases of a Typical EPC Project
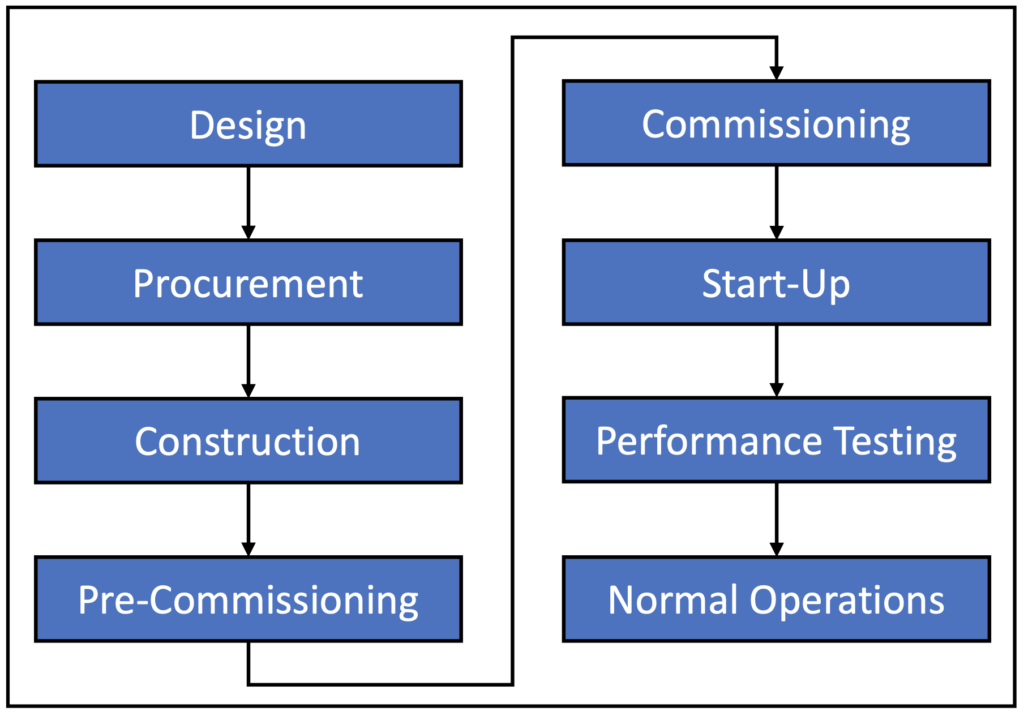
Although the entities that typically perform the various commissioning and start-up activities are listed above, in some cases the contractor may perform the commissioning and performance testing, or the owner may contract the services of an independent third-party commissioning consultant to perform these activities. Therefore, contract documents should clearly state the party responsible for executing each project phase to avoid ambiguity.
The definition of the mechanical completion milestone, at which point the construction organization hands over the system to the commissioning organization, can be project-specific, occurring either prior to5 or after6 the pre-commissioning phase. Therefore, contract documents should clearly define the criteria for achieving the mechanical completion milestone. The ready-for-start-up milestone is typically achieved upon successful completion of the commissioning phase (prior to the start-up phase).7
In some cases, depending on the specific industry and geographical location, there may be commissioning and start-up codes, specifications, and/or guidelines published by various governmental agencies and/or professional organizations that should be adhered to and comprehended in the commissioning and start-up planning and procedures.8 For example, ASME PTC 40-1991 provides performance test codes for flue gas desulfurization (FGD) units,9 the U.S. Department of Energy (DOE) provides guidelines for the commissioning of nuclear plants,10 and Jarløv11 and the U.S. Environmental Protection Agency (EPA)12 summarize general commissioning guidelines and requirements for buildings. Where applicable, parties should include reference to such documents in contract requirements. Further discussion of such industry and location-specific commissioning and start-up specifications is beyond the scope of this article.
The remainder of this article first discusses general considerations for commissioning and start-up planning in Section 2. The execution of the various commissioning and start-up phases in construction is then discussed in Section 3.
2. GENERAL CONSIDERATIONS
2.1 Responsible Parties
Responsibility for the various commissioning and start-up planning and execution tasks is generally project-dependent and can lie with any one of several potential organizations. The responsible organizations can include the EPC contractor’s commissioning team, the owner’s commissioning team, an owner engineer’s commissioning team, a third-party commissioning consultant contracted by the owner, the owner’s permanent operations and maintenance (O&M) team, or a combination of these organizations. Typically, the contractor’s commissioning team is expected to provide on-site support during activities for which the owner is responsible.13
To avoid ambiguity, ownership of project commissioning and start-up planning and execution tasks should be determined early on so that the EPC contract can clearly define contractor-responsible tasks and deliverables.14 Regardless of the organization(s) responsible for the planning and execution of the various activities, the commissioning organization will ultimately turn over the system to the owner’s permanent O&M organization for ongoing O&M, including asset and spares management.15 The turnover process typically includes provision of O&M manuals and training manuals, as well as training of the owner’s O&M personnel. Therefore, the owner’s O&M organization should ideally be involved in the execution of commissioning and start-up activities to facilitate appropriate training and develop expertise with the O&M of the new system.
2.2 Planning
Commissioning and start-up planning activities typically start early in a project and continue throughout various project phases to fully prepare the commissioning organization to take over ownership of system components at mechanical completion and proceed directly to the commissioning and start-up phases. These planning activities typically include:
- development of commissioning organizational charts and hiring of personnel, if required;16
- development of commissioning schedules including determination of the order in which various new equipment will be commissioned;17
- development of documentation including O&M manuals, training materials, and test plans and procedures;18 and
- procurement of necessary materials to support commissioning and start-up activities, including spares19 and chemicals.
Detailed discussions of the scheduling of these planning activities are available elsewhere and are outside the scope of this article.20
To facilitate detailed commissioning and start-up planning, the system should first be systemized.21 The system hierarchy should be defined from a systems engineering perspective, as in the example shown below in Figure 2, and clear delineations between various components, modules, and sub-systems should be shown on the P&IDs. This systemization allows for a bottoms-up approach to commissioning, where individual pieces of equipment are first commissioned at the component level and then integrated together and commissioned at higher and higher levels of the hierarchy to ultimately facilitate commissioning and start-up of the facility at the system level. If a project was specified and/or designed based on systems engineering principles, this hierarchy may be similar to the work breakdown structure (WBS) for the project.
Figure 2: Typical System Hierarchy
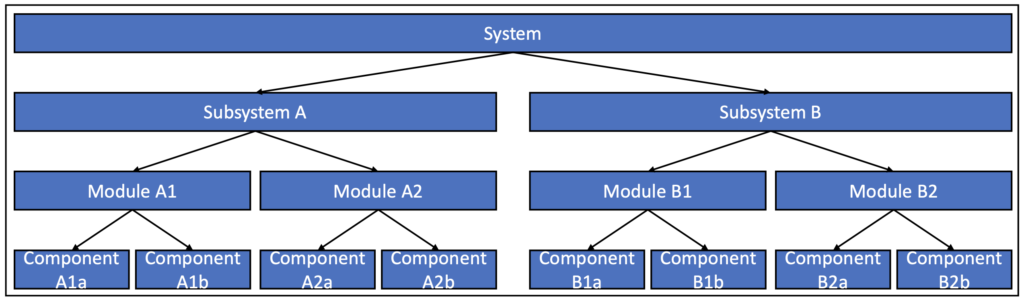
Once systemization is complete, the order of commissioning priority for the various components, modules, and subsystems can be determined. Typically, utilities such as power, water, and compressed air, and other global modules, such as control systems, wet laboratories, and reagent delivery systems, are commissioned first because they need to be available to facilitate the commissioning and start-up of the primary processing equipment.22 The commissioning prioritization sequence should be defined early enough in a project so that it can be reflected in the turn-over prioritization shown in the construction schedule.23
The documentation deliverables should be completed early enough in a project to allow for owner review and/or approval before they are required for execution of commissioning and start-up activities and/or subsequent ongoing operations. These deliverables typically include but are not limited to:24
- the O&M manual, which should include all safety considerations and requirements such as the result of process hazard reviews, material safety data sheets (MSDS), definition of lock-out/tag-out (LOTO) points and confined spaces as well as standard operating procedures (SOPs) for nominal and off-nominal operation;
- the process control narrative;
- all required O&M training documents; and
- procedures for tests and special operations to be performed during pre-commissioning, commissioning, start-up, and performance testing activities.
All testing and operational procedures should include detailed step-by-step instructions and should reference P&ID tags for specific equipment, instrumentation, and controllers to remove any possibility of ambiguity. Additionally, the documentation should encompass all modes of operation. All operational modes as well as the transition between the various operational modes should be fully tested during commissioning and start-up.
3. SITE EXECUTION
This section discusses execution of the various activities in each of the commissioning and start-up project phases: pre-commissioning, commissioning, start-up, and performance testing. In addition to descriptions of the activities typically performed during each of the phases, insights into general best practices are provided based on the author’s experience.
3.1 General Execution Considerations
Throughout the commissioning and start-up phases of a project, safety should be of the utmost importance. This is especially true if the system being brought online contains new technology, if the owner’s O&M organization does not have prior experience operating and maintaining a similar system, and/or if the installation is at a greenfield site where established safety protocols do not exist prior to the execution of the project.
As such, system documentation, including O&M manuals, training documentation, and commissioning and start-up procedures and checklists, should contain all relevant safety information including responses to off-nominal operation. All personnel performing commissioning and start-up activities should be fully trained in the safety aspects of the new system. Operations personnel should be trained with regards to chemical safety as well as in the potential for, and response to, off-nominal conditions such as over-pressurization and vessel overflows. Maintenance personnel should be trained in chemical safety as well as standard maintenance-related safety programs including lock‑out/tag-out (LOTO) and confined space entry.
Documentation is also critical throughout the commissioning and start-up activities. Commissioning and start-up test procedures should contain detailed, step-by-step instructions in checklist format to provide a record of the tests, tasks performed, and any corrective actions taken. The test procedures should also clearly detail unambiguous success criteria for the various commissioning and performance tests. Process data should be preserved either in the plant historian (for data gathered by online instrumentation) or on standardized data sheets and/or test reports (for data gathered offline, for example, laboratory results or the results of third-party testing). In addition to preserving a historical record of the satisfaction of contractual performance requirements, the commissioning and start-up data will serve as the baseline for comparison of future operations for the life of the system.25
Finally, all materials required for the commissioning and start-up activities should be procured and available prior to when they are needed. These materials may include but are not limited to:26
- general commissioning consumables,
- spare parts,
- chemical reagents,
- catalysts and other process media,
- laboratory chemicals and supplies,
- lubricants, and
- calibration tools and gases.
The contract and/or commissioning documentation should fully define the procurement specifications for these materials as well as the organization responsible for their procurement, and there should be no deviations from these specifications during the commissioning and start-up activities unless all parties mutually agree upon those deviations in advance.
3.2 Pre-Commissioning
Pre-commissioning is performed after the completion of construction/installation of a newly installed system component and consists of de-energized verification and testing of the component, prior to the introduction of any processing chemicals.27 Examples of activities typically performed during the pre-commissioning phase include:28
- verification of installation vs. the P&IDs and other design documents;
- verification of safety device installation such as guards and interlocks;
- vendor and factory acceptance testing;
- vessel cleaning;
- line flushing, cleaning, and/or blowing;
- initial leak testing;
- rotating equipment alignment checks;
- rotating equipment motor bumps to verify rotation direction;
- electrical loop testing;
- first fill of lubricants and utility fluids;
- loading of catalysts, dessicants, and other fluids; and
- any other required checks or tests prior to the energization of the component.
Upon completion of pre-commissioning of a given system component, that component is now ready for commissioning.
3.3 Commissioning
Commissioning is performed after a given component has been pre-commissioned and consists of the first energized tests of the equipment. Commissioning is typically performed with safe chemicals (water, nitrogen, and/or air), which is known as “cold testing.” Once individual components have been commissioned, they are integrated together to facilitate the commissioning of modules, subsystems, and finally the entire system, as shown above in Figure 2. Examples of activities typically performed during the commissioning phase include:29
- energization of equipment,
- instrumentation calibration,
- introduction of safe chemicals,
- final leak checking,
- fluid circulation,
- checkout of PLC and emergency shutdown systems,
- testing of all safety functions,
- testing of all controller functions, and
- vendor commissioning of large and/or skid-mounted equipment.
Commissioning tests should be designed to encompass all possible modes of operation, including mode-switching between the various operational modes. Commissioning procedures should include response procedures and/or checklists for off-nominal and alarm conditions so that the commissioning team can make adjustments and corrections when off-nominal operation is encountered. Commissioning procedures should also clearly state the success criteria for the various commissioning tests, including what tests must be successfully completed prior to commencing higher-level integrated tests at the module, subsystem, and system levels.
It is important to build confidence in instrumentation measurements and data logging since these readings will be relied upon during subsequent system start-up and performance testing. Therefore, instrument calibration should be independently verified wherever possible, such as the use of tank level measurements to calculate flow rates for comparison to flow meter measurements and the performance of “catch and weigh”30 tests to verify flow rates for chemical dosing equipment.
If applicable, on-site vendor commissioning, as specified in the purchase order, should be scheduled in advance so that the vendor is on-site when required and the equipment is available and ready to be commissioned by the vendor. Any support equipment and/or systems required for vendor commissioning should already have been commissioned so that they are ready to support the vendor commissioning.
All data should be logged, and all completed test plans and checklists should be preserved. Test results should be summarized in test reports as per contract requirements for review and/or approval by the owner.
Commissioning and start-up difficulties such as equipment failure and performance issues can occur, and these issues should be addressed and resolved as they arise to facilitate successful completion of the commissioning and start-up tests. Mr. Amin Almasi discusses typical problems that may be uncovered during the commissioning and start-up phases.31 Further discussion of these issues is beyond the scope of this article.
Upon successful commissioning of the various components, modules, subsystems, and system, the system is ready for start-up (RFSU).
3.4 Start-Up
The start-up phase is typically where processing chemicals are first introduced, and the system is ramped up to steady state operation.
This is a critical project phase that can require significant personnel resources, as system operation and performance are dynamic and may require corrections, including manual operation and engineering intervention. System shake-out and optimization activities may also occur during this period to prepare the system for subsequent performance testing. Given the 24×7 continuous operational nature of most systems, the night shift should be appropriately staffed with engineering support to facilitate decision making during non-normal work hours in the event that significantly off-nominal operations are encountered or discrepant data requires detailed analysis and operational response.
The start-up procedures should specify valve positions for start-up prior to introducing chemicals and process flows and should include step-by-step instructions for introducing processing chemicals and ramping the system to steady state production. The procedures should also include detailed sampling instructions, including the frequency of collection, for chemical samples for offline analysis, if required. Depending on the system, it may take several days or more to reach steady state operations. During this inherently dynamic operational period, the use of a process model to predict expected values for key operational parameters as a function of time is useful for assessing system performance as well as for the validation of said process models.
If offline laboratory measurements are required, it is critical that the lab be properly staffed at all times. To avoid discrepant data during this critical phase of operations, it is imperative that all operations personnel are properly trained in taking samples and that all lab technicians are properly trained in analyzing the samples and resulting data. Standardized data sheets should be used to record raw data and the results of any data analysis, and the data should be stored for future reference. The inventory of lab supplies should be monitored closely, and the setting of re-order points should account for the likelihood of engineering requests for many more lab samples and tests during the start-up period than are typically required for nominal operations.
Once the system has successfully been brought to steady state operation, it is ready for performance testing.
3.5 Performance Testing
The final project phase is performance testing. During performance testing, the system is operated as per the performance test plan to demonstrate that system performance satisfies all performance requirements as specified in the contract documents.
Performance test success criteria are typically tied to performance goals such as system effectiveness, production rates, and/or product quality to demonstrate that the system operates as was intended and as was specified in the contract requirements. In some cases, performance goals may also demonstrate compliance with governmental regulations, such as in the case of air quality control (AQC) systems. Additional success criteria are also typically tied to other performance goals such as power usage, reagent usage, and spares usage to demonstrate that operating cost goals have been met. Finally, performance testing also typically verifies system availability and/or reliability over an extended period of time, typically 30 days or more.
The performance test plan should clearly define the purpose of the tests and should include step-by-step instructions for completion of the required tests. The test plan may include testing of the system across a wide range of operating conditions and system loads, as defined in the contract requirements. It is imperative that the test plans clearly define the parameters to be monitored, data and samples to be collected, any required laboratory analysis, any required data analysis and calculations, and the associated success criteria. All parties should mutually agree to the performance test plan prior to commencement of the testing.
Like the start-up testing discussed above in Section 3.4, performance testing typically requires 24×7 system operation. Therefore, night shift operations should be appropriately staffed with engineering support to facilitate decision making during non-normal work hours in the event that significantly off-nominal operations are encountered or discrepant data requires detailed analysis and operational response. All required supplies and materials should be readily available to avoid any unnecessary interruptions to the performance testing.
All performance test data should be logged and saved, and all completed procedures and checklists should be preserved. The performance test results should be summarized in a test report as per contract requirements for review and/or approval by the owner. Lessons learned during the commissioning and start-up of the system should be documented for future reference.
Upon successful completion of the performance test and approval of the final performance test report, the project is ready for close-out and the system is handed over to the owner’s permanent O&M organization for ongoing operations.
4. SUMMARY
In summary, the commissioning and start-up phases of a typical EPC project include pre-commissioning, commissioning, start-up, and performance testing. To avoid conflict, a contract should clearly state which parties are responsible for the various associated activities. Documentation during these stages of a project is critical: procedures and success criteria should be fully defined and unambiguous, and data and analysis results should be archived for future reference. Successful commissioning and start-up phases are typically indicative of the future success of ongoing operations. Therefore, the commissioning and start-up activities require appropriate focus and resource allocation to ensure overall project success.
About the Author
Eric J. Klein, Ph.D., P.E., PMP, is a Vice President of Long International. He has over 20 years of industrial experience as a Technical Leader, Project Manager, and Consultant in engineering, procurement, and construction (EPC), manufacturing, and research and development (R&D) environments. Dr. Klein is skilled in corporate leadership and has significant experience leading cross-functional teams to design, build, commission, start up, and test chemical processing systems in the power generation and semiconductor manufacturing industries. He possesses project management experience for multimillion‑dollar capital projects including earned value management, risk management, contract and scope of work negotiation, technical project proposals, cost estimating, change control, requests for information (RFI), change order management, design management, and equipment procurement oversight. He has experience reviewing drawing packages and performing quantum cost analysis for LNG projects. Prior to joining Long International, Dr. Klein held the positions of Chief Technology Officer, Vice President of Chemical Systems, Director of Chemical and Process Engineering, Staff Technologist, and Senior Process Engineer. Dr. Klein is based in Castle Rock, Colorado, and can be contacted at eklein@long-intl.com and (720) 982-3813.
1 Killcross, Martin (2012). Chemical and Process Plant Commissioning Handbook: A Practical Guide to Plant System and Equipment Installation and Commissioning, Elsevier Ltd., p. 17.
2 Sheridan, Mark (2015). “Managing Large Chemical Plant Startups,” Chemical Engineering, 122(5), p. 50.
3 Construction Industry Institute (2015). Achieving Success in the Commissioning and Startup of Capital Projects: Implementing Critical Success Factors (Implementation Resource 312-2, Volume 1), p. 3.
4 Id. at pp. 8–11 and Somerville, Nathan (2020). “What is Plant Commissioning, Exactly?,” Industry Week. See https://www.industryweek.com/operations/article/21125193/what-is-plant-commissioning-exactly.
5 Almasi, Amin (2018). “Processing Plant Commissioning Considerations,” Processing Magazine. See https://www.processingmagazine.com/home/article/15587340/processing-plant-commissioning-considerations; Killcross, Martin (2012). Chemical and Process Plant Commissioning Handbook: A Practical Guide to Plant System and Equipment Installation and Commissioning, Elsevier Ltd., p. 204; and Construction Industry Institute (2015). Achieving Success in the Commissioning and Startup of Capital Projects: Implementing Critical Success Factors (Implementation Resource 312-2, Volume 1), p. 10.
6 International Electrotechnical Commission (2006). Commissioning of Electrical, Instrumentation and Control Systems in the Process Industry – Specific Phases and Milestones (Standard IEC-62337), p. 6 and The Project Definition (2015). M/C (Mechanical Completion). See https://www.theprojectdefinition.com/m-c-mechanical-completion/.
7 The Project Definition (2015). RFSU (Ready for Start-up). See https://www.theprojectdefinition.com/rfsu-ready-for-start-up/.
8 One comprehensive source for determining the existence of such specifications is the American National Standard Institute website, ansi.org.
9 The American Society of Mechanical Engineers (1991). Flue Gas Desulfurization Units: Performance Test Codes (ASME PTC 40-1991).
10 U.S. Department of Energy, Office of the Chief of Nuclear Safety and Office of Environmental Management (2017). Design and Commissioning Report, Revision 1.
11 Jarløv, Thomas Toftgaard (2021). A Practical Guide to the Commissioning Process, Forlaget TTJ.
12 U.S. Environmental Protection Agency (2007). General Commissioning Requirements Section 01 91 00.
13 Somerville, Nathan (2020). “What is Plant Commissioning, Exactly?,” Industry Week. See https://www.industryweek.com/operations/article/21125193/what-is-plant-commissioning-exactly.
14 Killcross, Martin (2012). Chemical and Process Plant Commissioning Handbook: A Practical Guide to Plant System and Equipment Installation and Commissioning, Elsevier Ltd., p. 53 and Sheridan, Mark (2015). Managing Large Chemical Plant Startups, Chemical Engineering, 122(5), pp. 52–54.
15 Killcross, Martin (2012). Chemical and Process Plant Commissioning Handbook: A Practical Guide to Plant System and Equipment Installation and Commissioning, Elsevier Ltd., p. 210.
16 Id. at pp. 90–102.
17 Id. at pp. 65–73.
18 Sheridan, Mark (2015). “Managing Large Chemical Plant Startups,” Chemical Engineering, 122(5), pp. 53–55.
19 Almasi, Amin (2018). “Processing Plant Commissioning Considerations,” Processing Magazine. See https://www.processingmagazine.com/home/article/15587340/processing-plant-commissioning-considerations and Killcross, Martin (2012). Chemical and Process Plant Commissioning Handbook: A Practical Guide to Plant System and Equipment Installation and Commissioning, Elsevier Ltd., pp. 113–114.
20 Killcross, Martin (2012). Chemical and Process Plant Commissioning Handbook: A Practical Guide to Plant System and Equipment Installation and Commissioning, Elsevier Ltd.; Almasi, Amin (2018). “Processing Plant Commissioning Considerations,” Processing Magazine. See https://www.processingmagazine.com/home/article/15587340/processing-plant-commissioning-considerations; Sheridan, Mark (2015). “Managing Large Chemical Plant Startups,” Chemical Engineering, 122(5), pp. 50–58; and Construction Industry Institute (2015). Achieving Success in the Commissioning and Startup of Capital Projects: Implementing Critical Success Factors (Implementation Resource 312-2, Volume 1), pp. 15–17.
21 Killcross, Martin (2012). Chemical and Process Plant Commissioning Handbook: A Practical Guide to Plant System and Equipment Installation and Commissioning, Elsevier Ltd., pp. 65–73.
22 Ibid.
23 Ibid.
24 For a detailed discussion on documentation requirements, see Long International’s article by S. Andrew McIntosh (2017) “The Importance of Project Handover Documentation.”
25 Henzel, D.S. et. al. (1981). Limestone FGD Scrubbers: Users Handbook (EPA-600/8-81-017), §5, pp. 5–13.
26 Killcross, Martin (2012). Chemical and Process Plant Commissioning Handbook: A Practical Guide to Plant System and Equipment Installation and Commissioning, Elsevier Ltd., pp. 110–114.
27 Construction Industry Institute (2015). Achieving Success in the Commissioning and Startup of Capital Projects: Implementing Critical Success Factors (Implementation Resource 312-2, Volume 1), p. 8.
28 Killcross, Martin (2012). Chemical and Process Plant Commissioning Handbook: A Practical Guide to Plant System and Equipment Installation and Commissioning, Elsevier Ltd., p. 16 and Construction Industry Institute (2015). Achieving Success in the Commissioning and Startup of Capital Projects: Implementing Critical Success Factors (Implementation Resource 312-2, Volume 1), pp. 8–9.
29 Construction Industry Institute (2015). Achieving Success in the Commissioning and Startup of Capital Projects: Implementing Critical Success Factors (Implementation Resource 312-2, Volume 1), pp. 8–9.
30 In a catch and weigh test, fluid flow is diverted and captured in an external container and the amount of captured fluid is measured as a function of time to determine the volumetric or mass flow rate of the fluid stream.
31 Almasi, Amin (2018). “Processing Plant Commissioning Considerations,” Processing Magazine. See https://www.processingmagazine.com/home/article/15587340/processing-plant-commissioning-considerations.
Copyright © Long International, Inc.
ADDITIONAL RESOURCES
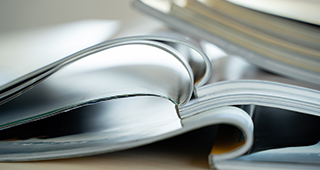
Articles
Articles by our engineering and construction claims experts cover topics ranging from acceleration to why claims occur.
MORE
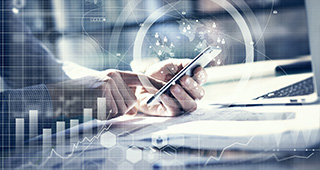
Blog
Discover industry insights on construction disputes and claims, project management, risk analysis, and more.
MORE
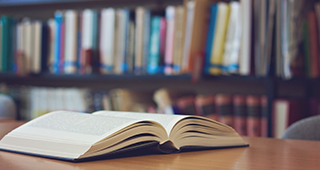
Publications
We are committed to sharing industry knowledge through publication of our books and presentations.
MORE