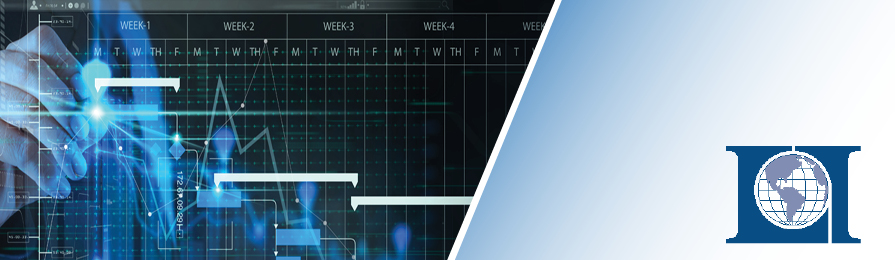
Delay Damages in Construction
This article summarizes what delay damages are, their types, and how they translate to compensable and non-compensable costs.
1. INTRODUCTION
Construction contracts between owners and contractors typically state what actions should be taken if a project experiences delay. Depending on who is responsible for the delay, an owner or contractor may be entitled to delay damages, and a contractor may be entitled to a time extension. Construction contracts typically include a clause or clauses for delay damages, including (1) liquidated damages (LDs); (2) actual delay damages;1 and (3) consequential damages. This article discusses types of delay that may lead to damages, the three types of damages, and methods for calculating costs related to these damages.
2. PROJECT DELAY CONSIDERATIONS
When a delay analyst assesses a delay’s impact on project cost and schedule, the first step is often to determine whether the delay is critical or non-critical. If the delay event affects activities on what was the project critical path2 at the time that the delay occurred, the event will delay project completion unless delay mitigation occurs. A critical delay caused by an owner-responsible event may entitle a contractor to a time extension and delay damages. If the delay is non-critical, meaning the delayed work is not part of the critical path, then in most cases, the contractor cannot recover increased time-related costs.3 A critical, force majeure delay may entitle the contractor to a time extension, but not delay damages, unless the contract terms and conditions state that such damages are compensable.
If the objective of the delay analysis is to assess all delays during a window of time or the entire project duration, then a comparative analysis of planned and actual activity start dates and durations may be the appropriate first step before determining criticality. If the analysis is being performed on each monthly schedule update, then the analyst compares activity start dates and durations at the beginning of the month to the activity start dates and durations at the end of the month and quantifies the delays. This initial analysis also includes quantifying extended lag durations.
In order to determine delay criticality properly, the analyst must first examine the quality of the schedule to ensure that the schedule contains no open ends (missing predecessors or successors) and that noncontractual mandatory constraints do not drive the schedule. Open-ended activities should be linked, and inappropriate mandatory constraints should be changed.4
After remedying schedule logic and inappropriate mandatory constraints, the analyst identifies critical path delays either on a prospective basis, such as when using a time impact analysis,5 or on an as-built basis6 when using other modeled schedule analysis methodologies such as an as-built but-for schedule delay analysis method7 or an observational method using an as-planned vs. as-built comparison.8
If the analyst determines a delay to be critical, the next step is to determine if the delay is excusable or non-excusable. The causes of a contractor’s excusable delays are beyond the contractor’s control. If an act of God (e.g., extremely unusual weather) or other force majeure events cause an excusable, critical delay, the contractor may be entitled to a time extension, but usually not its delay costs. If an owner-responsible event causes an excusable, critical delay, then the contractor may be entitled to a time extension. If there is no “No Damages for Delay” clause, and the contractor has not caused concurrent delay, the contractor may also be entitled to delay damages.
Non-excusable delays are generally within the contractor’s control and include poor quality of work requiring rework, lower-than-planned labor productivity that is not caused by the contractor’s underestimate of planned productivity or owner-responsible events, problems with construction equipment, or other events directly tied to the contractor’s responsibility and performance. If contractor-caused, non-excusable delay is critical, the owner may be entitled to LDs or actual delay damages if the contractor does not take action to make up the lost time.
AACE International provides general rules related to excusable and compensable delay:
Excusability exists where there is contractual or equitable justification in a claimant’s request for a contract time extension for relief from potential claims for liquidated/stipulated or actual delay damages. The showing of excusability does not necessarily mean that the claimant is also entitled to compensation for the delay. Conversely, delay is non-excusable when such justification does not exist.
Compensability or compensable delay exists where the claimant is entitled to recover not only a time extension but compensation for expenses associated with the extension of completion date or the prolongation of the duration of the work. Excusability is a prerequisite to compensability. Therefore, where compensability can be established, excusability is assumed.9
Before determining whether a contractor or owner can recover delay damages, the analyst should determine if the delay event is concurrent with any other project delays. A concurrent delay occurs when two or more individual delay events, one caused by the owner and the other caused by the contractor, occur during the same timeframe, and both events would delay the project completion date. A core principle from the Society of Construction Law states:
Where Employer Delay to Completion and Contractor Delay to Completion are concurrent and, as a result of that delay the Contractor incurs additional costs, then the Contractor should only recover compensation if it is able to separate the additional costs caused by the Employer Delay from those caused by the Contractor Delay. If it would have incurred the additional costs in any event as a result of Contractor Delay, the Contractor will not be entitled to recover those additional costs.10
Thus, neither the owner nor the contractor may be able to recover its delay damages for concurrent delay, although the contractor may still be entitled to a time extension.11
If the contractor does not complete work on time, the owner may be entitled to liquidated damages per day of delay. Similarly, a contractor may be entitled to LDs if its subcontractor delays the project, provided that the contract between the contractor and subcontractor includes LD terms. Parties typically establish the value of LDs and how they are to be applied during the contracting phase, before work begins.
The owner and/or the contractor may incur “actual” delay damages, but an owner may not be entitled to its actual delay damages if the contract contains an LD clause. Actual delay damages can be calculated and tabulated by different methods, which are discussed in Section 4.1.2 of this article.
“Consequential” damages, which are typically separate from delay damages, occur if one of the contracting parties breaches the contract. Construction contracts typically include waivers for consequential damages, and therefore, this article does not discuss in detail delay damages related to consequential damages.
3. DETERMINING ENTITLEMENT TO DELAY DAMAGES
After determining criticality and concurrency, the analyst should evaluate a delay and any concurrent delays for causation and potential compensability. The analyst determines whether the delay is excusable or non-excusable, and, if it is excusable, whether it is compensable to the contractor for its entire duration or only part, due to a concurrent, contractor-caused delay.
3.1 NON-CRITICAL DELAY
Non-critical delays may be excusable to the contractor if they cause its labor, equipment, or subcontractors to work longer than it reasonably planned. If an owner causes a non-critical delay, then delay to non-critical work activities may be compensable. In these cases, the contractor must prove that others (i.e., owner, other owner-responsible contractors, etc.) caused its actual damages, and that it calculated its damages based on the costs specifically incurred for the non-critical work and not time-related costs associated with the completion of the overall project. Delay costs would include such things as the costs of indirect labor, overhead, and equipment working on the affected non-critical activity, but not for the entire project. In these situations, contractors should seek recovery via contract change orders for non-critical, unplanned delay caused by others. Figure 3-1 below shows a five-day, owner-caused delay to a contractor’s non-critical Activity C.
Figure 3-1: Non-Critical, Owner-Caused Delays12
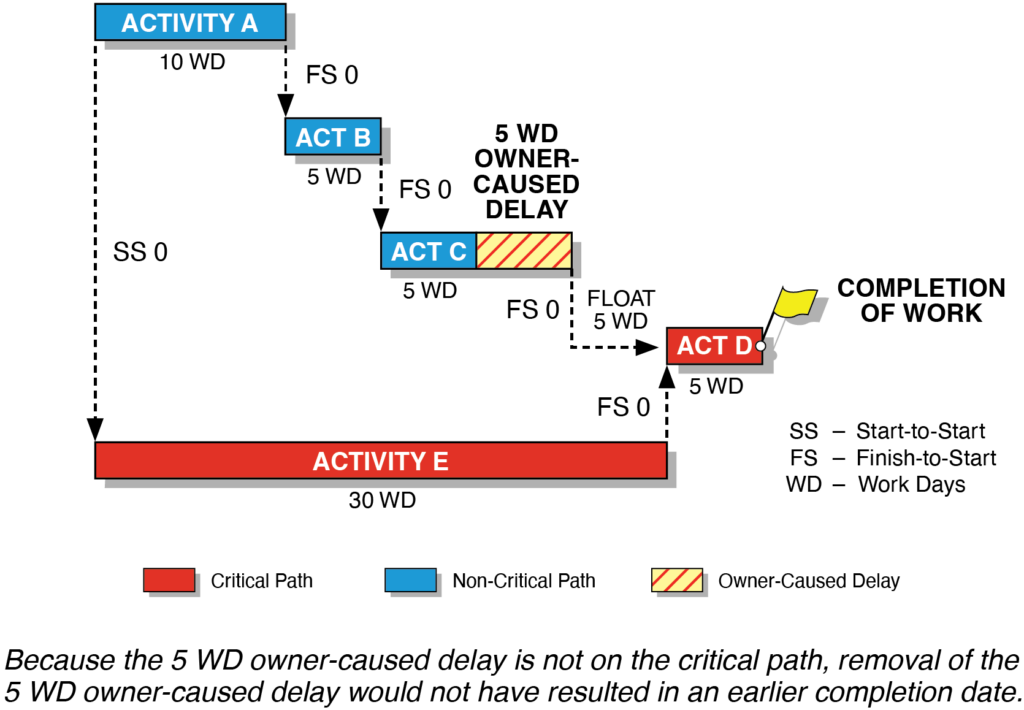
The figure above shows that although the owner-caused delay to the contractor’s Activity C does not affect the start of the contractor’s Activity D and therefore delay completion of work, the delay may have caused unforeseen delay costs to the work on Activity C. This owner-caused, excusable delay and any associated delay costs may be compensable if the contractor can prove that its unplanned costs were a direct result of the owner-caused delay.
3.2 CRITICAL DELAY
A critical delay to a project activity or set of activities affects the overall project completion date, as shown in Figure 3-2 below.
Figure 3 2: Critical Path Delay
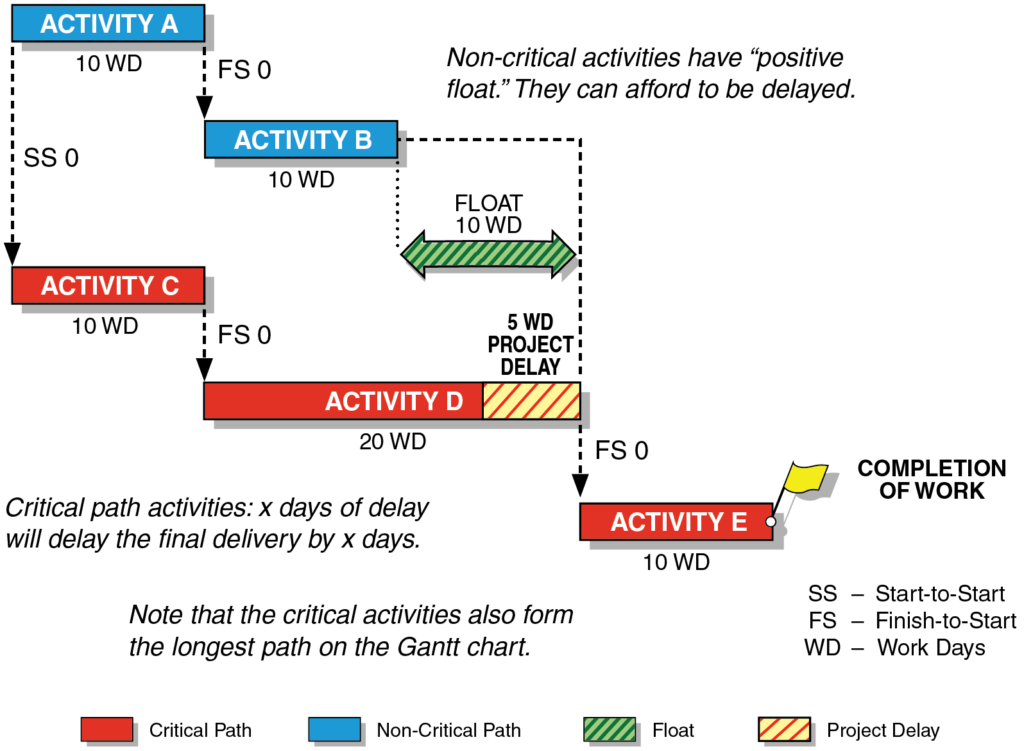
The analyst should determine whether the delay is excusable or non-excusable by performing a causation analysis. An excusable delay may entitle the contractor to additional compensation as delay damages. Conversely, a non-excusable delay may entitle the owner to LDs or actual delay damages, unless the contractor later mitigates and recovers the delay.
3.2.1 Critical, Excusable Delay
Excusable delay may be compensable or non-compensable, depending on causation. Construction contracts often contain force majeure clause(s) to remove contractor delay liability for unforeseeable and unavoidable events outside of the contractor’s control. Below are examples of force majeure events that may excuse the contractor from late completion of the work.
- Acts of God (severe weather conditions)
- Natural disasters (fire, flood, earthquake, etc.)
- War, invasion, terrorist threats, and civil unrest
- Labor disputes
- Government order or law
- Epidemic, pandemic, or similar (COVID-19)
- Other similar events beyond the contractor’s control
If a force majeure event causes a delay, the contractor is typically entitled to a time extension but not compensation. If the owner causes the critical delay, the delay is excusable and potentially compensable, absent a “No Damages for Delay” clause. Below are examples of owner-caused delay:
- Suspension of work
- Scope of work changes
- Design changes
- Approval delays
- Site access delays
- Late receipt of owner-acquired permits
- Differing site conditions
- Constructive changes
- Late owner-furnished equipment
- Errors and omissions (owner-provided engineering)
- Other owner-caused delays
3.2.2 Critical, Non-Excusable Delay
When a delay is determined to be critical but non-excusable, the contractor cannot recover delay damages. However, if the contractor and/or the contractor’s subcontractors are the sole cause of a delay, the owner may be entitled to LDs or actual damages unless the contractor later mitigates and recovers the delay.
Furthermore, if the contractor materially breaches the contract, the owner may also be entitled to consequential damages, unless the contract excludes such damages. It is important to distinguish between consequential damages and actual (direct) damages. Consequential damages are typically unexpected losses that arise from the breach of a contract and are not actual or direct delay damages.
3.3 CONCURRENT DELAY
AACE International addresses concurrent delay in the following ways:
- Two or more delays that take place or overlap during the same period, either of which occurring alone would have affected the ultimate completion date. In practice, it can be difficult to apportion damages when the concurrent delays are due to the owner and contractor respectively.
- Concurrent delays occur when there are two or more independent causes of delay during the same time period. The “same” time period from which concurrency is measured, however, is not always literally within the exact period of time. For delays to be considered concurrent, most courts do not require that the period of concurrent delay precisely match. The period of “concurrency” of the delays can be related by circumstances, even though the circumstances may not have occurred during exactly the same time period.
- True concurrent delay is the occurrence of two or more delay events at the same time, one an employer risk event, the other a contractor risk event and the effects of which are felt at the same time. The term ‘concurrent delay’ is often used to describe the situation where two or more delay events arise at different times, but the effects of them are felt (in whole or in part) at the same time. To avoid confusion, this is more correctly termed the ‘concurrent effect’ of sequential delay events.
- Concurrent delay occurs when both the owner and contractor delay the project or when either party delays the project during an excusable but non-compensable delay (e.g., abnormal weather). The delays need not occur simultaneously but can be on two parallel critical path chains.
- The condition where another delay-activity independent of the subject delay is affecting the ultimate completion of the chain of activities. (June 2007)13
Figure 3-3 below illustrates an example of concurrent delay.
Figure 3-3: Illustration of Concurrent Delay14
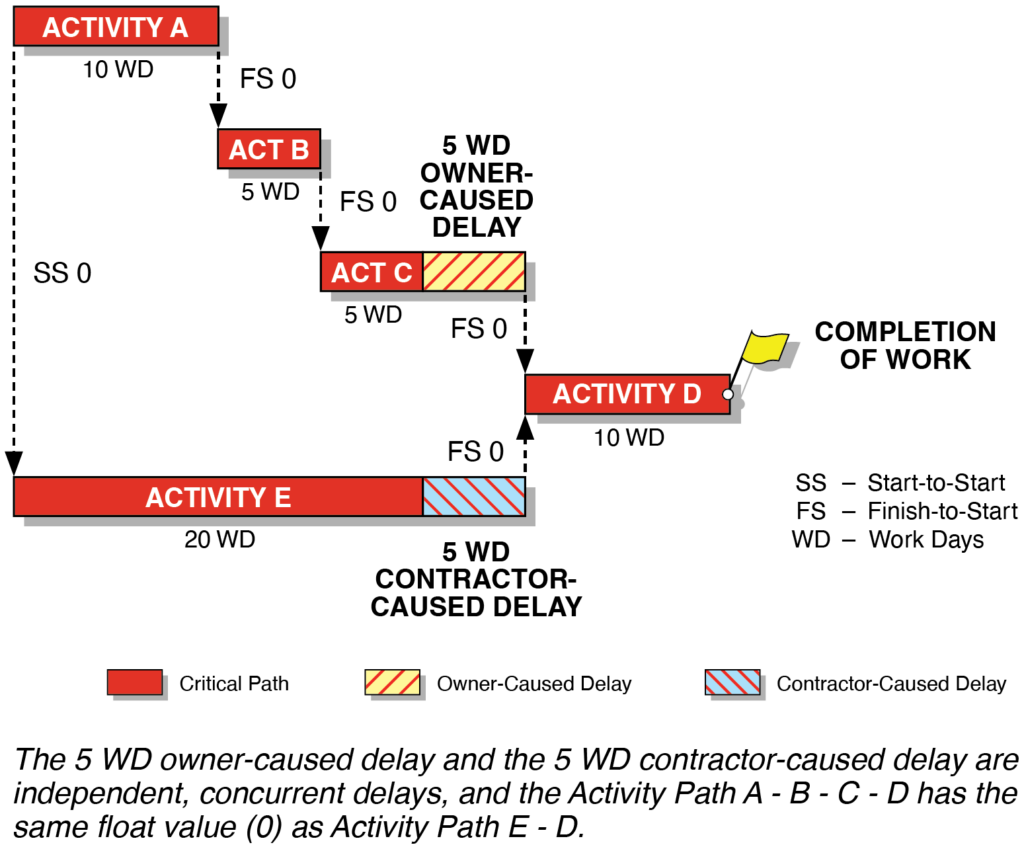
Figure 3-3 shows that the owner delayed Activity C by five working days, and during the same time period, the contractor delayed Activity E by five working days. Because both delays occurred within the same time period,15 they are concurrent delays. The owner-caused delay may be deemed excusable but not compensable because it did not solely delay the project completion date.
3.4 SUMMARY OF TYPES OF CONSTRUCTION DELAY
Each of the types of delay described above can be summarized as 1) delays within the contractor’s control, 2) delays within the owner’s control, and 3) delays caused by neither party. The tables below represent the types of delay that may result in delay damages.
Table 3-1: Types of Delay for a Single Delay Event

Table 3-2: Types of Delay for Concurrent Delay16
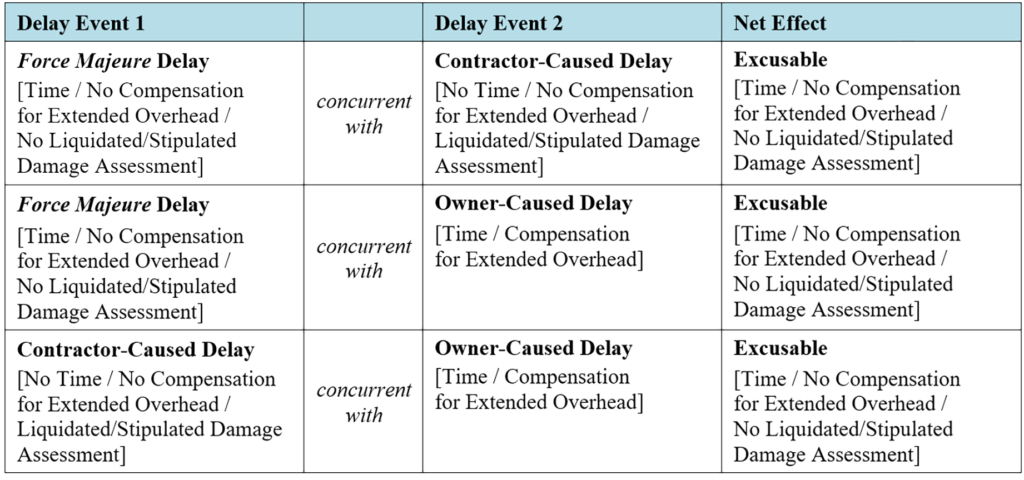
4. DELAY DAMAGES
This section discusses types of delay damages and methods for calculating expenses resulting from a compensable delay event.
4.1 TYPES OF DELAY DAMAGES
As previously discussed, delay damages may be categorized as: (1) liquidated damages (LDs), (2) actual/direct delay damages, and (3) consequential damages.
4.1.1 Liquidated Damages
Parties most often establish LDs in contracts prior to signing. LDs offset the costs an owner would incur for contractor-caused delay to project completion. A contractor can similarly claim LDs included in a subcontract when the subcontractor fails to complete its work on time. LDs are typically a dollar value per unit of time (e.g., $50,000 per day) and must reasonably represent the actual costs that an owner would incur. They are typically used in lieu of determining actual delay damages and are not intended to “punish” the contractor.
The American Bar Association provides this definition of liquidated damages:
In general, liquidated damages provisions specify a predetermined amount of money that must be paid as damages if one party fails to meet certain contractual requirements. In construction contracts, this typically manifests as a fee per unit of time (the “Liquidated Amount”) in the event of a missed schedule milestone such as Substantial Completion.17
4.1.2 Actual Delay Damages
Actual delay damages, also referred to as direct delay damages, may be associated with and result from a project delay event. If the contract does not include language to address delay damages, the contractor may still be liable for actual delay damages that the owner incurs.
As an example, an owner and a contractor enter into a construction contract that does not definitively set out delay damages. The contractor fails to execute and complete the work per the contractual completion date. Because project completion is delayed, the owner may incur delay costs, such as extension of the services of its project management personnel, consultants, engineers, site offices, administrative personnel, etc. Conversely, if the owner causes the delay, costs directly associated with the delay may be compensable to the contractor if it can demonstrate that the delay impacted what was the project critical path at the time that the delay occurred and provide support for its delay costs.
Many delay-related cost components can comprise the contractor’s actual delay damages. Below is a list of the more common cost components used to determine these damages.
- Extended field office overhead
- Field office facilities
- Field office staff salaries
- Field office staff vehicles
- Field office utilities
- Field office consumables
- Miscellaneous field office costs
- Unabsorbed home office overhead
- Home office rental or ownership costs
- Home office utilities
- Home office equipment and maintenance costs
- Corporate taxes
- Insurance costs not assigned to projects
- Home office staff salaries
- Idle direct labor costs
- Idle and/or extended construction equipment
- Contractor-supplied temporary utilities
- Equipment preservation
- Additional material storage
- Escalation
4.1.3 Consequential Damages
Consequential damages, also known as special damages or indirect damages, are not always directly caused by a breach of contract. The non-breaching party of the contract may seek these types of damages for losses that result indirectly from the breach.
Examples of consequential damages are listed below:
- Loss of product
- Loss of profits
- Loss of business opportunities
- Increased financing costs
- Increased operating costs
Because consequential damages may cause significant losses to the breaching party, construction contracts commonly include waivers of consequential damages. The following is an example of a consequential damages waiver:
18.2 Consequential Damages Waiver. IN NO EVENT WILL EITHER PARTY BE LIABLE TO THE OTHER PARTY FOR ANY INDIRECT, SPECIAL, CONSEQUENTIAL, PUNITIVE OR EXEMPLARY DAMAGES (INCLUDING, BUT NOT LIMITED TO, DAMAGES BASED UPON LOST PROFITS, BUSINESS INTERRUPTION, LOST BUSINESS, OR LOST SAVINGS (EXCEPT THAT IN CASE OF BREACH BY CUSTOMER, BRAMMER CAN RECOVER ITS LOST PROFITS UNDER THIS AGREEMENT THAT BRAMMER LOST AS A RESULT OF THE CONTRACT NOT BEING FULLY PERFORMED)) FOR ANY ACTS OR FAILURE TO ACT UNDER THIS AGREEMENT, EVEN IF IT HAS BEEN ADVISED OF THEIR POSSIBLE EXISTENCE.18
4.2 METHODS FOR CALCULATING DELAY DAMAGES
When calculating delay damages, it is important to understand the differences among the various cost components discussed in Section 4.1.2 above. In the case of a contractor experiencing delay by no fault of its own, certain cost components may comprise an excusable, compensable delay claim. For an owner, delay damages are typically LDs or actual delay damages.
Figure 4-1 below shows the relationship between owner-caused delays and contractor-caused delays and the resultant delay damages.
Figure 4-1: Relationship between Owner-Caused and Contractor-Caused Delays
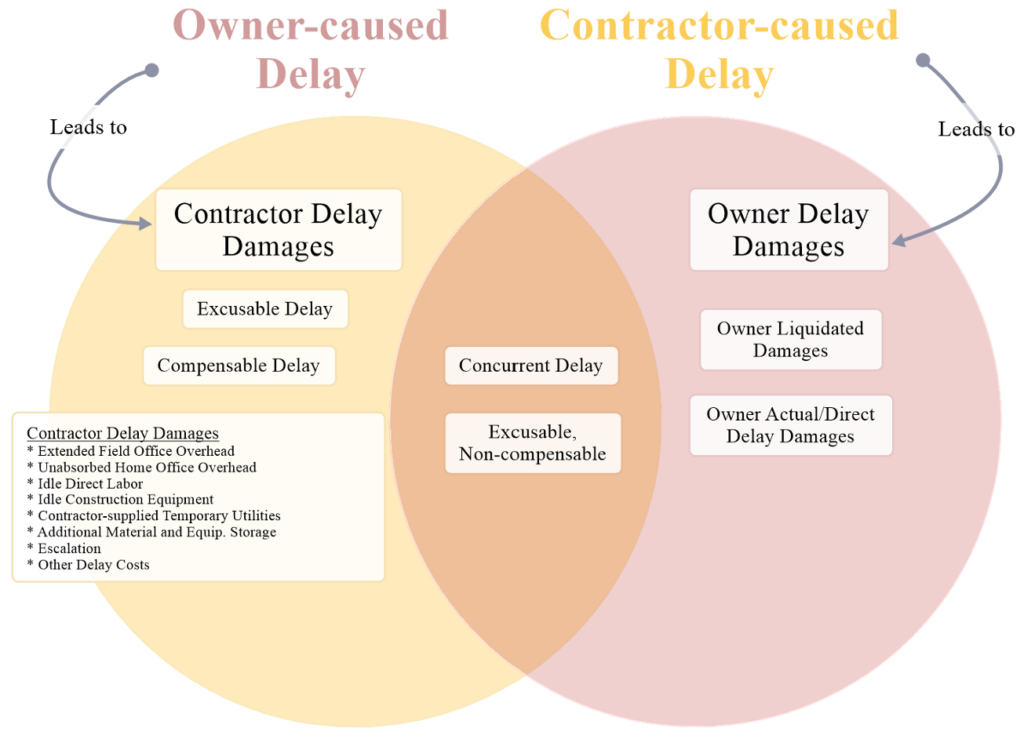
4.2.1 Owner Delay Damages
When a contractor delays a project, the owner may be able to recover delay damages by LDs or actual/direct delay damages, but typically not both.
4.2.1.1 Owner-Assessed Liquidated Damages
When a contractor causes delay and no concurrent delay is established, the owner may be entitled to assess LDs as set forth in the contract. A typical LDs clause may look like the following:
Delay Liquidated Damages. If substantial completion of the liquefaction train occurs after the guaranteed substantial completion date, Bechtel will pay CCL delay liquidated damages at the applicable daily rate as defined in the EPC Contract (T3) until substantial completion of the liquefaction train occurs; provided that, if substantial completion occurs within an initial grace period following the guaranteed substantial completion, no delay liquidated damages would be owed.19
For example, assuming the LDs daily rate in the above excerpt is $50,000 per day, a calculation of delay damages for a delay period of 30 days would be:
30 days × $50,000/day = $1,500,000 as delay damages paid to the owner
4.2.1.2 Owner Actual (Direct) Delay Damages
If a contract does not set forth liquidated damages, and the project incurs a contractor-caused delay, the owner may be entitled to seek actual damages. Although there is no formula or standard method for calculating actual delay damages that an owner incurs for contractor-caused delay, below are typical examples of owner costs from a delayed project:
- Additional project management personnel, consultants, and engineering costs
- Additional site offices costs
- Additional administrative personnel costs
- Other additional costs
For example, assuming the additional daily costs for the items listed above is $80,000 per day on average, a calculation of delay damages for a delay period of 30 days would be:
30 days × $80,000/day = $2,400,000 as delay damages paid to the owner
4.2.2 Contractor Delay Damages
As discussed in Section 4.1.2 above, delay typically impacts several contractor cost types. Below are generally accepted methods for calculating contractor delay damages for each cost type.
4.2.2.1 Extended Field Office Overhead
The first step in calculating extended field office overhead (FOOH) costs is to determine when a delay occurred in relation to the overall duration of the project. Far too often, contractors establish one daily rate for FOOH and use it to calculate the cost for extended FOOH. However, the daily rate for FOOH costs typically changes over time, following a curve in conjunction with planned progress and direct labor levels. FOOH costs gradually build up during the beginning of a project, level off at peak labor levels when the project is in full swing, and decrease as the project nears completion.
Therefore, to determine the daily rate to apply to a project delay, it may be appropriate to identify phases of field overhead rates. Typically, there are a minimum of three phases: 1) ramp-up phase, 2) construction phase, and 3) ramp-down phase. Depending on the size and duration of the project, there may be additional phases where FOOH differs from other phases.
If delay occurs during the height of the construction phase (i.e., peak direct labor force), the FOOH daily rate would be greater than the rate during the ramp-up or ramp-down phase. Thus, the resulting extended FOOH costs would be greater during the peak construction phase than they would be if the delay occurred during the beginning or ending phase of the project.
When developing the daily rate for FOOH, a contractor should include applicable cost accounts allocated as FOOH. Section 4.1.2 above includes many of the typical cost accounts. For example, the contractor should divide the monthly cost for field office facilities into a daily rate. Similar calculations should be performed for each of the applicable FOOH cost accounts. However, there may be certain FOOH cost accounts that the contractor should exclude from FOOH daily rate calculation. For example, project mobilization costs are typically coded as FOOH costs, but the contractor should exclude these and other one-time costs from the pool of time-related costs that are subject to prolongation claims.
As an example, assuming the total daily rate for the applicable cost accounts under FOOH is $20,000 per day, a calculation of delay damages for a delay period of 30 days would be:
30 days × $20,000/day = $600,000 as delay damages calculated by the contractor
4.2.2.2 Unabsorbed Home Office Overhead
Law Insider provides this definition of a contractor’s home office overhead (HOOH) costs:
Home Office Overhead means that portion of Contractor business costs necessary to operate the business entity that are not specifically related to the Work but are properly allocable to this Contract. Such costs include, but are not limited to, those associated with office and office personnel salaries and related payroll taxes and benefits; costs of office occupancy and maintenance, all supporting services (such as utilities, office equipment, computers, and similar items) related to the home office function; business taxes and licenses; and all such other costs necessary to operate the business entity.20
Unabsorbed home office overhead costs due to project delay could be calculated similarly to extended field office overhead. However, determining all HOOH costs associated with a single project may be difficult, especially if the contractor’s organization has multiple projects active simultaneously. While several industry studies exist, the Eichleay formula is a widely used method for calculating HOOH costs. The Eichleay formula first appeared in Eichleay Corp. (1960) when Eichleay, the contractor, sought to recover damages from a U.S. government-caused delay. The original Eichleay formula consisted of three calculations shown in the equations below.
Total Contract Billings / Total Company Billings for Contract Period × Total Overhead for Contract Period = Allocable Overhead
Allocable Overhead / Days of Performance = Daily Unabsorbed HOOH Rate
Daily Unabsorbed HOOH Rate × Number of Days of Delay = Unabsorbed HOOH Amount
Although the above equations provide a reasonable approach to calculating unabsorbed HOOH costs due to project delays, the Eichleay formula is not without shortfalls. For example, it presumes that any delays affect overall project costs uniformly over the duration of a project. As previously discussed, project costs are not linear, and therefore, the application of HOOH costs using the Eichleay formula is not always fair and accurate.
Nonetheless, the Eichleay formula remains frequently used and accepted in court cases to this day. In their scholarly paper “Guidelines for Recovering Home Office Overhead Costs with Emphasis on the Eichleay Formula,” Dr. William Ibbs and Benjamin T. Davis provide criteria for applying the formula. The paper states:
Based on a review of court cases, the following criteria were created for when the Eichleay formula can be applied to recover unabsorbed HOOH. They are ordered by precedence. All seven conditions must be met for Eichleay to apply.
- The Eichleay formula is used for primarily prime contractor versus owner disputes. Subcontractor and prime contractor disputes are discussed later in this paper;
- Unabsorbed HOOH caused by force majeure events cannot be recovered;
- The Eichleay formula is only applicable to HOOH when the project’s schedule is extended past the contract performance period;
- Any “wholly unrealistic figure” produced by the Eichleay formula will be disallowed;
- Oral agreements may be enforceable regardless of a written contractual agreement stating otherwise;
- Contractual agreements are upheld regardless of actual damages; and
- Inability to calculate actual damages warrants the use of the Eichleay formula.21
Figure 4-2 below captures the HOOH recovery formula criteria in a flowchart.
Figure 4-2: Flowchart for Navigating Unabsorbed HOOH Recovery22
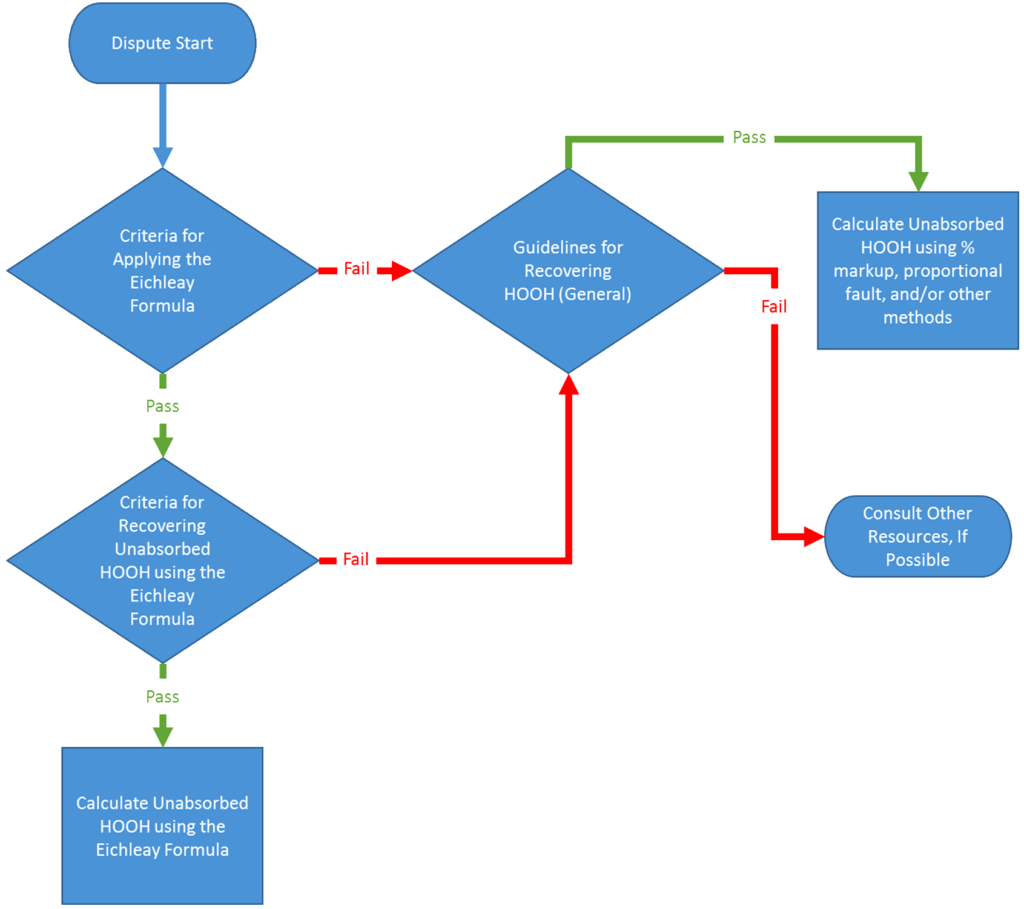
The figure above provides a guideline for contractors to determine if the Eichleay formula should be used. When calculating the effects of unabsorbed home office costs, contractors should consider the Eichleay formula unless a fair and equitable daily rate is agreed on or the rate is defined in the contract.
An example of using the Eichleay formula for a hypothetical project that has experienced owner-caused delay is shown below.
Actual contractor billings for delayed project = $500,000
Total contractor company billings for the period = $3,000,000
Total home office overhead costs for contractor company = $75,000
$500,000 / $3,000,000 × $75,000 = $12,500 (HOOH allocable to delayed project)
Days of contractor work through delay period = 90 days
$12,500 / 90 days = $138.89 (Daily rate contract home office overhead)
Total days of delay on the project = 30 days
$138.89/day × 30 days = $4,166.67 (Unabsorbed expenses
for additional HOOH costs due to delay)
4.2.2.3 Idle Direct Labor
Contractors typically include additional costs for direct or craft labor in disruption claims rather than delay claims. However, delays sometimes lead to the idleness of a direct labor force that the contractor cannot reassign to other work or remove from the project. If the contractor can tie these circumstances to a delay, it may properly include the costs in a delay claim.
When calculating the delay damages, it should be determined if the direct labor had to remain on site but could not work due to delay. Contractors typically maintain daily labor force and payroll records for their direct labor personnel and document idle time in daily logs and/or timesheets. The contractor should compile these records for the duration of the delay period, total the actual payroll costs for the idle direct labor force during this time, and include this sum in the overall damages calculation.
4.2.2.4 Idle and Prolonged Construction Equipment
On a delayed and disrupted project, several factors can complicate the pricing of additional costs for equipment. First, certain equipment, such as welding rigs, are more task related than time related, and therefore, the additional costs are more closely tied to craft labor productivity than time. Time and overall project duration typically drive the costs of other equipment, such as tower cranes. Second, delay may cause some equipment to sit idle while other equipment is utilized but still on the project longer than planned. Third, hourly, daily, weekly, or monthly equipment rates may be derived from several sources, including rates set out in the contract, estimated ownership costs, rental costs, and other industry sources such as blue book values. Moreover, the contract may include separate rates for idle versus working equipment. Finally, equipment costs can be spread across many different cost accounts in the contractor’s records, and the costs may be established using internal methods that may not align with, for example, the rates stipulated in the contract. For example, a contractor may allocate its monthly ownership costs across several projects based on the equipment assigned to those projects, but such allocation may not account for specific contract rates or how the equipment is being utilized on a particular project.
Given these complications, the contractor must clearly establish, often for each type or piece of equipment, the basis for the pricing and the underlying causes for the increased costs. As with idle direct labor costs, the contractor should document and compile costs for idle construction equipment for the duration of the delay period. The contractor should also add ownership and rental costs, and it should assess other project-based equipment for prolongation costs. For example, eligible costs typically include those for site supervision-assigned vehicles, certain large cranes, and other equipment.
4.2.2.5 Contractor-Supplied Temporary Utilities
If the owner causes compensable delay to project completion, and the contractor is required to continue to provide and pay for temporary utilities, then the contractor may be entitled to recover its additional costs for these utilities. Temporary utilities can include but are not limited to electric power, natural gas, drinking water, plant water, nitrogen, hydrogen, other similar gases, etc.
For example, if the daily cost of these temporary utilities is $10,000, and the owner delays the project by 30 days, then the cost of temporary utilities would be:
30 days compensable delay × $10,000 per day = $300,000
4.2.2.6 Equipment Preservation
If a long, owner-caused delay requires the contractor to protect the equipment that it has installed from water damage, corrosion, contamination, cold temperatures, etc., then the costs of this protection may be recoverable. These costs include material costs to protect the equipment, installation of equipment preservation materials, labor costs to maintain the equipment, and labor costs to restore the equipment after construction resumes. If the contractor maintains supportable documentation for all costs associated with equipment preservation and maintenance, it may have a supportable claim for recovery of these costs.
4.2.2.7 Additional Equipment and Material Storage
Because equipment and material storage costs are time dependent, an analyst can determine delay damages using project cost records. The contractor typically pays the costs for facilities required for storing equipment and materials prior to their installation. If a project is delayed and the contractor incurs additional costs for extended equipment and material storage, those costs may be recoverable as delay damages. Alternatively, if the contractor is delayed and elects to postpone the purchase of materials, the differential between pre-delay and post-delay costs of materials may be recoverable.
Materials used for construction projects are typically stored in onsite or offsite warehousing facilities. Although warehousing may be considered a field office overhead cost, delineating costs associated with material storage increases the likelihood of recovering them.
Below is a simple example for calculating additional material storage delay damages:
Monthly cost for warehousing = $50,000 per month
Daily warehousing cost = $50,000 / 30 days per month = $1,666.67 per day
Additional material storage costs = 30 days × $1,666.67 per day = $50,000
4.2.2.8 Escalation
Construction contracts often assign the contractor the risk for increases in labor, equipment, and material costs during the contracted timeframe of the project. However, if the contractor is delayed through no fault of its own, the costs for escalation resulting from the extended project duration may be recoverable.
Damages resulting from escalation due to delay can be determined by calculating the difference between the cost of labor, equipment, or materials that the contractor would have incurred had there been no project delay and the actual cost of the labor, equipment, or materials resulting from performing the work later than originally planned. This calculation requires the contractor to provide supporting documentation for its planned and actual labor, construction equipment, and purchased materials costs.
An example of an escalation calculation due to excusable, compensable delay is as follows:
Project costs without any delay:
Labor costs = $5,000,000
Construction equipment = $2,000,000
Purchased materials = $3,000,000
Actual project costs after project delay:
Labor costs = $5,500,000
Construction equipment = $2,500,000
Purchased materials = $3,250,000
The difference between what would have been spent had there been no project delay and the actual costs after project delay equals escalation costs.
Labor escalation: $5,500,000 (actual) – $5,000,000 (planned) = $500,000
Equipment escalation: $2,500,000 (actual) – $2,000,000 (planned) = $500,000
Materials escalation: $3,250,000 (actual) – $3,000,000 (planned) = $250,000
Total escalation costs claimed by the contractor due to owner-caused delay = $1,250,000
4.2.2.9 Other Delay Costs Potentially Recoverable by the Contractor
In the case of a long, owner-caused delay, the contractor may incur additional costs that may be recoverable, including but not limited to:
- Extended equipment warranty costs
- Extended construction insurance costs
- Extended bonding costs
5. SUMMARY
When a construction project experiences a delay, either the owner or the contractor typically incurs delay damages. An analyst can determine the delay to be:
- Critical or non-critical
- Concurrent or non-concurrent
- Excusable or non-excusable
- Compensable or non-compensable
When an owner-caused delay falls on the then-current critical path and is non-concurrent with other contractor-caused delays, the contractor may be entitled to seek delay damages. Conversely, if a contractor-caused delay is not concurrent with owner-caused delays, the owner may be entitled to assess liquidated damages or actual delay damages.
The types of delay damages are: (1) liquidated damages (LDs), (2) actual or direct delay damages, and (3) consequential damages. Parties typically establish LDs in the contract prior to execution of the work, calculating the LDs as a fair representation of the owner’s additional costs resulting from contractor-caused delay. Absent an LD provision in the contract, the owner may seek its actual delay damages. If the owner delays the contractor’s work, the contractor may calculate its actual delay damages. Consequential damages are often waived in construction contracts or are considered in the owner’s LDs.
Contractor damages due to owner-caused delay can include, but are not limited to, the following cost components:
- Extended field office overhead costs
- Unabsorbed home office overhead costs
- Idle direct labor
- Idle and/or prolonged construction equipment
- Temporary utilities supplied by the contractor
- Equipment preservation
- Additional material storage
- Escalation
- Other delay costs
The contractor typically compiles delay damages from its actual costs during the period of owner-caused delay. It calculates extended field office overhead costs by determining the daily rate of expense that would be incurred during the delay period and multiplying by the number of days of delay. The contractor could determine unabsorbed home office overhead costs similarly, but due to the nature of home office costs, contractors often use the Eichleay formula or other industry formulae. Costs related to idle direct labor, idle construction equipment, and additional material storage are compiled from actual contractor costs from direct labor payroll, paid invoices and/or internal costs for rented or owned construction equipment, and paid invoices or internal cost accruals for additional storage. Escalation costs due to owner-caused delay can be determined by calculating the difference between the cost of labor, equipment, or materials that the contractor would have incurred had there been no project delay and the actual cost of the labor, equipment, or materials resulting from performing the work later than originally planned.
About the Author
Garrett J. Brown is a Principal with Long International and has 30 years of progressive work experience related to various aspects of engineering, procurement, and construction. Key work experience includes planning and team management; project cost and schedule controls; change order management, including change order pricing and resolution; subcontract management; and arbitration/litigation experience related to construction claims. Mr. Brown also has expertise in the development and implementation of process improvements to increase business unit and project workflow efficiency. He has performed schedule delay and loss of productivity analyses and has evaluated change orders for scope growth and project time and cost impacts. His project experience includes combined cycle power plants, oil refineries, petrochemical facilities, materials handling amenities, coke handling facilities, water storage facilities, and aboveground storage tanks. Mr. Brown is based in the Kansas City area and can be contacted at gbrown@long-intl.com.
1 Actual damages are also called “direct damages.”
2 The “critical path” is the longest sequence of activities from start to finish that must be completed to ensure a project is finished by a certain date.
3 If an owner delays a contractor or subcontractor on non-critical path work and causes the contractor or subcontractor to incur increased time-related costs, the contractor or subcontractor may be entitled to delay damages.
4 Other schedule quality checks should also be performed. See Ronald J. Rider, “Forensic Schedule Assurance Review: A Vital Step Before Starting a Detailed Schedule Analysis,” https://www.long-intl.com/articles/forensic-schedule-assurance
5 See Richard J. Long, Ronald J. Rider, and Rod C. Carter, “Implementing Time Impact Analyses and Update Impact Analyses on Large, Complex EPC Projects,” https://www.long-intl.com/articles/time-impact-analyses.
6 See Andrew Avalon, “Calculating the As‑Built Critical Path,” https://www.long-intl.com/articles/as-built-critical-path
7 See Richard J. Long, “As-Built But-For Schedule Delay Analysis,” https://www.long-intl.com/articles/as-built-but-for.
8 See AACE International Recommended Practice No. 29R-03, “Forensic Schedule Analysis,” April 25, 2011, MIP 3.1 through 3.5, pp. 41–72 of the pdf.
9 See AACE International Recommended Practice No. 29R-03, “Forensic Schedule Analysis,” April 25, 2011, Section 4.1.A, p. 100 of 136.
10 See SCL Delay and Disruption Protocol, 2nd Edition, February 2017, p. 7.
11 For a more complete discussion of concurrent delay, see Richard J. Long, “Analysis of Concurrent Delay on Construction Claims,” https://www.long-intl.com/articles/concurrent-delay.
12 See Richard J. Long, “As-Built But-For Schedule Delay Analysis,” https://www.long-intl.com/articles/as-built-but-for.
13 See AACE International Recommended Practice No. 10S-90, “Cost Engineering Terminology,” Rev. May 15, 2023, p. 29.
14 See Richard J. Long, “As-Built But-For Schedule Delay Analysis,” https://www.long-intl.com/articles/as-built-but-for.
15 Concurrent delays may be literally concurrent (i.e., they occur at exactly the same time) or functionally concurrent (i.e., they occur during the same time period). Either delay would delay project completion, but because the schedule was not updated on the precise date that the delays occurred, they are called functionally concurrent. See Richard J. Long, “Analysis of Concurrent Delay on Construction Claims,” https://www.long-intl.com/
articles/concurrent-delay.
16 See AACE International Recommended Practice No. 29R-03, “Forensic Schedule Analysis,” April 25, 2011, Figure No. 15 – Net Effect of Potential Concurrent Delay Combinations, p. 113 of 136
17 See Jeremy Wegener and Chad Caplan, “Liquidated Damages – The Basics,” Under Construction, ABA Forum on Construction Law, September 20, 2021, https://www.americanbar.org/groups/construction_industry/publications/
under_construction/2021/summer2021/liquidating_damages.
18 Development and Manufacturing Services Agreement, Freeline Therapeutics Limited and Brammer Bio MA, LLC, https://www.sec.gov/Archives/edgar/data/1810031/000095012320006919/filename3.htm.
19 See Cheniere Corpus Christi Holdings, LLC, Prospectus Supplement No. 1, Dated December 18, 2017, to the Prospectus Dated November 24, 2017, United States Securities and Exchange Commission Form 8-K, https://www.sec.gov/Archives/edgar/data/1693317/000119312517372110/d467315d424b3.htm.
20 See “Home Office Overhead definition,” Law Insider, https://www.lawinsider.com/dictionary/home-office-overhead.
21 See Benjamin T. Davis and William Ibbs, “Guidelines for Recovering Home Office Overhead Costs with Emphasis on the Eichleay Formula,” Journal of Legal Affairs and Dispute Resolution in Engineering and Construction 9, no. 1, February 2017, p. 2, https://ascelibrary.org/doi/10.1061/%28ASCE%29LA.1943-4170.0000201.
Copyright © Long International, Inc.
ADDITIONAL RESOURCES
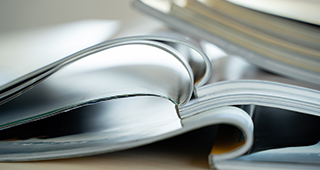
Articles
Articles by our engineering and construction claims experts cover topics ranging from acceleration to why claims occur.
MORE
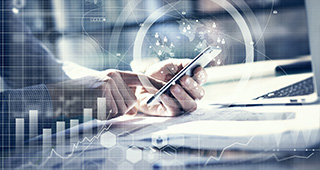
Blog
Discover industry insights on construction disputes and claims, project management, risk analysis, and more.
MORE
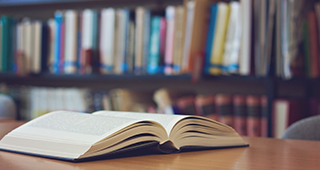
Publications
We are committed to sharing industry knowledge through publication of our books and presentations.
MORE